Linear Friction Welding of Advanced Materials - Carbon Fibre Reinforced Thermoplastic
By B Flipo, C Worrall, P Clark and J Greenwood
Industrial Need
Air traffic is doubling every 15 years and carbon fibre reinforced polymer (CFRP) is helping to meet this demand. The increasing use of composite materials in aircraft is set to continue as they offer the potential for significant weight savings over metallic materials. The predicted growth in single aisle aircraft is driving the need for faster production rates. With composites this challenge is likely to be met using thermoplastic composites as they offer alternative production processes such as thermoforming; a process that does not suffer from long cure schedules afflicting thermoset composite materials cured in an autoclave. There will, inevitably, be a need for joining parts, and thermoplastic composites offer the potential for joining by thermal welding processes.
Continuous carbon fibre reinforced PEEK composites joined using induction welding or resistive implant welding can achieve joint strengths up to the shear strength of the parent materials being welded, approximately 45MPa, and adhesively bonded carbon/PEEK laminates have demonstrated joint strengths of up to 28MPa after the application of appropriate surface treatment. The target for this project was to achieve a value of 25MPa in joints produced using equipment designed for linear friction welding of metals. This would be comparable to adhesively bonded joints but without the need for any surface pretreatment.
Key findings
- Use of a sacrificial interlayer requires careful placement of the layer during laminate manufacture.
- Pure PEEK and carbon/PEEK composite joints were welded successfully using suitable process conditions. ssessment of the PEEK welded coupons showed molten polymer had been forged out of the joint during the welding process indicating sufficient heat had been generated.ssessment of the PEEK welded coupons showed molten polymer had been forged out of the joint during the welding process indicating sufficient heat had been generated.
- Visual assessment of the PEEK welded coupons showed molten polymer had been forged out of the joint during the welding process indicating sufficient heat had been generated. ssessment of the PEEK welded coupons showed molten polymer had been forged out of the joint during the welding process indicating sufficient heat had been generated.ssessment of the PEEK welded coupons showed molten polymer had been forged out of the joint during the welding process indicating sufficient heat had been generated.
- The PEEK polymer was not discoloured which suggests that the temperature had not exceeded the material’s degradation temperature.
- Applying LFW to continuous carbon fibre reinforced PEEK thermoplastic composites using the metal welding equipment shows potential for preparing welded joints.
Basic principle of linear vibration welding/linear friction welding
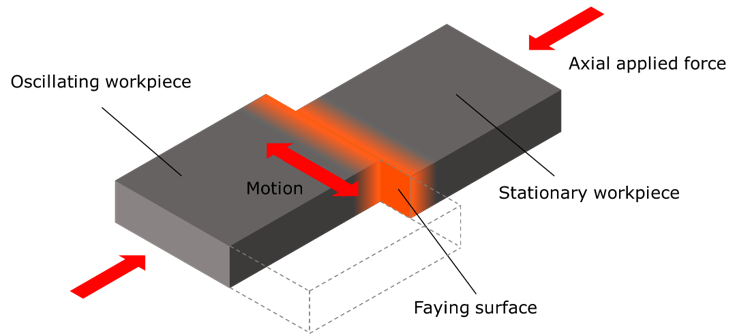
Linear friction weld in continuous carbon fibre/PEEK composite (yellow lines denote weld location)
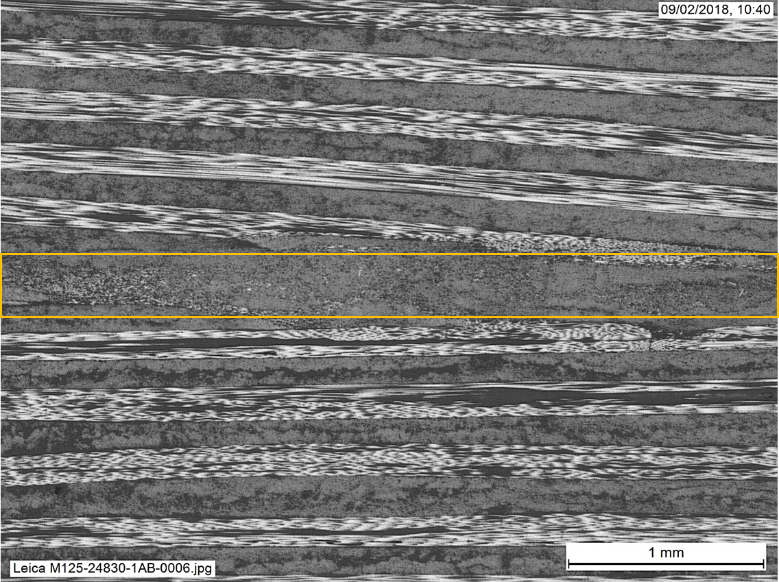