Effect of Welding Parameters on the Integrity and Structure of Butt Fusion Welds in Polyethylene Pipes
By M Troughton and M Shaheer
Industrial Need
There are a number of different butt fusion (BF) welding procedures for polyethylene (PE) pipes specified around the world. However, some of these are significantly different, especially in the welding pressures used. The main reason for such differences is that different mechanical test methods were used to optimise the welding parameters. In the UK water industry the welds were assessed using a short-term tensile test on specimens cut from the joint, whereas in Germany they were assessed using a bend test and specimen creep rupture test. In the US, the welds were assessed using a tensile impact test on specimens and hydrostatic pressure testing of the welded pipe.
For this reason there is a need to understand the factors that can influence the integrity of BF joints and, based on these results, determine the welding procedure that produces BF joints with better integrity.
Key findings
- All of the welds made in accordance with all of the six welding procedures examined in this project passed all of the three standard short-term specimen tests (waisted tensile test, guided side bend test and tensile impact test). However, the guided side bend test and the tensile impact test failed to differentiate between the different welding procedures because, in these tests, failure did not occur at the weld.
- This study therefore suggests that the most appropriate test for assessing the short-term performance of BF joints in PE pipes is the waisted tensile test, which forces failure to occur at the weld. Although all of the welds produced failed in a ductile manner, this test indicated that the welds made to DVS 2207-1 had a slightly lower energy to break the weld than the welds made to the other welding procedures. Since the weld beads were left intact during testing, this may have been due to the smaller weld beads produced using this procedure.
- The results of long term creep rupture tests indicated that the welds made to WIS 4-32-08 and DVS 2207-1 had significantly longer (more than double) average times to failure than the welds made using higher interface pressures. However, it should be noted that these results are based on only two tests per welding procedure.
- For the welding procedures studied, there is no correlation between short-term and long-term performance of BF joints in PE pipes. However, taking into account both the short-term and long-term performance, joints made to WIS 4-32-08 have the highest mechanical integrity.
- Nanoindentation is a valuable tool in characterising and mapping the variation in the material properties across BF welds in PE pipe. The nanoindentation results showed that BF welds have a melt zone, where the material was melted during the welding operation and also have an HAZ, where the material was annealed, resulting in an increase in mechanical properties.
Waisted tensile test specimen.
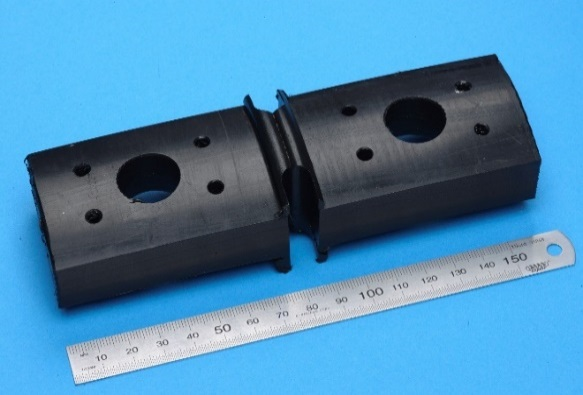
Failure in a typical waisted tensile test specimen showing ductile fracture surfaces at the weld.
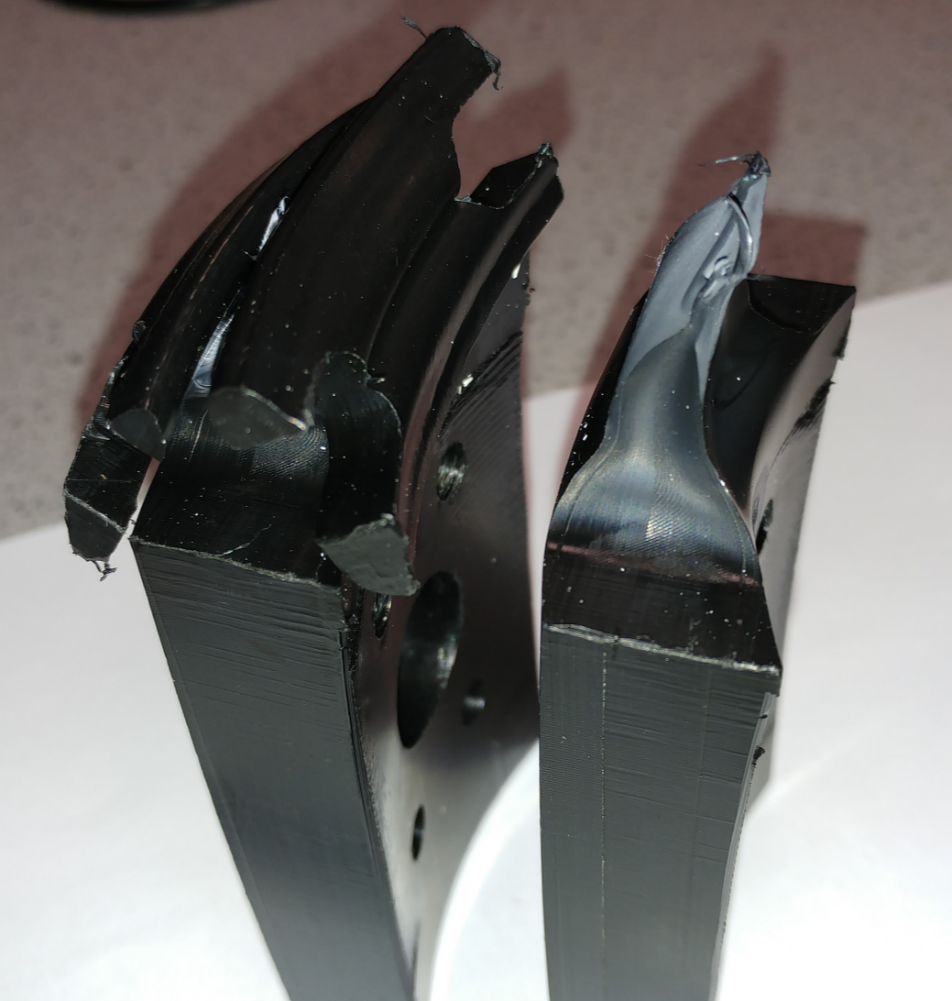