Signal Processing Techniques for Guided Wave Inspection of Buried Pipelines
By R Sanderson and H Nakhli Mahal
Industrial Need
Guided wave testing is a cost-effective means of examining long lengths of pipes for detection of metal loss defects occurring in service, usually from corrosion. The technique is particularly suited to the oil and gas industry where long lengths of largely uninterrupted pipeline exist. Guided waves have inherently low attenuation characteristics compared with the ‘bulk’ wave modes used for conventional ultrasonic testing, so that test ranges in excess of 100m are possible in a bare metallic pipe. However, many pipelines are buried in the ground for safety or aesthetic reasons and in such cases non-metallic coatings are widely used to protection the pipe from corrosion.
The presence of external coatings, which are often viscoelastic in nature, is known to reduce the test range due to absorption of the sound energy into the coating. For example, an epoxy coating can reduce the inspection range to around 50m and bitumen further still to less than 25m, depending on the thickness and properties of the coating (Alleyne et al, 2001). Furthermore, the noise level can increase due to imperfections in the bonding conditions between the coating and the pipe, or general corrosion of the pipe. These phenomena all degrade the Signal-to-Noise Ratio (SNR).
It is unworkable to remove coatings over large lengths of pipe so the attenuation cannot be reduced. However, any contribution to SNR enhancement through improved signal processing methods for data collected on coated pipes will increase the capability of guided wave inspection.
Key findings
- The spatial variances method was successful in detecting a relatively small defect (2% cross sectional area loss) in a clear way that can be easily interpreted by a non-expert. However, the current technique showed sensitivity to frequency and also requires a threshold to be set.
- The adaptive filtering technique showed significant improvements over the standard guided wave method in detecting defects at 34kHz. However, above 40kHz there were no significant improvements.
- The spectral matching technique was successful in detecting a relatively small defect (3% cross sectional area loss) in a clear way that can be easily interpreted by a non-expert. However, there was some dependence on frequency observed.
- The low frequency testing technique was predicted to have significant improvements in signal to noise ratio. Even with imperfect transducers simulated, a 1.1% cross sectional area defect was predicted to be clearly detectable. However, this method is yet to be tested experimentally.
- The coded excitation technique was predicted to improve the detection capability over a standard guided wave test. However, this method is yet to be tested experimentally.
Guided wave inspection of a pipeline test loop.
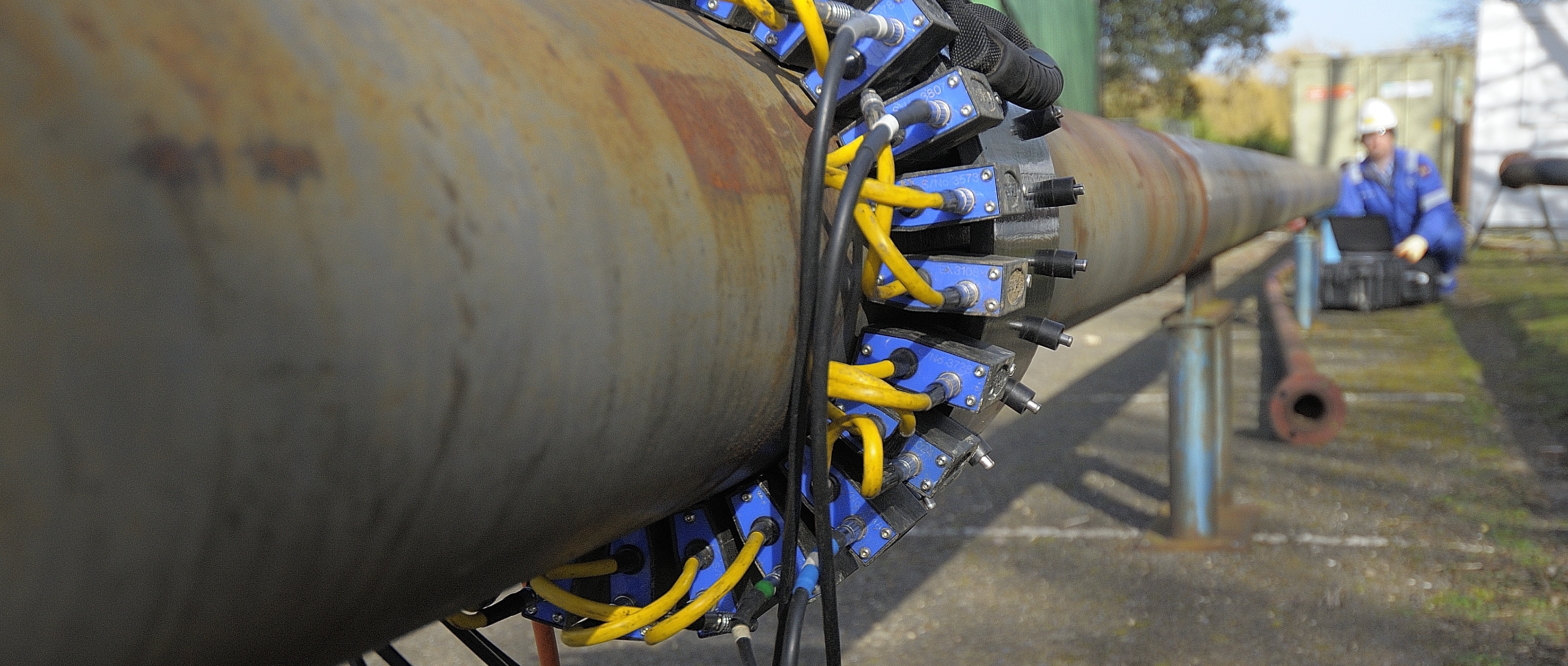