By Stephen Cater
Industrial need
As the benefits and advantages of friction stir welded fabrications have become widely accepted, interest has grown in welding considerably thicker sections of aluminium and for these fabrications to be deployed in more demanding applications. Examples of such potential uses are structural reinforcing beams in marine and aerospace applications, undercarriage and bogie structures in railway rolling stock, cryogenic tanks for the storage and transport of liquefied natural and petroleum gases. Interest in joining aluminium alloys up to 75mm is now not unusual. Furthermore, this interest is spread across a wide range of alloy classes, with cryogenic applications tending to favour the work hardened 5xxx series alloys and the aerospace sector looking at heat treated 2xxx and 7xxx alloys in particular.
Key Findings
The state of the art for conventional FSW of thick section aluminium has been established. Fully consolidated welds can be made in both strain hardened and precipitation hardened aluminium alloys up to 75mm thick at industrially useful welding speeds.
- The welding performance envelope is acceptably wide, allowing manufacturers to tailor the process to their particular requirements.
- The TriFlat™ tool design has been shown to remain a useful, proven and robust design suitable for the welding of thick section aluminium alloys.
- The welds made have consistent microstructures and cross-weld tensile strength throughout the length of the steady state weld .
- A good baseline of data and process technique has been established against which it will be possible effectively to evaluate novel techniques currently under development for welding thick section aluminium alloys.
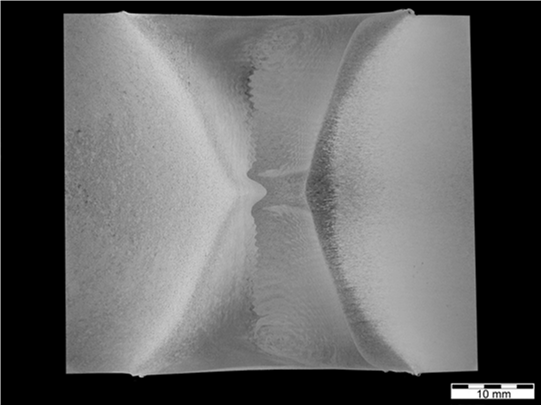
A weld in 50mm thick section aluminium alloy using the simultaneous double sided welding technique
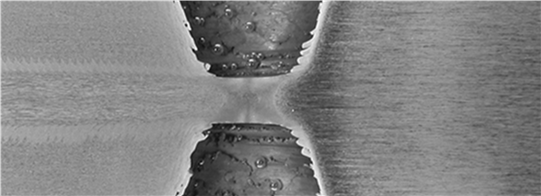
Micrograph showing flow between and around two directly opposed FSW tools in 50mm thick aluminium alloy