Validation of BS 7910:2013 and R6 Fracture Assessment Procedures: Summary Report, Including Treatment of Plastic Collapse, Weld Strength Mismatch and Probabilistic Data
By I Hadley, K Kouzoumis and Y J Janin
Industrial Need
TWI, on behalf of its industrial members, is involved in the maintenance and development of three major flaw assessment procedures:
- BS 7910, ‘Guide to methods for assessing the acceptability of flaws in metallic structures’.
- R6, ‘Assessment of integrity of structures containing defects’.
- The joint API/ASME fitness-for-service procedure, ‘Fitness-For-Service (FFS)’, API 579-1/ASME FFS-1.
All three procedures use a similar model assessment of crack-like flaws under static loading (fracture assessment) ie the use of a Failure Assessment Diagram (FAD), on which a Failure Assessment Line (FAL) represents a notional failure surface, ie points inside the FAL are considered safe and those outside are deemed potentially unsafe. There is considerable overlap between the procedures, and information is freely shared between the committees, but there are also some differences in the underlying solutions, for example the equations for stress intensity factor and limit load/reference stress. Consequently, if the same structure is assessed using different assessment procedures, slightly different assessment points may be generated, and it is considered good practice to use a consistent procedure throughout, rather than to mix solutions from different procedures.
Alothough the procedures are based on sound principles, they require validation against full-scale test data and numerical analyses in order to demonstrate that they are safe, user-friendly, practically useful and not excessively conservative. For the purposes of this report, validation involves assessing a large-scale laboratory test that may contain features typical of engineering structures (for example welding residual stress, attachments, structural misalignment), following the principles set out in the appropriate procedure and plotting the results on a FAD. Typically, an artificial flaw is introduced to represent a flaw that could arise from fabrication and/or during service. Because factors such as load to failure, initial flaw size and materials properties (fracture toughness and tensile properties) are known with some precision, the assessment point associated with failure is expected to lie on or outside the FAL.
This validation provides industry with confidence in the assessment procedures, ensuring that structures are safe and cost effective by design and in operation.
Key findings
- The test results presented in this report can be used in a number of ways, including:
- As a reference source for validating existing and future flaw assessment procedures;
- As an indication of areas in which current procedures might need to be modified;
- For teaching material;
- For validation of software.
Example of probabilistic fracture mechanics assessment
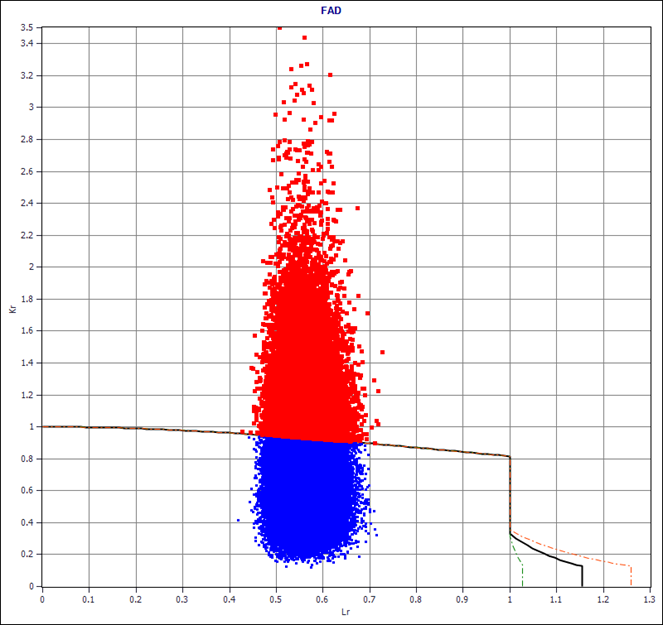