Integrating Diverse Approaches to the Reliability of Engineering Structures: Background and Example Calculations for Failure by Brittle Fracture
By Isabel Hadley
Industrial Need
The probability of failure, POF (the converse of which is ‘reliability’) of engineering components and structures depends on numerous factors, including design, manufacture, inspection, operation and human factors. Reliability may be calculated on the basis of direct observation (what proportion of components fail prematurely?) or theoretical methods (what failure mechanisms are possible, and how likely is it that the conditions for failure will be present during operation?), or some mixture of the two. In this study, two methods are used to estimate probability of failure, using approaches drawn from a range of standards, and comparing the outcomes with situations related to other standards. Relevant documents include BS 7910 (BSI, 2019), R6 (EDF Energy, 2001), API 581 (API, 2016), PD 5500 (BSI, 2018) and EN 13445 (BSI, 2014), and ASME B31.3 (ASME, 2018):
- A ‘top-down’ method based on a mixture of failure statistics and engineering judgement.
- A ‘bottom-up’ method based on fracture mechanics/engineering critical assessment (ECA). Both ‘deterministic’ (using a single characteristic value of each variable) and probabilistic approaches were used, the latter allowing direct estimation of probability of failure.
Key findings
- Two radically different approaches to estimating the reliability of safety-critical engineering components – risk-based inspection (RBI) and probabilistic fracture mechanics (PFM) – have been reviewed, and preliminary example calculations were carried out for two case studies: (1) a pressure vessel and (2) pressure piping.
- Although the origin of the damage factors for brittle fracture in API 581 is somewhat obscure, the method produced logical trends for the cases examined – for example, higher reliability when weldments are post-weld heat-treated and/or have high toughness (low values of T27J).
- For the two cases examined, the relative effects (in terms of reliability) of Charpy test temperature (Case Study 1) and post-weld heat-treatment (PWHT, Case Study 2) were broadly similar, regardless of whether the RBI or PFM approach was used.
- The PFM calculations tend to produce higher estimates of POF than those based on RBI. This is consistent with the fact that the models have not yet been optimised to take account of factors known to be important in the control of brittle fracture (actual occurrence of flaws, reliability of inspection, effects of hydrotest, effects of welding residual stress).
- Whilst the values of POF from the PFM calculations should not be interpreted literally, the results presented here support the concerns expressed about the reliability of certain aspects of ASME B31.3 (PWHT protocol) and EN 13445 (brittle fracture avoidance in as-welded grade 355 steel).
- The ‘simplified’ PFM procedure described in R6 has been used to analyse a set of laboratory data, with a view to quantifying the probability of failure of a wide plate specimen when conventional deterministic ECA is used and the assessment point lies on the failure assessment line (FAL). A value of POF of around 0.14 was calculated, although this will vary on a case-by-case basis depending on details such as the geometry of the flaw and the structure, the loading mode, the way in which the characteristic variables are chosen, and the stress intensity factor/reference stress solutions adopted.
References
API (2016): API RP 581: ‘Risk-based Inspection Methodology’.
ASME (2018): B31.3: ‘Process piping’.
BSI (2014): BS EN 13445-1:2014+A2:2018: ‘Unfired pressure vessels‘.
BSI (2018): PD 5500:2018+A2:2019: ‘Specification for unfired fusion welded pressure vessels’.
BSI (2019): BS 7910:2019: ‘Guide to methods for assessing the acceptability of flaws in metallic structures’.
EDF Energy (2001): R6 - Assessment of the Integrity of Structures Containing Defects: Revision 4, as amended.
Example of a PFM Monte Carlo assessment
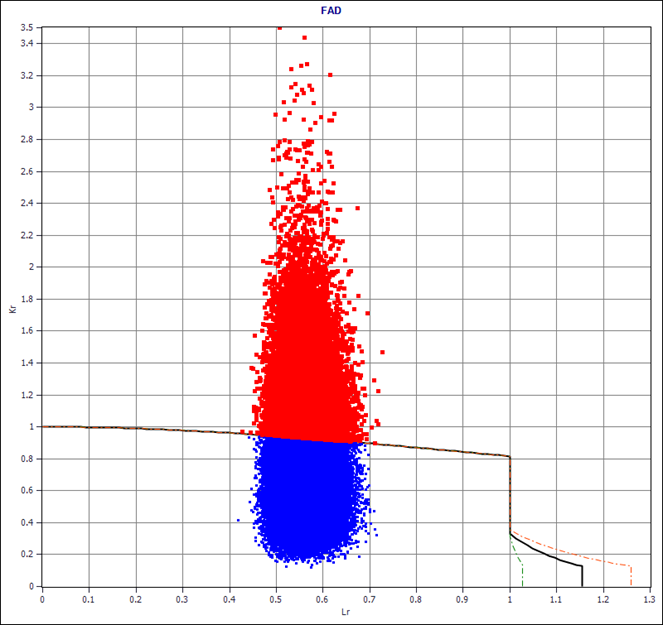
Case Study 2, pressure piping: comparison of RBI and PFM (level 1 and level 2) methods, as-welded (AW) and after PWHT. API 581 baseline figures are also shown for comparison
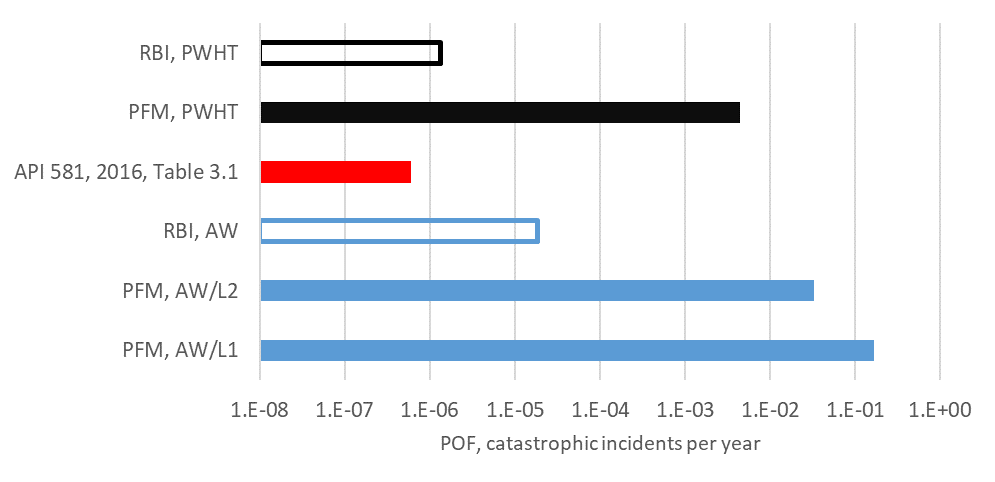