Distortion Reduction and Elimination for Additive Manufacturing
TWI Industrial Member Report 1176-2023 [pdf / 604 KB]
By Tyler London
Industrial Need
Laser Powder Bed Fusion (LPBF) is an additive manufacturing (AM) process that is capable of producing metallic parts in a layer-by-layer fashion directly from CAD data. LPBF can produce complex parts with near-full density and mechanical properties comparable to those provided by conventional casting and forming. Although there has been significant research into the entire LPBF supply chain, one of the key challenges to the widespread adoption of LPBF is the inability to achieve repeatable, high-quality parts from every build. The reduction of distortion in LPBF components is critical for ensuring a right-first-time LPBF build.
To support this industrial challenge, TWI participated in an Innovate UK (IUK) collaborative project called DREAM (Distortion Reduction and Elimination for Additive Manufacturing). The DREAM project sought to address this challenge through a multidisciplinary digital approach: coupling real-time data acquisition, advanced modelling, cloud-based computing, and adaptive machine process parameter controls to achieve zero-distortion builds. The DREAM project involved a number of partners: Renishaw, Granta Design (now ANSYS/Granta), and nquiringminds. The software, hardware, and cloud-based solution aimed to allow internet-enabled machines and systems to identify distortion during the build process and make real-time decisions and forecasts about process parameter controls to mitigate and control distortion during the build process. The successful implementation of such a strategy would have resulted in cost reduction, higher material utilisation, improved quality assurance, and reduced design cycle times in the LPBF process chain.
The DREAM solution was principally implemented through the installation of a Materialise Control Platform (MCP) in a Renishaw AM250 machine at TWI Ltd. The MCP enabled layer-by-layer control of processing conditions such as the laser power, exposure time, spot spacing, hatch spacing, layer thickness, and interpass time (recoating time). In parallel, a thermal imaging camera (along with other data acquisition systems) collected data in real-time during the build and sent the data sets to a data processing hub that integrated both nquiringmind’s and Granta Design’s contributions to the project. The data processing hub allowed for real-time data analytics to be calculated and decisions about whether or not (and how) to change processing conditions to be sent back to the MCP. Thus, in principle, if distortion (or a proxy for distortion) was assessed to have occurred, the data processing hub could then send a command to the MCP in an attempt to mitigate or control the observed distortion. This would then be repeated layer-by-layer or over groups (or aggregates) of layers, with the controlling commands updated based on how the observed signals evolved.
Owing to the value perceived by TWI of the modelling activities, TWI provided additional support for a small Core Research Programme with a 3 month duration to further the FE modelling efforts. This report summarises these activities.
Key Findings
- FE modelling can be a useful tool for optimising process parameters “offline” without physically performing the AM trials. In other words, conventional trial-and-error experimentation is not the most efficient approach to determining the best parameter sets. Instead, a validated FE model closely coupled to a targeted experimental test programme can be useful in establishing optimal parameter sets with reduced time and costs over existing work flows.
- FE models, with sufficient development, can be used to identify strategies that can give rise to more uniform thermal transients in AM parts. In particular, heat transfer models can be used to quantify the effect of changing laser power within a slice or on a slice-by-slice basis.
- It may not be advisable to pursue a technology strategy for part qualification based on real-time control and modification of process parameters. Any system that could achieve this would be redundant after the first instance. There are also quality assurance and control considerations around (potentially) regularly modifying parameters for nominally similar parts.
Impact
Through the DREAM project, this short-term Core Research Programme project, and associated parallel activities at TWI, the value of using modelling and simulation to support the development of AM technologies has been established. The maturity of advanced simulations methods for AM processes has led to a growth in both R&D activities and commercial consultancy. It is recommended that FE modelling of AM processes is seen as a key enabling technology to streamline design concept to design manufacture timelines by complementing experimental test programmes and performing virtual design-of-experiments to minimise physical testing and characterisation.
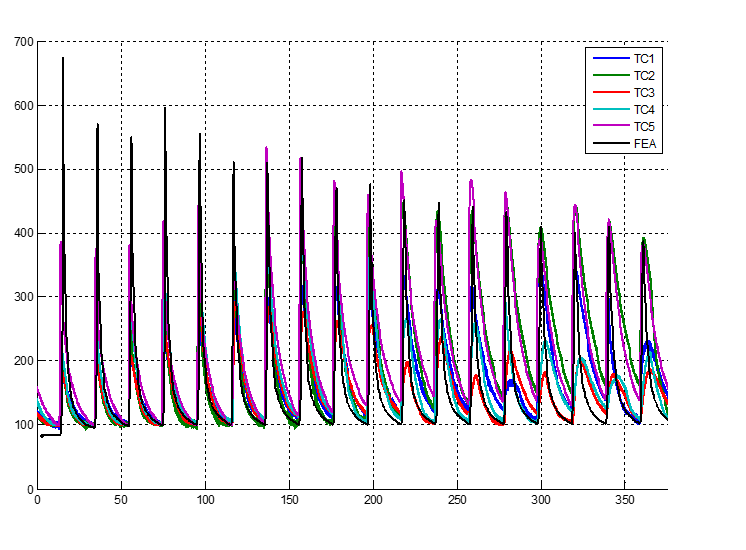
Thermal transients captured by in-situ monitoring of the laser powder bed fusion process