Development of Advanced Material Model for Metal Additive Manufacturing
TWI Industrial Member Report 1178-2023 [pdf / 668 KB]
By Tyler LondonMSc PSE CSci CEng CMath FIMA MWeldI andDamaso De Bono
EngD MEng PSE CEng MWeldI
Industrial Need
Whilst significant progress has been made in the last few years, the structural integrity and reliability of Additively Manufactured (AM) metallic parts remains a barrier to wide scale adoption by industry. This is principally due to the inability to robustly correlate the link between processing conditions, manufacturing defects, material structure, and mechanical performance. Whilst experimental trials can provide improved insight into these causal links, the number of variables to consider is excessively large, meaning that such experimentation would be exceptionally time-consuming and cost-prohibitive. Therefore, complementary activities, such as numerical modelling, can help address this problem.
Manufacturing process simulation, when properly verified and validated, can enable an improved understanding of the relationships between processing conditions, material properties, and the quality of the final part. Therefore, to improve the understanding of these fundamental relationships for PBF/LB, this project sought to develop, implement and validate a thermo-mechanical-metallurgical manufacturing process simulation.
Key Findings
- A manufacturing process simulation for PBF/LB Ti-6Al-4V that could predict temperature transients, distortion, residual stress and microstructure was developed and implemented.
- It is possible to use a continuum-scale, simplified modelling approach to accurately predict temperature transient, distortion and residual stress that occur during and arise as a consequence of laser powder bed fusion additive manufacturing. Despite not explicitly modelling the powder, ignoring fluid dynamics considerations, and not necessarily modelling layer-by-layer, the model can still account for a high-level of agreement with experimental measurements.
- Existing prediction methods for solid state phase transformations can predict the phase fractions in Ti-6Al-4V builds within 10-15% accuracy.
- A semi-empirical approach can be used to link local phase fraction to local stress-strain behaviour in Ti-6Al-4V parts. However, the Koistinen-Marburger (KM) models cannot predict the hierarchical structure of the martensitic alpha prime phase. This is a minor shortcoming, which may be overcome through more sophisticated modelling approaches that were beyond the scope of the present work.Opportunities to extend and validate the modelling framework on IN625 and AlSi10Mg samples arose. This additional work added to the confidence and validation of the general modelling approach. Moreover, whilst the report focuses specifically on PBF, the methods developed are applicable to direct energy deposition methods as well. Therefore, the project has enabled a step-change in the manufacturing process simulation capabilities for additive manufacturing.
Impact
- A manufacturing process simulation for the laser powder bed fusion processing of Ti-6Al-4V and other common AM alloys was developed and implemented.
- The manufacturing process simulations were validated through various experimental measurements.
- Opportunities for translating the model for laser powder bed fusion (L-PBF) processing to other AM processes such as direct energy deposition (DED) were identified.
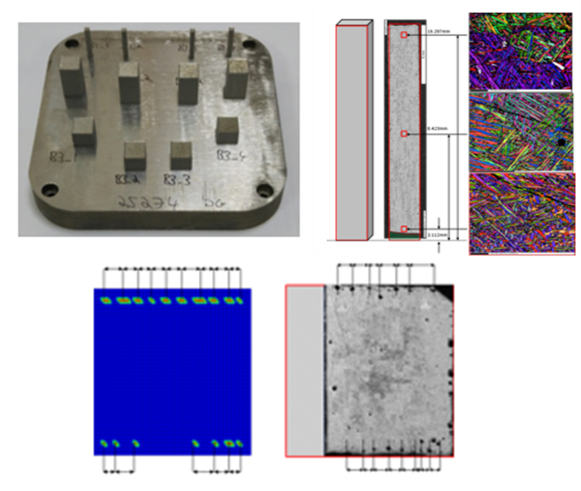
Metallurgical phase transformation framework applied to additive manufacturing processes: physical parts builds (top left), metallographic examinations (top right), physical state change prediction (bottom)