Refill Friction Stir Spot Welding Parameter Development for Transport Industry Aluminium Alloys
By P Santos and A McAndrew
Industrial Need
Refill friction stir spot welding (RFSSW) has several advantages compared with other mainstream single-point joining or mechanical fastening processes. Although many organisations recognise these advantages and benefits, further research is required in order to implement this technology into large-scale production and increase the current technology readiness level. This report describes the collection of baseline mechanical properties and microstructure characterisation of RFSSW welds on various transport aluminium alloys used in the transport sector, intending to promote industrial uptake.
Key findings
- All the process parameter combinations used in this investigation surpassed the strength requirements for resistance spot welding, one of the competing single-point joining processes.
- In lap shear testing, average strength values showed small scatter and consistent failure modes within the same parameter combination. Low rotation speed and high plunge depth values improved the mechanical performance on all alloys tested in this investigation.
- Similar failure loads under cross tension conditions were obtained across all alloys. This was attributed to the increased stress concentration at the hook tip from this testing method, leading to early failure of the specimen.
- Fatigue test results were used to establish an equation for the S-N curve. Acceptable fitting coefficients were found for each test condition. Failure before the first million cycles was observed for the specimens in the bare condition.
- The presence of an interfacial sealant improved the static and fatigue strength of the joints tested, without compromising weld integrity.
Schematic of the RFSSW process:a) Shoulder-plunge variantb) Probe-plunge variant
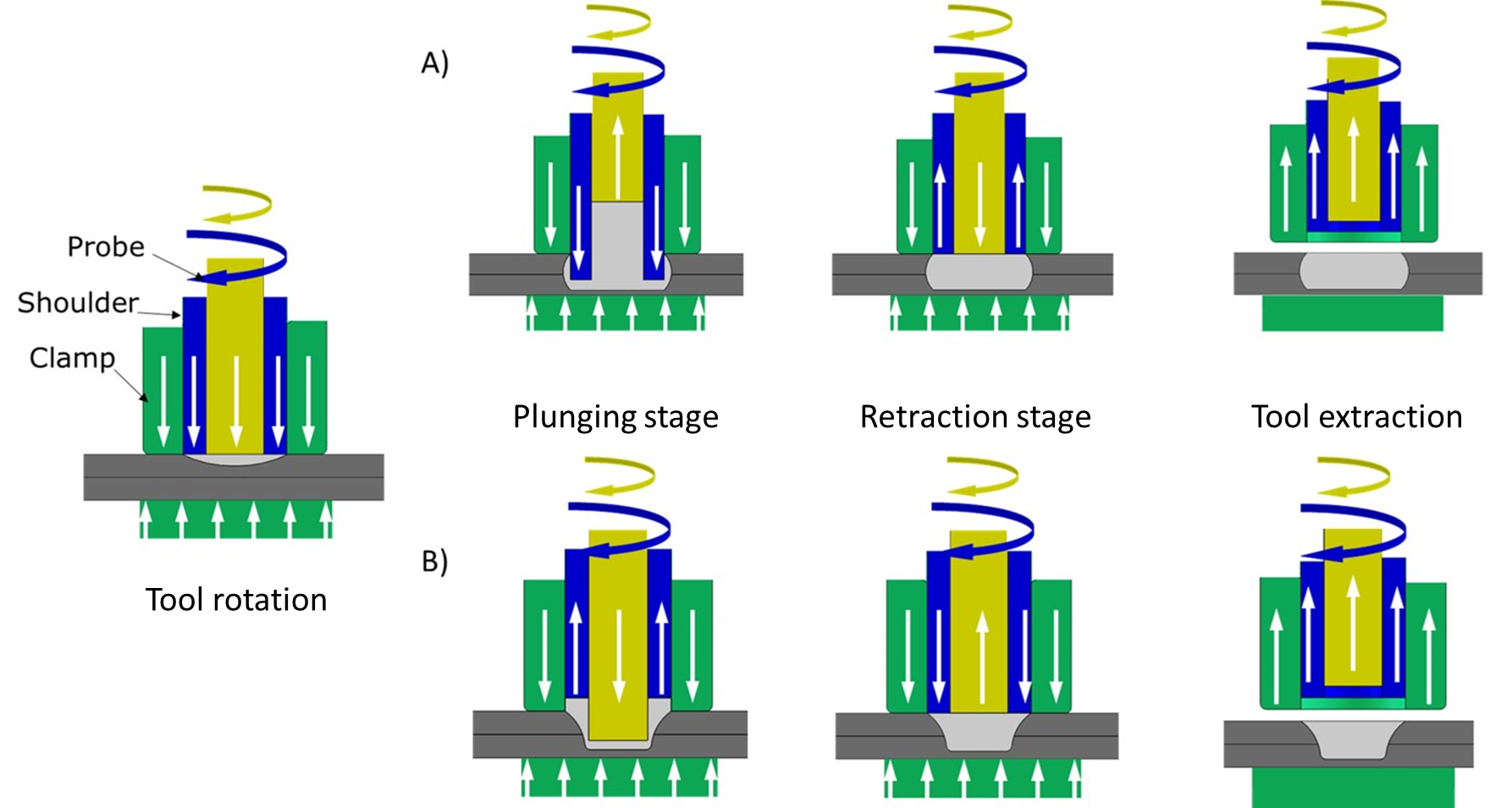
TWI’s FW-35 KHI RFSSW system
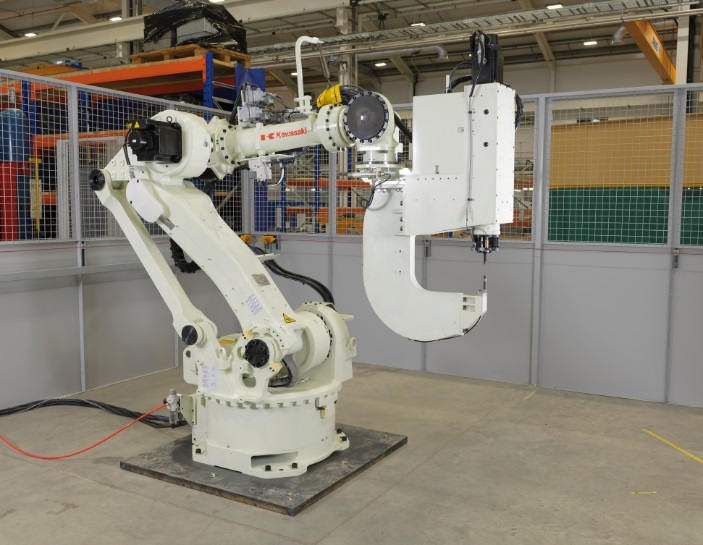
Cross-section of RFSSW AA7075 (in T6 condition). SZp and SZs are the stir zones of the probe and shoulder respectively. HAZ is the wider heat affected zone surrounding the weld:a) Hook region (transition from unjoined region to welded area);b) Stir zone/thermo-mechanically affected zone (SZ/TMAZ) interface
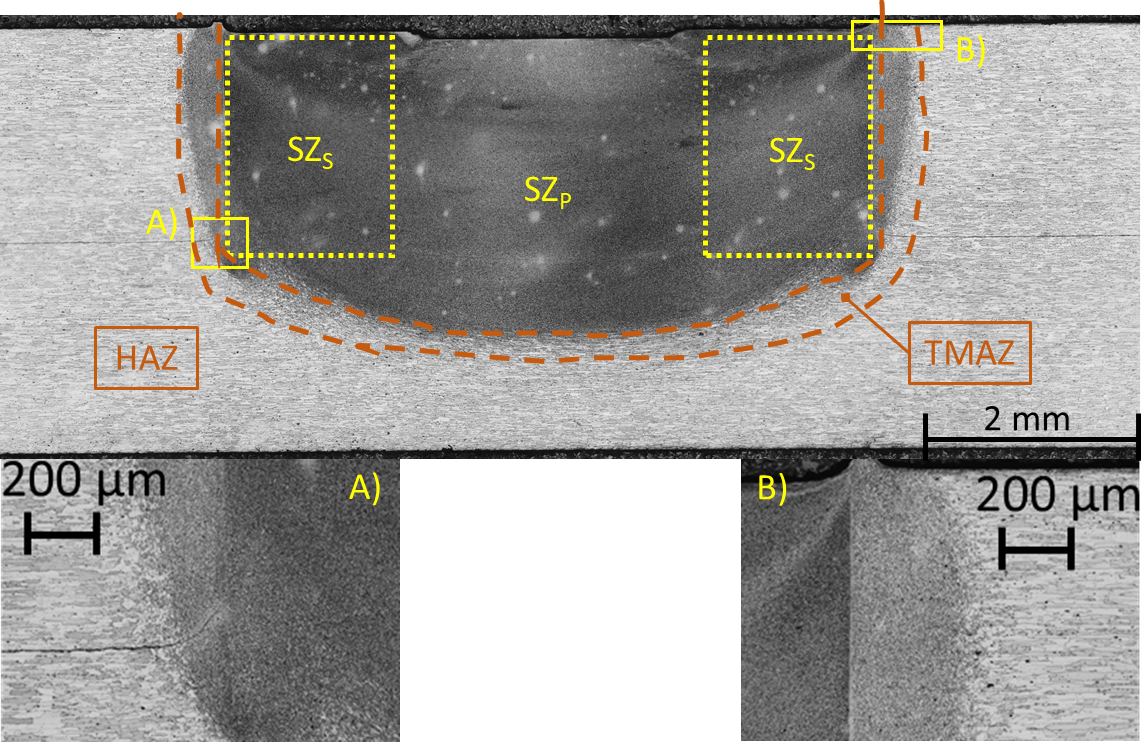