By Callum Picken and Michal Lewandowski
Industrial need
The development of the hydrogen economy depends on the ability to produce, transport and store hydrogen safely. Austenitic stainless steels show much lower susceptibility to hydrogen embrittlement than ferritic steels. Their mechanical properties require investigation in high pressure hydrogen environments. TWI has developed unique capabilities for tensile, fracture, crack propagation and fatigue tests in hydrogen at high pressure and high temperature.
This project assessed the performance of candidate austenitic stainless steels. The materials were selected because they are known to offer high resistance to damage caused by stress in the presence of hydrogen, a phenomenon known as hydrogen environment embrittlement (HEE).
Key Findings
- Loss in performance was observed in all the materials studied (AISI grades 304, 304L, 321, 347 and 316L) when tested in hydrogen gas. Based on the relative reduction in area, the two materials which performed worst were 304L and 316L; 304 appeared to perform the best.
- High pressure hydrogen atmospheres did not affect the room temperature proof strength in these materials.
- Only the 304L exhibited a significant reduction in ultimate tensile strength under high pressure hydrogen.
- Failure occurred through quasi-cleavage, micro void coalescence and faceted cleavage with a degree of temperature dependence, as expected.
- Despite the routine use of 316L materials in hydrogen service by industry, a significant reduction of ductility was observed.
- The formation of strain-induced martensite is a factor during these failures; in general materials with a higher nickel equivalent are less likely to form martensite on straining and hence perform better in the environments examined.
- Despite the performance loss of these materials, they retained a significant amount of ductility in hydrogen and are valid candidate materials for hydrogen service. Testing of materials to be used for critical service is recommended.
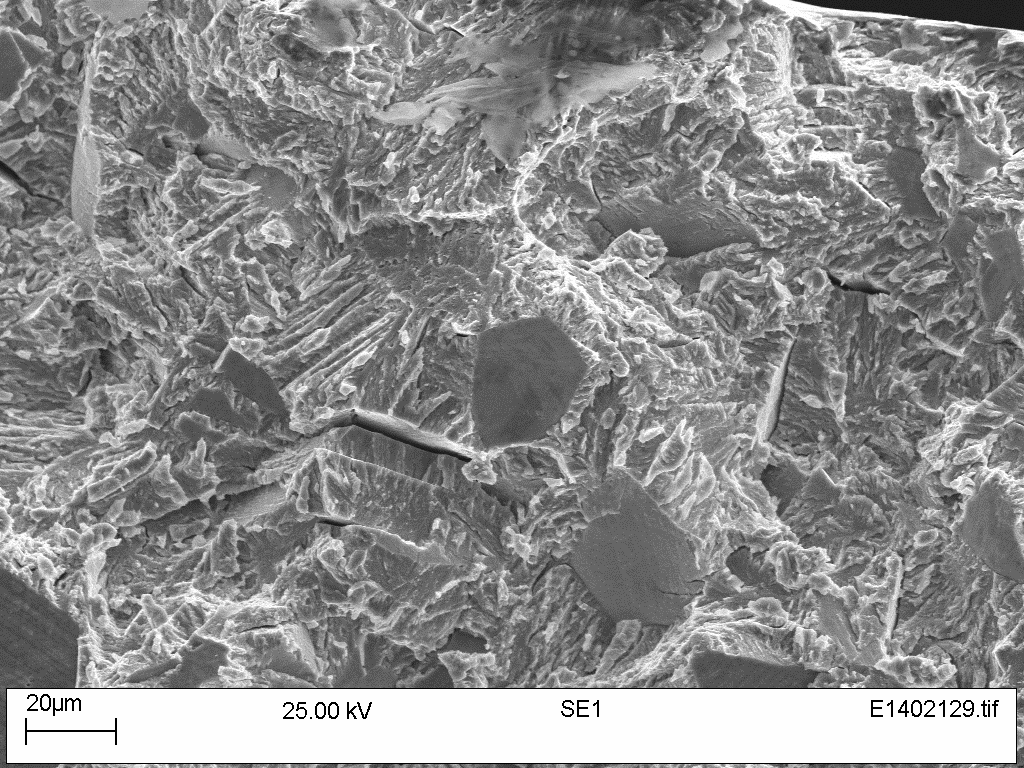
Brittle fracture in low-nickel 304L austenitic steel tested in 400 bar hydrogen at –50°C