Preliminary Mechanical Properties of Thermoplastic Composites Containing Multiple Pierced Perforations
By C Worrall and F Bahrami
Industrial Need
Perforated metal panels are currently used in many industries and applications including sound absorbing engine components, leading edge de-icing, and blast protection systems. Due to the increased demand for ever more lightweight components, the aerospace industry in particular is trying to exploit composite materials. Composite parts can be manufactured to near-net-shape with minimum wastage of material; however, there is often a need for further machining. Creating holes for assembly account for approximately 90% of the aerospace industry’s requirements for composite machining.
Perforation of composite materials is currently carried out using conventional machining techniques, such as drilling or abrasive water jet cutting. However, these techniques cut the load-bearing fibres and reduce the efficiency of the composite around the holes. The work described in this report aims to exploit the benefits of thermoplastic composite materials for perforated structures.
The approach investigated in this project is a development of thermally assisted piercing (TAP). The thermoplastic composite is heated to its melting point and a metal pin is pushed into the material. Since the matrix is molten, the fibres are free to move around the pin allowing a hole to be made without cutting the fibres. In previous work strength improvements of up to 11% and 21% were found for pierced specimens compared with drilled specimens for open-hole tension and compression loading, respectively.
Although offering several advantages over drilling as a means of making holes for mechanical fastening, the TAP process may offer a greater potential as a process for making multiple small diameter holes. The volume of material heated per hole is reduced for smaller holes, making it more energy efficient. Furthermore, if multiple holes can be made in a single TAP process then there could be significant time savings to be exploited when making a large number of small holes in a composite (perforating). Therefore, this work was carried out in order to determine what applications could benefit from using perforated composites, and whether the strength improvements seen with the larger TAP holes were preserved with multiple small holes.
Key findings
- Mechanical tests and microstructural analysis show that pierced composite coupons have superior tensile properties but inferior compressive properties, compared with drilled composite coupons.
- These findings will determine those applications that can benefit from the TAP perforation process in the future and those for which the process is not suited.
- Microstructural analysis of pierced coupons showed that the reinforcing fibres create a path around the holes that results in the tensile strength increase, but also the formation of local kink bands that cause the reduction in compressive strength.
- Numerical modelling of the process is challenging, and a validated model has not yet been achieved. A suitable model does not need to include the flow of a molten matrix and the displacement of every individual fibre; assumptions can be made to simplify the computation while still generating volume fraction and orientation distributions for the perforated composite.
Multiple piercing head, with 100 pin blocks attached
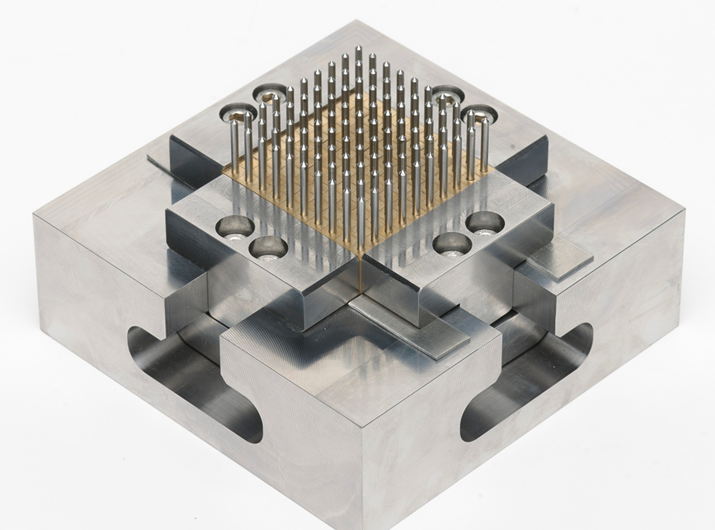
Average open-hole tensile strength of the composite for unperforated (UP), pierced (P), and drilled (D) group. Error bars indicate plus/minus one standard deviation
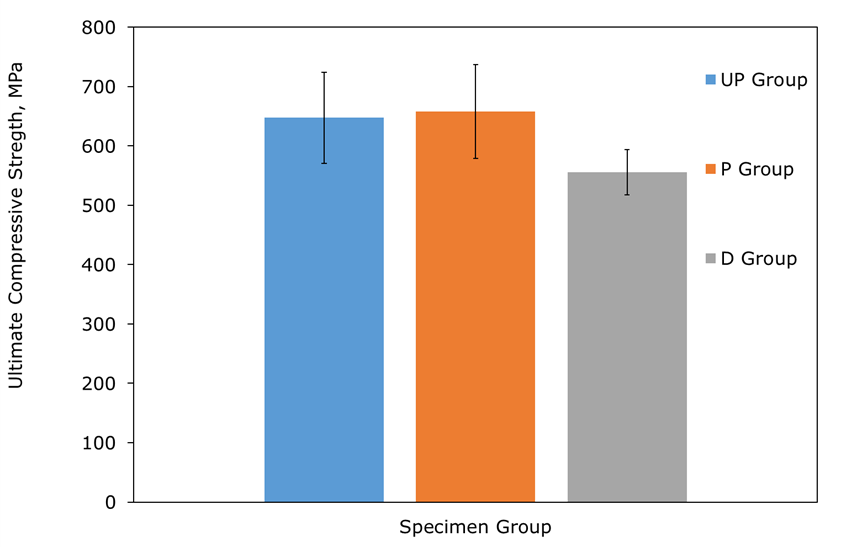