Testing of a Shearography System for On-Site Inspection of Wind Turbine Blades
By H Zheng, J Gao
Industrial Need
Wind energy is a rapidly growing industrial sector. As wind turbines are expected to work 90% of the time during a typical lifetime of 20 years, structural flaws are of great concern, particularly for blades. Repairing or replacing a blade is always difficult, especially for large wind turbines. The downtime of a wind turbine installation due to a blade failure usually lasts 4-6 days, longer than that due to electrical or mechanical failure within the nacelle. Cracks in the blades sometimes appear soon after manufacture. Defects also can be produced during transportation. Current inspection of wind turbine blades (WTBs) is mainly reliant on sending an engineer via rope access.
An ideal solution to this problem is to utilise a compact robot that can reach the blade and implement faster inspections on site. Shearography has long been recognised as a powerful inspection technique, and has found wide application in a range of industries including aerospace, automotive and shipbuilding sectors. However, conventional shearography still needs a relatively stable environment; thus it is difficult to use for on-site WTB inspections. The authors aim to develop an integrated system where a compact robot carries a shearography system to roam along the WTB surface to conduct an inspection.
This has led to collaborative research projects with funding from the European Commission and which involve a number of partners specialised in various techniques such as robotic systems and remote data communications and control, as well as wind farm operators and wind energy service providers. The work described in this report is part of this bigger picture, and is focused on data processing of the huge amount of shearography images recorded during a field test.
Key findings
- The approach of using shearography integrated with a robotic system to inspect WTBs on-site is viable. However the TRL (technology readiness level) of the whole system is 5 at the time of this report. Considerable work is required in order to move it up to TRL 9 for commercial application.
- Image processing algorithms are useful in improving the quality of shearography fringe patterns, and hence help to identify potential subsurface defects within the WTB. However, the effectiveness of those algorithms is limited. The main factors affecting performance are still the hardware of the shearography and the robotic deployment system.
Laboratory test demonstrating how the shearography system was carried by a suction based end-effector that was able to be attached vertically on a WTB section sample.
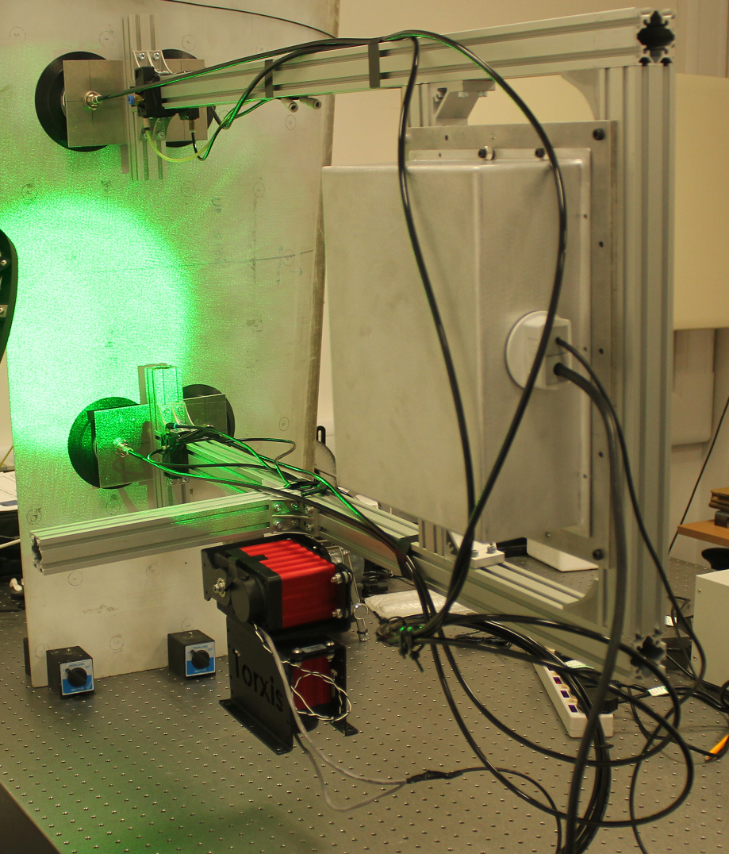
Field trial on a wind tower where the shearography equipment was attached to a blade for inspection.
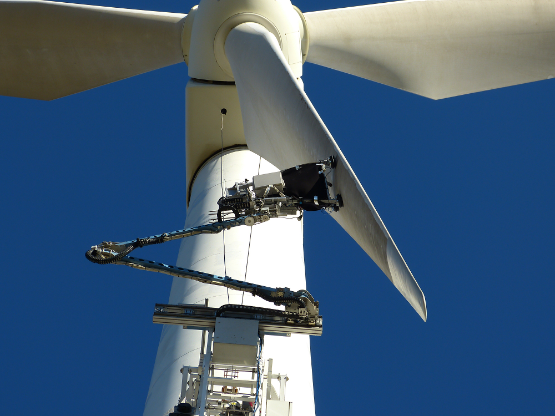