Ultrasonic Monitoring of Electron Beam Welding
By S Majidnia, I Kotropoulou, G Ptaszek, R Sanderson and C Nageswaran
Industrial Need
Electron beam (EB) welding offers significant savings in cost and time for thick-section fabrication. The process achieves a rapid joining rate because the full joint thickness is welded in a single pass. The reduced pressure electron beam welding (RPEBW) variant allows welding to be carried out using basic vacuum systems that can be applied locally to the joint, therefore negating the requirement for large and expensive vacuum chambers that are used for high vacuum EB welding.
EB welding generally produces high quality joints that are used in many applications. However, weld flaws can be generated if the process is not controlled correctly. Inspections are conducted after the component has been welded and removed from the welding environment. If any flaws are identified, there will be a need for weld repair using EB welding - ie the welding process will need to be performed again, which will be time consuming and costly.
Due to this challenge, in-process real-time monitoring techniques that can be implemented during welding are required. In this report, potential inspection techniques are considered and the development of the selected technique for real-time monitoring of RPEBW is presented.
Key findings
- Ultrasonic testing (UT) techniques can be effectively used to monitor the reduced pressure electron beam welding (RPEBW) process because the elevated temperature conditions are sufficiently low for the adverse effects due to temperature on UT to be tolerable for the monitoring purpose.
