Quantification of Hydrogen in TSA-Coated API 5L X80 and AISI 4137 Steels Exposed to Seawater
TWI Industrial Member Report 1162-2022 [pdf / 1751 KB]
By Shiladitya Paul
Industrial Need
Cathodic protection (CP) systems are employed to mitigate corrosion of offshore structural steel below the water line. As a side effect of CP, hydrogen is often generated on the steel surface, particularly at more negative potentials. This hydrogen can ingress the steel and cause hydrogen embrittlement. To reduce the generation of hydrogen it is imperative to reduce the surface on which hydrogen is generated. This is generally achieved by coating the steel structure with a dielectric coating, such as organic paint. The presence of a dielectric paint reduces the current demand, thus reducing the kinetics of hydrogen generation, and allowing the anodes to last longer. However, with exposure time, paints degrade and their barrier properties deteriorate, resulting in seawater ingress and an increase in anode consumption. In areas where the electrolyte layer is not always present, these coatings when damaged offer little or no protection. To overcome some of the issues associated with paints, the offshore industry has resorted to thermally sprayed aluminium (TSA) for immersion service. TSA provides protection to steel in a similar way to that of anodes because of their position in the galvanic series in seawater. However, most of the steel structures currently protected by TSA have been fabricated from lower strength grade steels primarily due to hydrogen embrittlement (HE) concerns. HE becomes more severe as the strength of the steel increases. The very microstructures that give some carbon and low alloy steels their strength also results in their embrittlement. There are very few studies elaborating the effect of sacrificial aluminium coatings on the HE of steels. The limited studies found in literature focus on the embrittlement behaviour and not on the levels of hydrogen. The location of hydrogen in coated steel also seems to remain largely unknown with an assumption that they are in the steel. Thus, there is a need to experimentally determine the amount and location of hydrogen in TSA-coated steels when exposed to seawater.
Key findings
- TSA polarises both API 5L X80 and AISI 4137 steels to below the so-called protective potential of -0.8V (Ag/AgCl).
- API 5L X80 and AISI 4137 steels show similar levels of hydrogen after 30 days of charging at −1100 mV (Ag/AgCl).
- The levels of hydrogen observed in TSA-coated steel specimens were ~100 times more than that observed in uncoated specimens.
- The hydrogen in TSA-coated steel was localised in the TSA layer/steel-TSA interface.
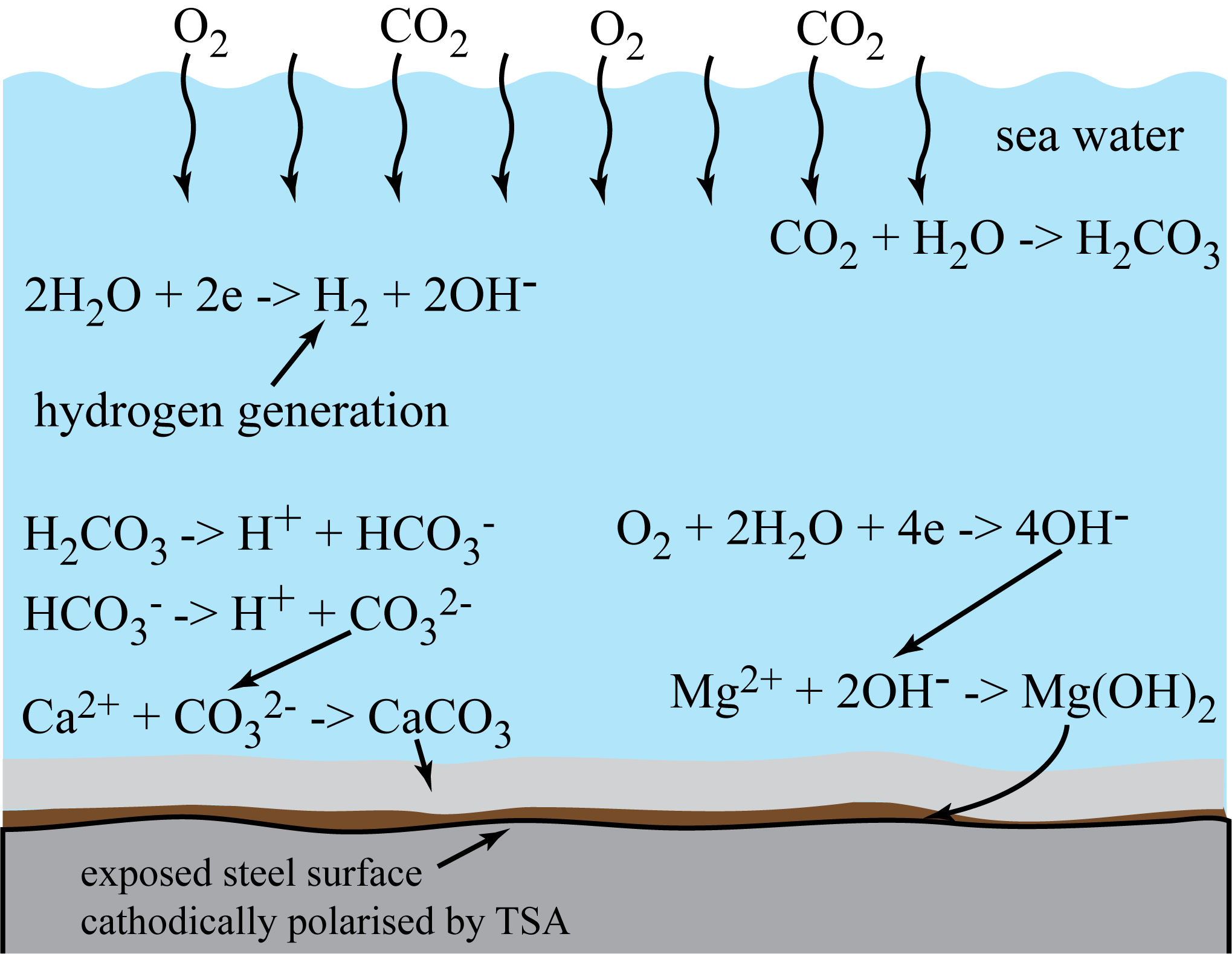
Mechanism of calcareous deposit formation on cathodically polarised steel surface in seawater