Gas Plasma as a Universal Dry Pre-treatment for Structural Bonding Applications
By D Williams and E Kellar
Industrial Need
One area of the structural adhesive bonding of metals is the pre-treatment stage. This is a critical phase of the joining process as it prepares the surfaces prior to the application of the adhesive with the aim of ensuring that the resulting joint is strong and durable. Currently, many metal pre-treatments use wet chemical based processes to etch the metal surface and modify its chemistry. The largest issue with this practice is that different metals require different types of chemical etchant. When bonding two or more metals, each etchant will have its own set of immersion processes to clean and treat each material; which, in turn, will affect the energy consumption, consumables and time required.
This work explored the use of cold atmospheric plasma (CAP) to treat metals prior to adhesive bonding as a means to move away from wet processing. It focused on two different metals, commonly used in industrial settings i.e. stainless steel (316), and titanium alloy (Ti 6Al 4V). In industry, plasma is predominantly used on metal substrates as a low-pressure batch process, which limits its viability for use on a production line. The plasma treatment investigated in this work operates at ambient pressure and therefore has the potential for use on a production line. The CAP torch also allows for the precise treatment of discrete areas of a structure prior to adhesive bonding, which could be an additional benefit.
Key findings
- A significant increase in dry bond strength, above the untreated state, is realised through the application of CAP as a pre-treatment on both stainless steel and titanium. The CAP treated stainless steel joints performed more than 10% better than oxalic/sulfuric acid etched samples. The performance of CAP treated titanium joints was about 5% lower than chemically etched samples.
- The durability of the bonded joints produced within this project using CAP was similar when considering stainless steel, when used in conjunction with grit blasting, but does not perform as well for titanium.
- The CAP process is less complicated with fewer stages and input/output streams. This may mean there are fewer control systems required and the material wastage for the process is easier to manage.
- CAP has the potential to be a multi-material pre-treatment system that can be scaled up by linear addition of components such as nozzles etc and automated using off-the-shelf equipment.
- It has been shown to offer a less energy intensive route over current ‘wet’ pre-treatment systems in addition to being greener with a low health and safety impact.
- Current studies on the effect of CAP have shown that the treatment window is relatively wide and has relatively low substrate sensitivity, i.e. the technology can treat a range of substrates effectively with only minor modifications to the process parameters.
Cold atmospheric plasma plume.
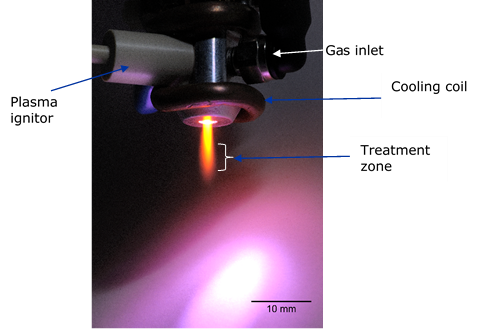