An Assessment of Joining and Recycling Options for Electric Vehicle Battery Pack Manufacture
TWI Industrial Member Report 1192-2024 [pdf / 3,586KB]
By Abbasi Gandhi
PhD, MEng, BEng, CEng, MWeldI
Kandarp Amin and
Necdet Caper
Industrial Need
With the increasing focus on reduction in CO2 emissions, there has been a significant change in the automotive industry with a drive towards electrification and electric vehicles (EVs). European Union targets propose a ban on the sales of new cars with internal combustion engines by 2035 (Reuters, 2021) with the UK targeting the same year, having pushed back from an initial 2030 target (UK Government, 2020; UK Government, 2023). As a result of the current surge in targets for EV manufacturing, significant challenges are being placed on the supply chain in terms of design requirements, joining and manufacturing technologies, inspection, testing and validation and electrical testing.
It is apparent from discussions with TWI Members and at industry events that most manufacturers are under significant pressures to set up suitable battery pack manufacturing facilities with relatively limited process knowledge and understanding of the resultant joints. Whilst laser welding seems to be the preferred technology in the UK, there are a number of other technologies such as wire bonding and micro-TIG, which may also be candidates in certain applications. Therefore, it is very timely to undertake a more specific research activity to benchmark and quantify the different joining technologies and develop quantified data sets for joining battery cell terminals to busbars. To achieve a better understanding of the end-of-life (EOL) cycle of EV batteries, this work also covered review of battery EOL, recycling and reuse, in terms of market, processes and studies/projects.
Key Findings
- Laser welding and ultrasonic welding (including wire bonding) are leading joining methods and have been extensively discussed in literature.
- Other joining methods (resistance welding and TIG) have shown promise however further research and development is required.
- From the literature search, laser welding appears to show the highest joint strength and lowest electrical contact resistance when compared with ultrasonic techniques, however, there was no directly comparable data available.
- There was no universal mechanical, electrical and thermal testing standards available for research and development work on battery joints.
- The wire bonding time was found to be the significant factor followed by the wire bonding force and the bonding current for the pull-out strength of the wire bonded NiP-SS or NiP-Cu to Al joints.
- Over deformation was observed on the bonds when using the best processing parameters identified in the DoE study during wire bonding on NiP-SS dummy cell tabs to Al wires.
- It was challenging to join Al wire to the negative NiP-SS terminals using the parameters identified in the DoE study. Reasons could be the curvature found in this region along with the observed over deformation.
- The results suggested that hook pull-out testing can be used as an alternative to tweezer pull-out testing where the bonded wire length is not long enough for the tweezer gripping.
- The experimental results confirmed the validity of Taguchi method for enhancing the joining performance and the best joining parameters for both joining operations for NiP-SS to Al joints.
- It would appear that recycling has been the strongest area of EOL research, where significant research has been undertaken on different separation methods to extract valuable metals.
Impact
The main objective of the project was to develop a capability for electrical and mechanical testing of battery joints and benchmark different technologies suitable for cell to busbar joining. The results from the study indicate that:
- Taguchi method for DoE study on battery joining process with more than two input factors is recommended. However, if there are only two input factors, the full factorial study is recommended.
- The solid-state wire bonding process for NiP-SS to Al joints is advantageous compared to laser welding, as the lack of molten material means it is less likely to form intermetallic phases. However for NiP-Cu to Al joints, laser (nanosecond pulsed laser) welded joints are stronger compared to wire bonded joints.
- The hook pull-out testing can be used as an alternative to tweezer pull-out testing where the bonded wire length is not long enough for the tweezer gripping.
- Non-destructive electrical 4-probe resistance method can provide good indication on joint strength if destructive mechanical pull-out testing is not feasible.
- Implementing a cost-effective and fully automated and innovative disassembly solution for both the battery packs and the cells themselves is where the biggest challenges lie, and as such require more research and development.
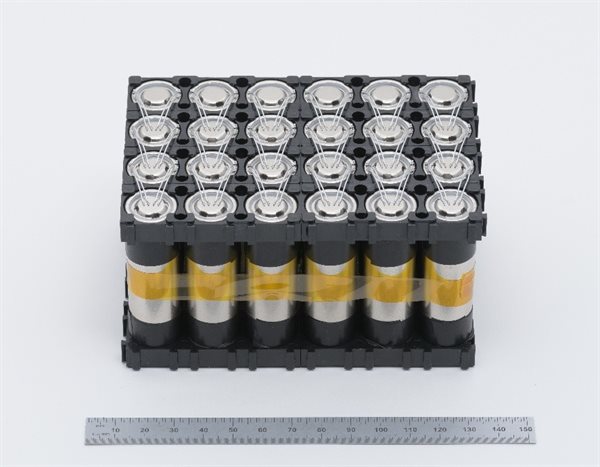
Wire bonded dummy battery cells
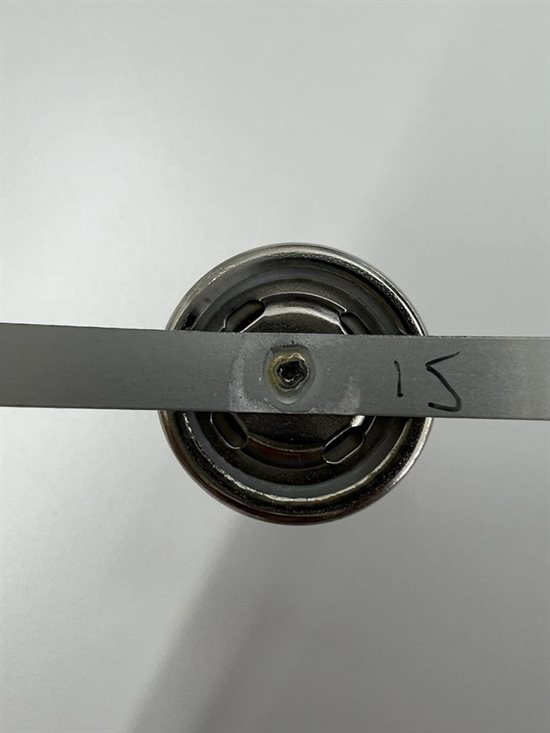
Welded dummy cell cap and Al strips using single mode laser