- The UT system must be placed in a position where it can tolerate the local surface temperature. For the thick component investigated, the UT probe must be at least 100mm from the joint, trailing behind the RPEBW system.
- Finite element analysis (FEA) can simulate the welding process, predict the resultant thermal profiles and use known sound velocities at different temperatures to optimise the UT system, including setting the distances from the joint and the RPEBW system.
- A prototype using phased array ultrasonic testing (PAUT) was successfully designed, taking into account the findings of the analytical and experimental investigations. The PAUT system can generate ultrasonic beams at different angles to interrogate the joint from a fixed position suitably far from the joint.
- The prototype PAUT system is expected to be sensitive to typical flaws that may emerge during the welding process, in particular small volumetric porosity in the so-called slope-in/slope-out region of an electron beam weld. The monitoring system is not optimised for fabrication stage weld inspection, but could be used to detect flaws in the joint once it cools down to ambient conditions; acceptance of the joint where flaws are found may require additional inspections, optimised for characterising flaws.
Temperatures at two different distances behind the gun and at different distances from the weld centreline
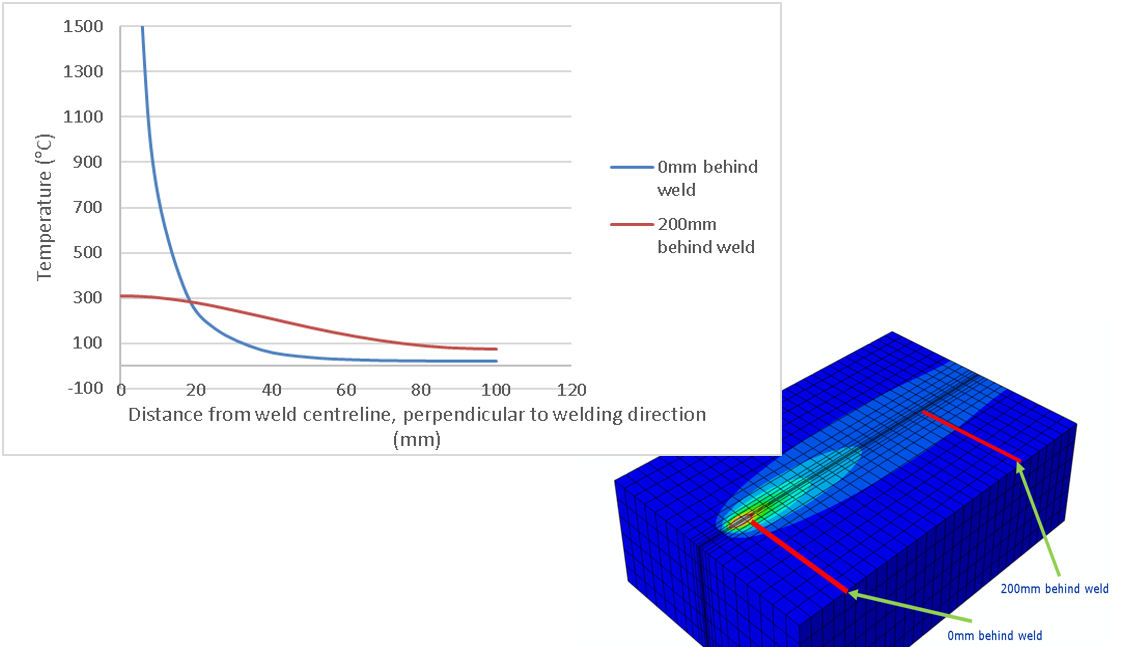
Experimental measurement of ultrasound velocity and attenuation. The steel block is heated at one end by a heating pad, with thermocouples used to log the temperature. The dotted red circle shows the ultrasonic probe
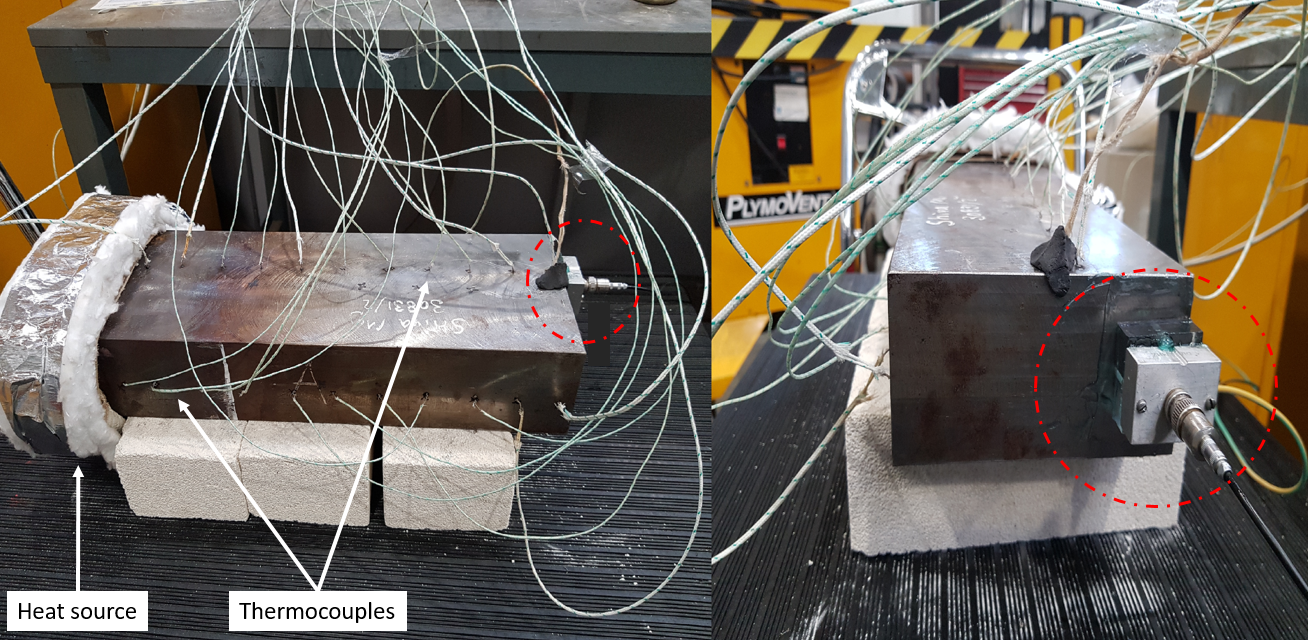