Ultimate - Leverage Funding Support
TWI Industrial Member Report 1175-2023 [pdf / 9,855 KB]
By Necdet Capar
Industrial Need
Due to stringent fuel economy regulations, automotive and aerospace companies are increasingly looking to reduce the weight of structures, through the use of dissimilar materials.
Joining dissimilar materials can be challenging and often beyond the capacity of conventional automated production processes. Currently, most challenging multi-materials assemblies are mechanically fastened and/or adhesive bonded. Limitations associated to using these two techniques include extra weight, cost and durability issues. These drawbacks limit the adoption of more advanced multi-material designs and reduce the potential benefits such optimised designs could achieve.
Consequently, there is a clear need for new, flexible, cost-effective and rapid methods for joining dissimilar materials, capable of meeting industry performance and manufacturing demands.
Key Findings
- Welding development on the spray coated CFRP samples was challenging due to delamination and cracking of the coated layer, which is mainly originating from CTE mismatch. In an effort to support project partners (in complementary funded 33032 Ultimate Project), It was demonstrated by TWI that even distribution of resin on the composite prepreg surface is critical to achieve void free homogenous coated layers.
- It was much more challenging to achieve a successful coating thickness and regime suitable for weld on CFRP substrates (max. coating thickness 150 µm) compared to metal subsrates (up to 1000 µm).
- As a result of these challenges, the demonstration for automotive and aerospace industry was completed successfully by using an intermediate layer in order to support coated layer.
- Fillet and overlap welding trials on aluminium materials (5XXX-6XXX ) series proved use of beam oscillation to make an improvement on porosity formation risks.
- The spray-coated layers have tendency to form rigorous porosity by its nature, a pre-heating before the main welding process or double pass of welding wire helps reducing the porosity. This approach can also be utilised in welding of high porosity casted materials.
- For titanium welding, it was found to be challenging to use panpipe gas shielding kits in narrow operating envelopes. The gas shielding too could be eliminated and it can be transferred on to the welding fixture itself by having air channels incorporated into a bespoke fixture design.
- IDM was successful for penetration depth reading in thick 1-2mm steels and 0.5mm titanium materials, however it was found to be more challenging on 1-2 mm Aluminium due to the dynamic keyhole characteristics.
- One of the main challenges with IDM for a consistent penetration depth tracking was 2D beam alignment during the calibration, where the imaging beam was aligned concentrically from top of the keyhole as the system does not allow the user to select a specific point depth from the keyhole 3D scanned topography. The imaging beam was delivered downstream through fixed optics of IDM module on the welding head and the system does not have capacity to apply an independent scanning pattern to acuqiredata from a surface area.
Impact
- Performed preliminary evaluation of the different laser approaches considered for laser welding on metal-to-metal samples, helped to achieve an understanding for the capabilities of the technology in terms of partially penetrated welds.
- Preliminary assessment of the IDM keyhole monitoring system during welding processes was completed. A public keynote will be presented at ILAS 2023 event.
- Welds were characterised through a series of destructive and non-destructive testing and the results were compared to understand joining performance as well as IDM monitoring technology capabilities.
- A demonstration for automotive and aerospace with down-selected final parameters performed. The outcomes of these demonstrations will lead to the new projects to improve dissimilar joining capabilities in related industries.
