Medium Range Guided Wave Inspection for Defect Detection and Monitoring of Plate-like Structures
By Hugo Marques
Industrial Need
The ability to launch ultrasonic guided waves from an accessible location in order to examine inaccessible or hidden sections can be applied to structures produced from medium sized plate-like components. These can range from flat plate structures such as bridges and storage tank floors to large diameter cylinders, for example storage tanks walls, pressure vessels and wind turbine support structures. However for such cases, deployment of an array of transducers via an encircling collar, as is done for pipeline inspection, is not applicable.
The work described in this report developed and evaluated a transducer array design , referred to an an omnidirectional SH0 transducer, to enable successful ultrasonic guided wave testing of plate-like components. The SH0 guided wave mode was selected because it has unique in-plane proapagation characteristics, making it ideal for inspection of structures such as filled storage tanks, that contain other material. The new transducer array could operate solo or as part of a sparse array for medium-range defect detection and monitoring of large plate-like structures.
For suitable applications, the technology described in this report should be considered, although at the time of publication it cannot be described as an off-the-shelf solution, and development work is likely to be needed before use in the field. The technology could potentially facilitate and reduce the cost of structural health monitoring of many structures in a variety of industries. Its deployment for relatively large scale structures, such as storage thanks, pressure vessels, offshore platforms, wind turbines, bridges, ship hulls, and many others, could provide a solution for effective structural maintenance.
Key findings
- FEA modelling predicted that a localised circular array design of eight or ten piezoelectric thickness-shear monolithic transducers would generate omnidirectional transmission of the SH0 mode with a mode purity above 20dB.
- A prototype, named “omnidirectional SH0 transducer”, was developed incorporating a localised circular array of eight commercially available piezoelectric thickness-shear monolithic transducers.
- The omnidirectional SH0 transducer was empirically characterised on a steel plate specimen. The results indicated omnidirectional transmission of the SH0 mode with a maximum 3dB variation in amplitude.
- In terms of SH0 mode purity, the omnidirectional SH0 transducer achieved an SH0 mode purity of 22±2dB at the 40kHz to 55kHz frequency range.
- Evaluating the omnidirectional SH0 transducer defect detection sensitivity, a semi-elliptical defect simulating a fatigue crack on a 10mm thick steel plate was successfully detected, at a distance of 1000mm.
- The defect was incrementally introduced. Through the use of the post-processing methods, it was possible to detect the defect at the frequency range 85kHz to 115kHz, with the dimensions 50.0±0.5mm length, 1.0±0.5mm width and 6.0±0.5mm depth, corresponding to approximately 60% wall loss of the structure.
- In pulse-echo operation without post-processing analysis, the defect was detected at 100kHz with the dimensions 65.0±0.5mm length, 1.0±0.5mm width and 8.0±0.5mm depth.
Test set-up - the prototype omnidirectional transducer, mounted at the centre of the plate, and the scanning vibrometer system, used to measure the ultrasound propagation, may be seen
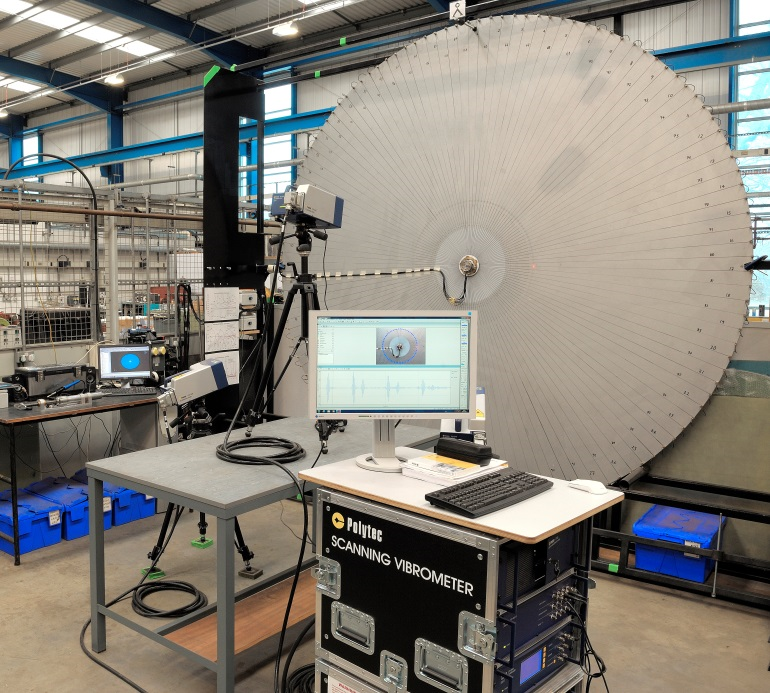