Integrity in Aggressive Environments
TWI Industrial Member Report 1159-2022 [pdf/ 1987 KB]
By Kuveshni Govender
Industrial Need
Pipelines and risers for oil production are increasingly required to carry sour fluids, ie containing significant levels of H2S. Depending on the precise chemistry of the environment, there may be a significant effect on the fatigue and stress corrosion resistance of girth welds in the pipe and risers. These effects must be taken into account in the design stage and when establishing flaw acceptance criteria for welding quality standards based on engineering critical assessment (ECA). For ECA, reliable fatigue crack growth rate (FCGR) data are required and generally the data are obtained using test specimens where the crack tip is exposed to an aqueous solution saturated with H2S gas. There are, however, operational conditions where nominally dry H2S gas is exported and this environment will be different and potentially less onerous than that for bulk aqueous sour systems.
There is limited data in the open literature showing the effect of low moisture contents in H2S gas on FCGRs in pipeline steel. This project investigated the effect of different moisture contents in a 7% H2S/bal.N2 gas mixture on FCGR behaviour of API X65 carbon manganese pipeline steel. A non-contact moisture analyser (NCMA) was used to measure both H2O and H2S content during the FCGR tests. The study also compared the FCGR data in the dry gas mixtures with data obtained in air and in an aqueous sour environment.
Key findings
-
· FCGRs in 7% H2S, bal. N2 gas with 2.5ppmv and 40ppmv H2O were similar. With moisture levels as low as 2.5ppmv, there was an enhancement in FCGR compared to in-air data. The FCGR curve obtained in the dry gases displayed three stages of crack growth. In the first stage in the low ΔK regime, the FCGR performance was the same as the in-air data suggesting the embrittling effect of hydrogen was insignificant. In the second stage, the FCGRs were higher than in air (up to 4 times at the transition point of Stages 2 and 3). This region was associated with the diffusion of hydrogen to the crack tip from an increase in the driving force from stress. The third region, which had a similar slope to the air curve, was influenced by the mechanical driving force when the crack tip was saturated with diffusible hydrogen.
-
Tests conducted in NACE solution B saturated with the 7%H2S, bal. N2 gas mixture, showed FCGRs up to 36.5x higher than in air. The two-stage FCGR behaviour is suggested to be controlled by the generation of hydrogen from the corrosion process, diffusion of hydrogen to the crack tip and the mechanical driving force. Diffusion of hydrogen is limited by the formation of a protective sulfide scale. The fact that testing in aqueous solutions gave rise to much higher FCGR compared to the data in dry H2S gas mixtures implies that for ECA purposes, the former may be too conservative and give rise to smaller tolerable flaw sizes.
-
The specimens tested in air showed a typical transgranular fatigue fracture surface whilst those tested in the dry gas showed transgranular fracture for Stage 1 (similar as fracture surface for air tests) and quasi-cleavage fracture for Stages 2 and 3. Specimens tested in the aqueous sour solution showed a mixture of transgranular/quasi-cleavage fracture in Stage 1 and quasi-cleavage in Stage 2. The latter is generally associated with a hydrogen embrittlement mechanism.
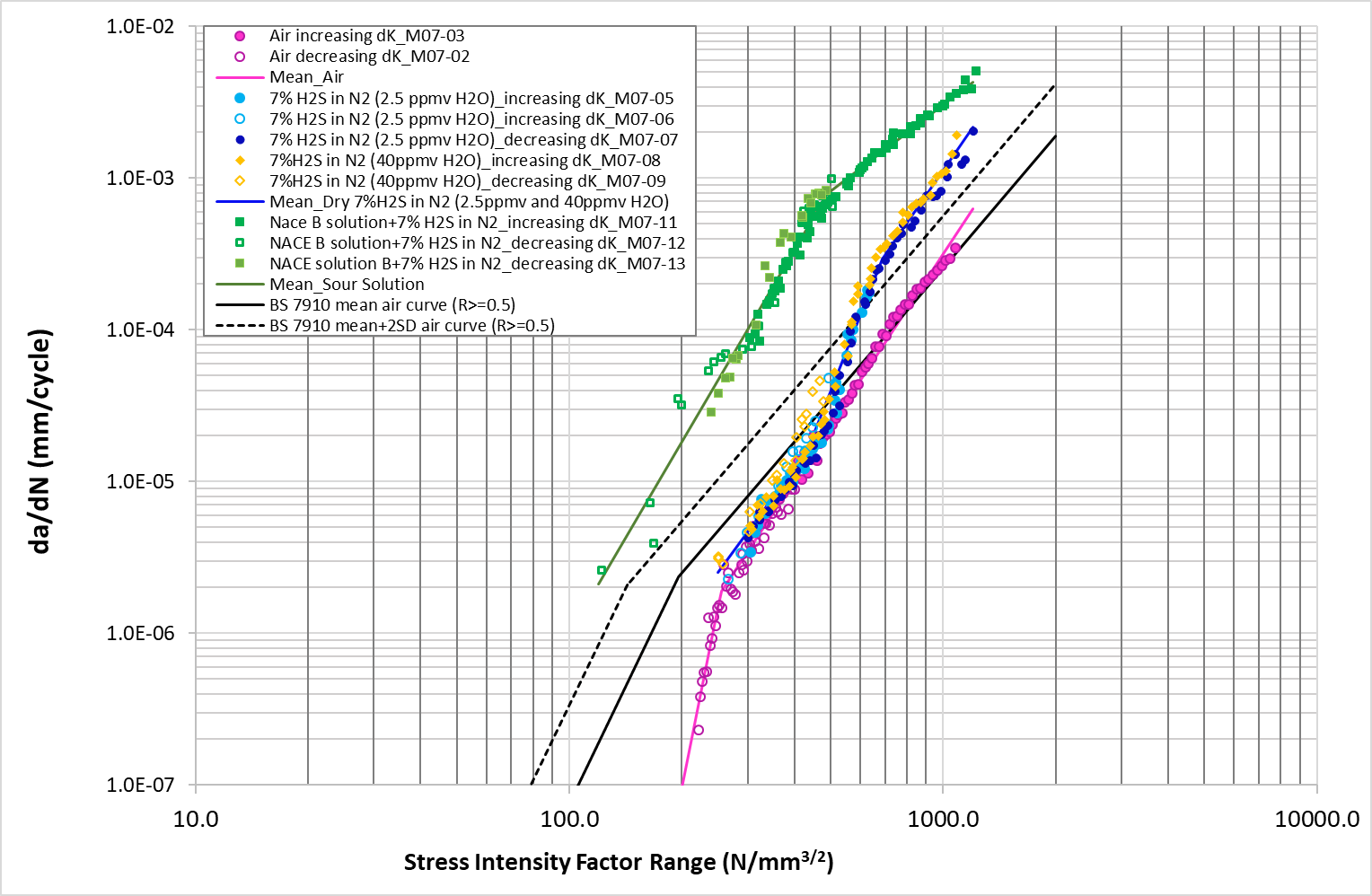
Comparison of FCGR in air, dry 7%H2S in bal. N2 (2.5ppmv and 40ppmv H2O) and NACE solution B saturated with 7%H2S in bal. N2. The BS 7910 mean and mean+2SD curves (R≥0.5) are included for comparison.