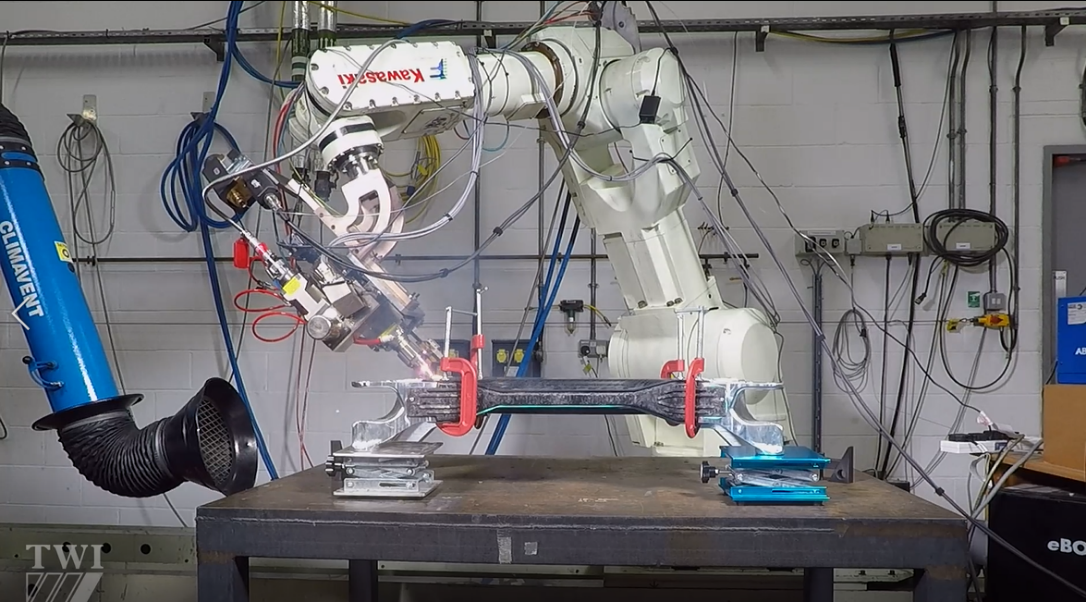
Automotive demonstration joining Al sub frame to CFRP panels.
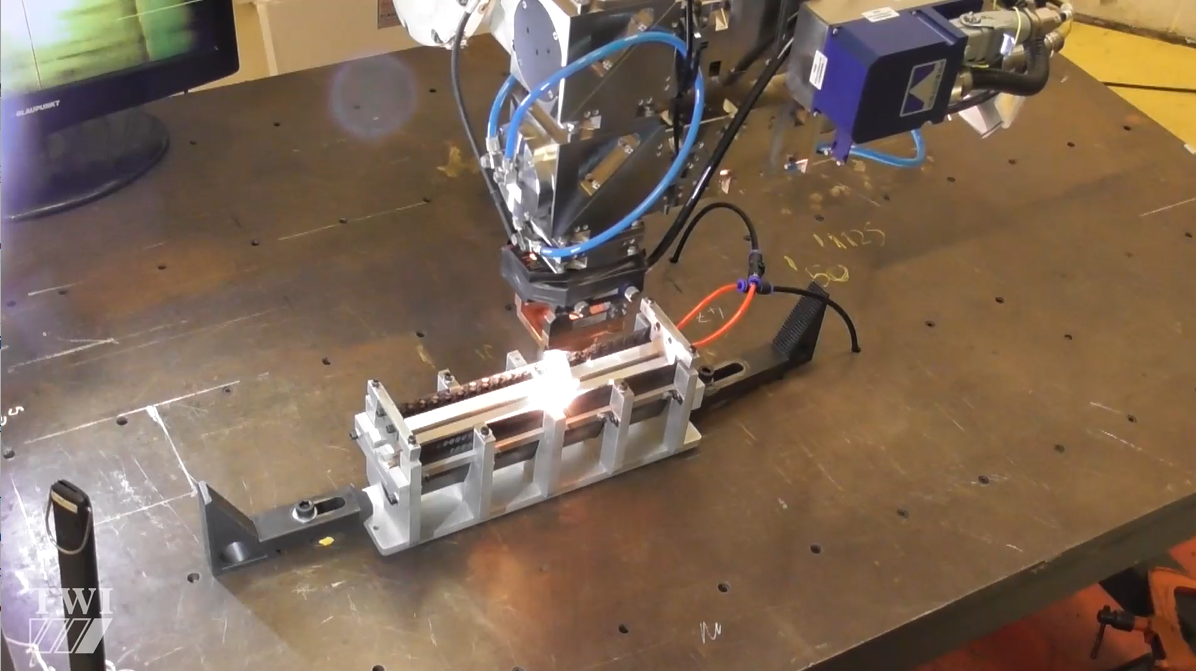
Aerospace demonstration joining Ti plate to CFRP panel.