By Ruth Sanderson, Shehan Lowe, Jane Allwright, Keith Thornicroft and Sabrina Blackwell
Industrial need
Guided waves are capable of screening straight pipe for patches of corrosion and can provide the axial distance of the defect from the tool location and an estimate of cross sectional area loss. However, the sensitivity is such that a defect must be around 5% of the cross section to be reliability detected and present systems cannot easily distinguish between a general wall thinning around the entire circumference and a deep corrosion pit.
The standard inspection technique uses a limited number of guided wave modes. However, there are many different wave modes possible in a given pipe that are currently ignored. These wave modes each interact differently with different sizes and shapes of defect. This project aims to investigate the potential to capture information from these wave modes and use it to detect smaller defects and provide a more quantitative assessment of them.
Key Findings
- A technique for rapid calculation of dispersion curves for pipes has been developed which can be incorporated into future inspection software. This could lead to time savings when applying many of the emerging quantitative guided wave inspection techniques.
- The use of a high number of flexural modes gives more accurate flaw size predictions. The use of the L(0,1) wave mode family has therefore been investigated since it has a high number of flexural wave modes for a given frequency. A pure L(0,1) signal has been successfully produced in the lab.
- A new technique for the measurement of the axial extent of a flaw has been developed and successfully experimentally validated.
- The effect of a 90° bend on the guided wave signals in a pipe has been investigated for several wave modes. The effect of the bend on an axisymmetric signal has also been calculated for four different geometries of bend elbow and welds.
- A time reversal technique for producing a desired signal beyond a pipe bend has been tested using FEA. This demonstrated that the technique is feasible but that the received signal will not be a perfect reconstruction of the originally sent pulse. This therefore provides an important method for creating a signal beyond a bend with a strong, but not 100%, axisymmetric component.
- An analytical method for applying and undoing the effect of a bend on a defect signal has been written into a MATLAB script, and has been successfully validated against results directly from the FEA.
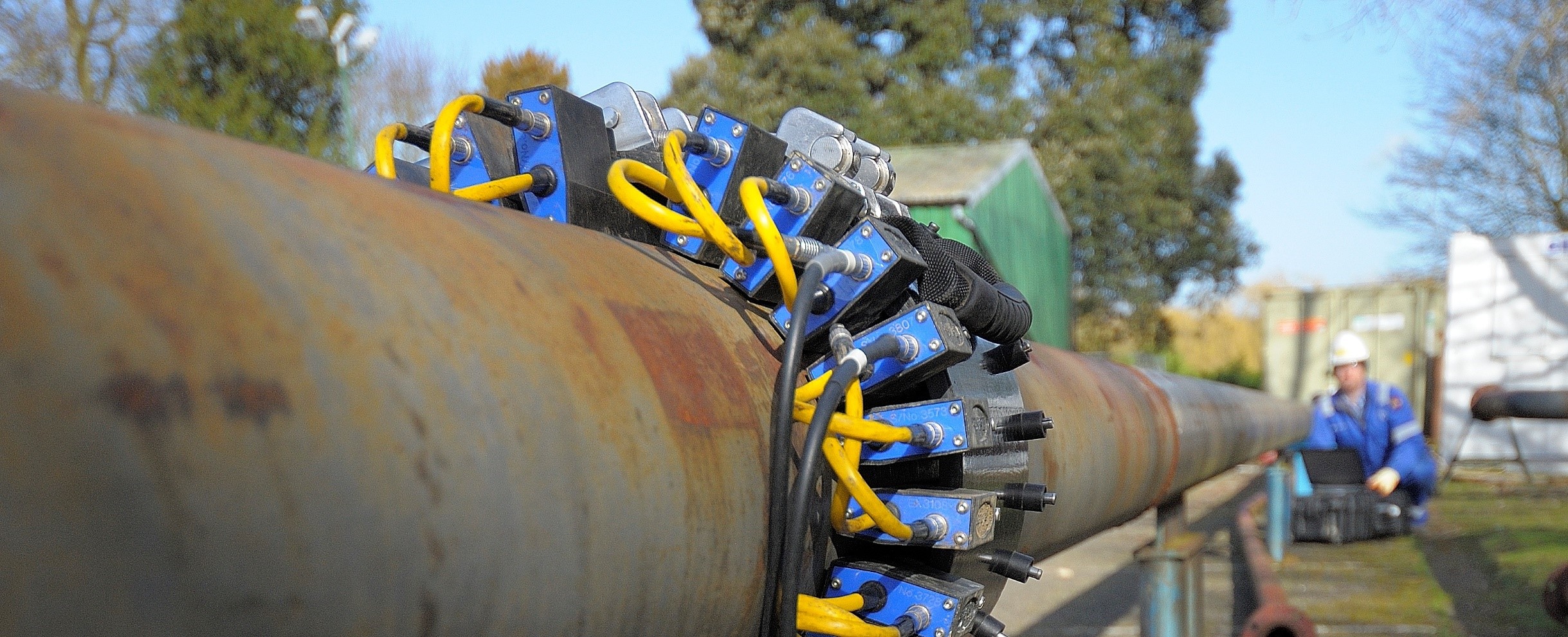
Guided wave inspection equipment