Solidification Cracking Susceptibility of AA6061 and AA2024 Aluminium Alloys during Laser Welding
TWI Industrial Member Report 1177-2023 [pdf / 3991 KB]
By Yao Ren and Tyler London
Industrial Need
High welding speed and low heat input are among the benefits associated with laser welding, making it an attractive fabrication process for many industries. In some applications, however, these benefits are overshadowed by weld zone hot cracking. This is particularly true in welds in which either impurities or solute atoms are segregated to weld metal and/or heat-affected zone (HAZ) grain boundaries, leading to the formation of low melting point brittle films, which can then crack during the final stages of solidification.
One example of commonly used yet hot crack susceptible materials are heat-treatable aluminium alloys (e.g. 2000, 6000 and 7000 series), which are prone to solidification cracking.
An approach to try to overcome hot cracking is to try to influence the welding parameters used, and control restraint, as the cause of hot cracking is not only metallurgical, but also an interplay of thermal and mechanical conditions, during solidification. In practical terms, however, a large number of welding trials can be required before determining what the desired laser beam energy distribution needs to be for a given application, and this is neither time efficient nor economic. With the assistance of computer-based finite element analysis (FEA), the laser beam welding process, as well as the hot cracking behaviour of the laser weld itself, can be simulated by introducing a moving heat source to a model that contains the full information of the material(s) being joined.
This report describes modelling and experimental work that was undertaken to investigate the link between thermal transients, strain transients and internal stresses and susceptibility of laser-welded aluminium specimens to exhibit hot cracking. Experimentally validated FEA models were established using measured temperature and strain histories. The validated models were then used to identify correlations between thermal transients, strain transients, and the susceptibility to hot cracking. This model can, in the future, be used to predict the type of laser energy distribution needed to reduce or mitigate hot cracking.
Key Findings
- Autogenous laser melt runs were made on both trapezium- and rectangular-shaped coupons, to produce hot cracked samples in which the length of the centreline hot crack could then be related to welding speed, restraint, as well as the effect of shielding gas type on the alloys and thicknesses tested.It was observed that weld centreline cracking initiated from the weld start position, at the narrow end of the coupon, propagating along the weld’s length and later stopping as the coupon became wider.
- During exposure to a constant laser beam power, the length of the centreline crack correlated with the welding speed, in the sense that the slower the welding speed, the longer the centreline crack.
- Welds made using He gas shielding showed longer centreline cracks than those made using Ar. This behaviour might be attributed to the lower presence of residual alloying Magnesium (Mg) element content in the case of Ar, compared to He, shifting further away from the critical level for crack sensitivity in Ar than in He.
- The initiation and propagation of cracking was affected by the extent of the restraint, applied external clamping and/or shape of the materials, on the molten weld material before it fully solidified.
- The results of the finite element simulations demonstrated that a semi-empirical approach can give a modelling criteria to estimate the susceptibility to cracking. The model was validated by comparing the thermal and mechanical behaviour of the welded plates to thermocouple and strain gauge data, respectively. The regions that exhibited cracking (and no cracking) were subsequently compared to thermal transients and stress/strain transients acting on the weld centre line. This approach then enabled a threshold to be defined that could approximate when cracking would occur. However, this approach is not in-and-of-itself predictive: it requires calibration data from physical tests before it can be used. More refined modelling, in conjunction with alternative crack susceptibility criteria (such as the physics-based models identified in the literature review) may therefore be needed to improve the predictive capability.
Impact
- Characterise the baseline hot cracking sensitivities of selected 2mm thickness AA6061 and AA2024 aluminium alloy sheets, when being laser beam welded with a single beam with a standard Gaussian energy distribution.
- Compare the hot cracking sensitivity of the materials being welded when using different shielding gases, argon (Ar) and helium (He).
- Identify experimental conditions resulting in a pronounced crack susceptibility in AA6061 aluminium alloy, then measure the temperature and transient transverse strain near to the weld pool during the welding process.
- Establish an FEA model to simulate this hot cracking behaviour.
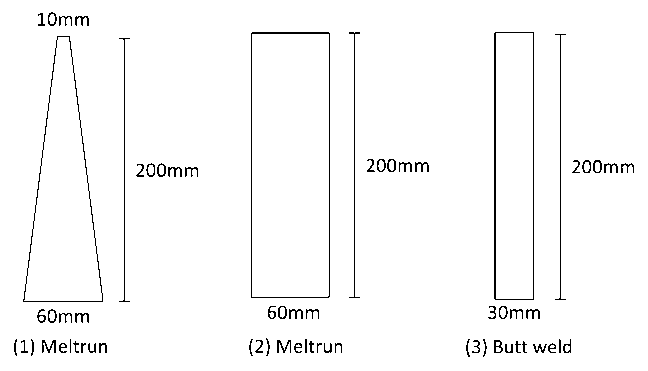
Materials and specimen configurations used for welding trials
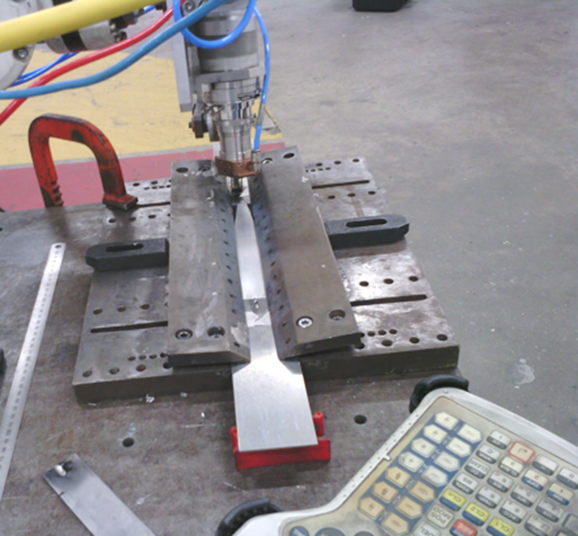
Welding setup for the welding trials performed in the PA welding position
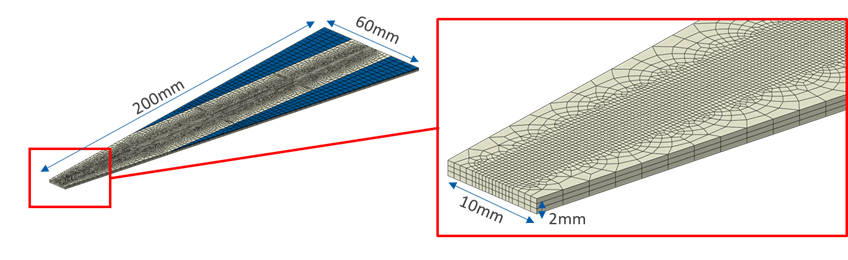
Images of the finite element mesh used in FEA modelling