Monitoring Corrosion of Marine Steels and Environments using Acoustic Emission
TWI Industrial Member Report 1179-2023 [pdf / 4,551 KB]
By Rodrigo Rueda CEng MWeldI
Industrial Need
Corrosion detection and monitoring is an important part of any survey of a marine structure or vessel. On ships, they are commonly undertaken every 5 years. The survey is carried out principally by means of Close-up Visual Inspection (CVI), which is time consuming, expensive and is subject to human error. Current inspection and Non-Destructive Testing (NDT) strategies, focus inspection on areas with previously noted problems and rely on inspector’s knowledge from similar vessels, namely a CAIP - Critical Area Inspection Plan. The CAIP approach means that unanticipated defects are less likely to be detected. Conversely, employing an inspection strategy providing equal attention to all regions of a structure is impractical and not economic.
Additionally on ships, special service surveys mitigate identified corrosion problems by reapplying protective coatings. Although coating protection is effective in dealing with corrosion, it creates challenges for future inspection performance and appears to have a mixed impact on probability of detection. Inspectors have reported that the scaling and corrosion that accompany coating breakdown could hide crack damage. Furthermore, coating protection is prone to degradation at welds, which may promote localised weld metal corrosion in addition to the potential for preferential weld metal corrosion. In optimising maintenance strategies, it is appropriate that consideration is given to the likelihood of corrosion rates at weldments being higher than the anticipated rate for parent material.
Therefore, there is a desire to supplement marine inspections with monitoring solutions that will increase the probability of detecting and monitoring corrosion, particularly around welds. Firstly, this may assist inspection by giving an early indication of the location of newly corroded areas at weldments. Secondly, it may assist with continuously assessing the condition of already identified corroded areas. Finally, monitoring may identify non-visible pits or cracks underneath protective coatings. By use of effective monitoring, instances of unexpected damage identified at inspection may be reduced and the length of time between service intervals may be extended. This will significantly reduce operating costs while also ensuring structural integrity.
In this regard, Acoustic Emission (AE) testing is a promising monitoring technique, potentially capable of detecting and monitoring pitting/crevice corrosion initiation and subsequent fatigue crack propagation, including spatial localisation. AE from plastic deformation ahead of a crack is detectable, as is physical crack extension. Subject to development of robust procedures, AE techniques could provide advance warning of active corrosion (or cracking) before it can be detected by other methods.
Key Findings
- HCL reactions were effervescent and modified only the superficial properties of the sample without inducing corrosion damage. As a result, AE detection and localisation of corrosion was not always achieved using this method.
- Images of localised areas of corrosion made by Phased array ultrasonic tests and Alicona scans were similar.
- Highest localisation accuracy of AE events were obtained using the shear wave velocity (3200 m/s) instead of compressional wave velocity (5950 m/s) for 6mm thick steel plates.
- Two groups of burst type signals were identified;
- Group 1 containing high frequencies and coming from a corrosion process.
- Group 2 not containing high frequencies and coming from unknown sources.
- For the localisation of AE sources, the Akaike Information Criterion (AIC) time picking algorithm provided enhanced results compared to the traditional threshold crossing method.
- A frequency based filter was proposed and verified in order to identify signals from free and accelerated corrosion.
- Signals identified from corrosion are typically up to 2500 microseconds long and up to 70dB peak amplitude.
- An AE data processing structure was validated for detecting, localising and identifying corrosion.
- AE signal duration and peak amplitude do not appear to increase with increased corrosion damage as initially expected. Therefore assessing the corrosion damage extent via these AE features is not possible.
- Instead, AE activity is a more suitable parameter for assessing corrosion severity, as it correlates with initial thickness loss and current density.
Impact
AE testing has been used routinely for many years in screening the floors of storage tanks for corrosion activity, but the results provide very little by way of quantifiable information as to the nature, extent and depth of the corrosion. AE testing has therefore always had to be supplemented with other NDT methods, namely ultrasonic and electro-magnetic methods, to provide this information. AE test results that provide quantifiable information about corrosion would therefore be of considerable economic benefit, especially in marine applications. This work has provided evidence of possible AE signal analysis methods for both eliminating noise, which is a constant problem in AE testing, and quantifying the corrosion. The evidence has come from analysing features in the AE signals from corrosion created artificially in the laboratory. These have included amplitude, number of counts per signal, duration and frequency content. Moreover a more accurate AE source location algorithm was introduced, which could be a useful addition to the standard localisation processors used in current AE testing instruments.
Evidence for qualifying AE test procedures that could be used to monitor corrosion in marine structures will require extending the work to cover much larger areas, where the effects of AE signal attenuation and dispersion could be accommodated. Various methods for creating corrosion artificially in the laboratory have been compared, some of which could be adapted for use on large structures.
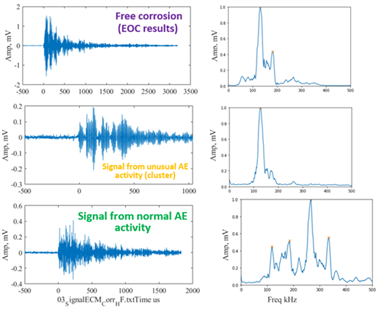
Laboratory corrosion test set-up Typical AE waveforms with frequency spectra