Investigation of Arc Based Additive Manufacturing
By Adrian Addison
Industrial Need
Additive manufacturing (AM) as a subject has received a great deal of interest in recent years as a method of manufacturing near net shape metallic components directly from design data without the need for pre-forming, casting, forging or machining from billet. There are several approaches to AM of metallic materials, but whatever the process, the basic concept is the same: using a controlled source of heat to melt a metal feedstock (consumable) in a specific point in space and combining these points to create a layer of fused metal. These layers are then stacked to create the desired three-dimensional part. There are different heat sources and feedstock options available, and different combinations have different capabilities. This report describes work carried out using the metal inert/active gas (MIG/MAG) process, i.e. an arc as a heat source and feedstock in the form of a wire. The work:
- Examines the basic approach to building simple parts with wire and arc additive manufacture using industry standard deposition and manipulation equipment.
- Develops deposition parameters for definable bead shapes and determines process capability and reliability.
- Explores methods of combining single beads into larger geometrical shapes in order to produce mechanical test samples.
- Generates basic mechanical properties and microstructural data for a range of materials deposited with wire and arc AM.
Key findings
- Even for relatively simple components, the deposition process is rarely in a steady state and modifications need to be made to deposition parameters to maintain a consistent bead geometry and thermal profile, particularly at the start and end of a deposit, and where features intersect.
- The thermal field and history experienced by material during AM is very complex and can result in the formation of microstructures which differ from those obtained from conventional weld metal.
- The mechanical properties of as-deposited material are not what would be expected when using the same consumable wire for conventional welding. The yield and ultimate strength are lower, whilst the impact and fracture toughness are higher.
- The use of welding consumables as a feedstock for AM is not necessarily appropriate. The use of a feedstock chemistry designed to respond to the thermal history of AM processes and provide the required properties in the as-deposited condition should be considered.
Completed full scale wall made with parallel bead deposition profile
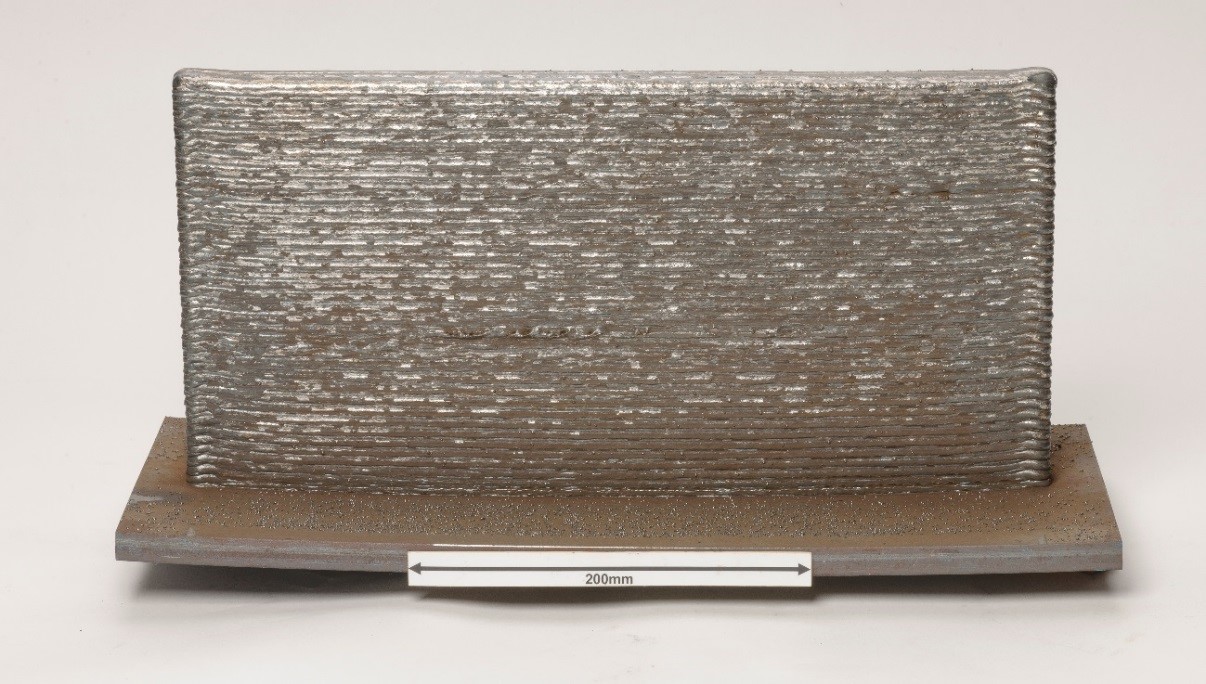
Vertical cross section of Alloy 625 alloy wall built using parallel bead deposition method
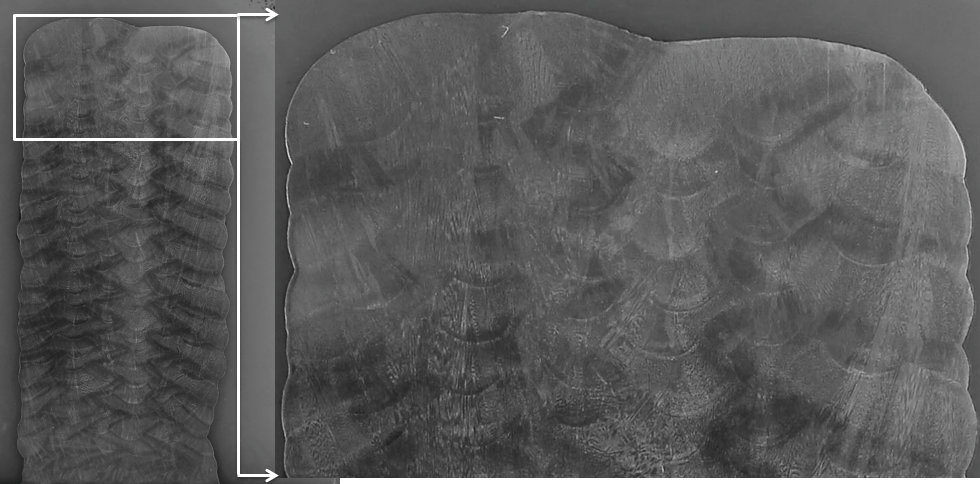