Investigation of Effect of Material and Geometric Features on SurFlow™ (Lamarr)
TWI Industrial Member Report 1181-2023 [pdf / 20,453KB]
By The Viet Hoang
Industrial Need
The demand by customers for increased comfort has resulted in the need for complex systems, which means interconnectivity. Electrification of aircraft, cars, ships etc. has led to an explosion in the quantity and complexity of data wires. For example, today's sophisticated computerised aircraft carry 30-50 miles of wires. As such, the exposure to intermittent wiring connections is higher than it was in the simpler aircraft 40 years ago. Application of SurFlow™ in structures will address the following need in the industry:
- Support increased communication needs: Boeing estimates that there are as much as 67km of wire on the Next-Generation 737-600/-700/-800/-900ER models. The Airbus A380 has 100,000 wires totalling 530km and uses 40,300 connectors performing 1,150 separate functions. Today's luxury cars contain 1,500 copper wires, totalling almost one mile in length. It is therefore imperative that these wires, along with connectors, are properly installed and maintained. All these wiring harnesses occupy a significant percentage of the vehicle payload.
- Reduce the complexity of cabling design: Systems development represent 17% of the development costs of a new airplane. The delivery of the A380 has been delayed for over two years due to integration of complex wiring system. This has led to an extra cost of £4.8bn.
- Reduce installation cost: The aircraft wire and cable market is worth US$1bn with 50% attributed to linefit and 35% dedicated to data transfer. SurFlow™ can significantly reduce this cost.Minimise the cost of wire maintenance: Honeywell estimate the wire maintenance costs at £90k every four years for narrow body aircraft.
- Reduce the weight of aircraft: This is a major impact on fuel consumption and payload. Removing 35% of the wiring will save 2m litres of aviation fuel over the lifetime of an Airbus A320.
Current studies at TWI have shown the following characteristics of the SurFlow™ technology:
- Data speed of 3Gbps, which is about three times faster than Cat5e Ethernet cables.
- In the case of damage, the signal will find a path around the damage and propagate, which means uninterrupted signal transmission.
- Can be applied to glass, carbon, aramid and natural fibre composites.Technology has been tested in the 2-6GHz range, but can be extended.
SurFlow™ has a variety of functionalities, which can be applied to many industries. These can be categorised as direct and indirect. Direct functionalities are where the signal is used for either data transmission such as a live video feed or as a control signal. Indirect functionalities are where the signal conveys information about the material it travels through. For example, if there is damage in the structure, the signal will travel around it. This change in the signal path will result in changes in some of the signal characteristics. Through application of signal interpretation and triangulation algorithms it is possible to locate the damage. Hence the technology can be used for structural health monitoring (SHM) or as a non-destructive testing (NDT) method.
Key Findings
- Carbon fibre composites exhibit high permittivity and conductivity in the frequency range of 2-6GHz.
- Due to their high conductivity, carbon fibre-based composites provide less support for electromagnetic surface waves that are tightly bound to the interface between the composite and air.
- Type and placement of transducers affect signal propagation through the composites.
- Despite efforts to optimize transducers and minimize the effects of air wave and guided wave modes, it is not possible to completely eliminate both modes.
- Because of their high conductivity and subsequent reduced support for surface electromagnetic waves, changes in the geometries of carbon fibre composites do not significantly impact the propagation of electromagnetic surface waves through the composite in in the frequency range of 2-6GHz.
Impact
The key findings translate to having met the main objective, which is to investigate the effect of materials and geometries on signal propagation in SurFlow™. It has been shown that the retrieved electrical properties of the selected carbon fibre-based composite are not suitable, due to their high conductivity, for supporting electromagnetic surface waves within the 2-6GHz frequency range.
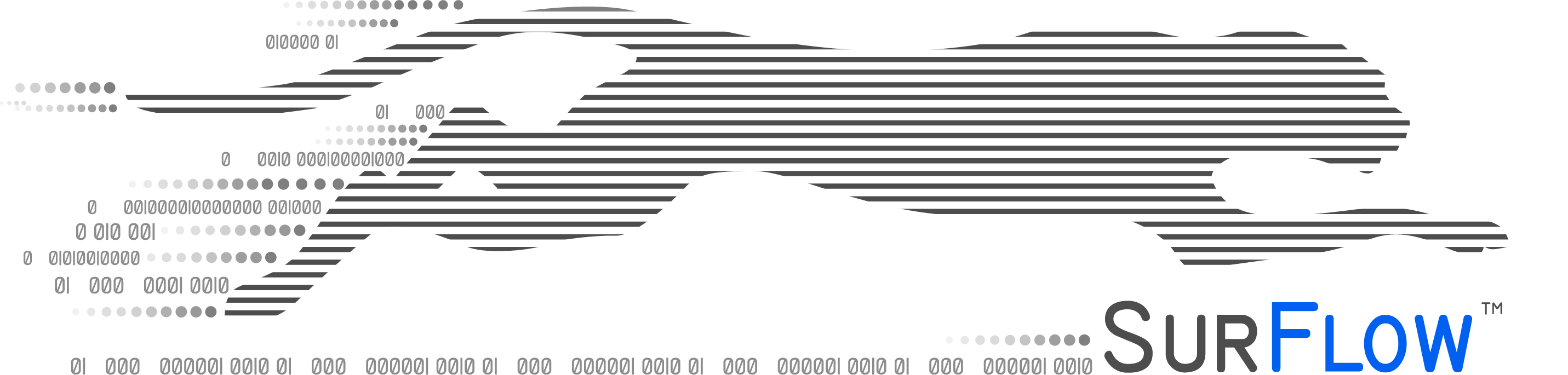
SurFlow: Future Composite Data Highways