Linear Friction Welding of an Aluminium-Copper-Lithium Alloy
By Bertrand Flipo and Paul Clark
Industrial Need
Air traffic doubles every 15 years. The increasing use of lightweight materials in new single aisle aircraft leads to an increased demand for lithium containing alloy such as the aluminium-copper-lithium (Al-Cu-Li) alloy, 2099. Wasteful processing routes such as machining, lead to ‘buy-to-fly’ ratios as poor as 20:1 and rarely as good as 4:1. Limited global production capacity presents a clear need for a manufacturing route for components that reduces costs and achieves improved material utilisation.
Linear friction welding (LFW) is a rapidly developing solid-phase joining process that is attracting increasing industrial interest. Linear friction welding is already successfully established as a key manufacturing technology for critical aero-engine components such as Blisks (bladed discs), and is now being qualified for use on titanium alloy aero structures. Linear friction welding is potentially applicable to many materials, including non-fusion weldable alloys, advanced multiphase materials, and dissimilar material combinations.
This report describes the assessment of LFW for joining an Al-Cu-Li alloy, with the aim of demonstrating process capability to facilitate a concept whereby LFW could be used to build up structural parts, and/or to add materials/functionality, locally, to primary product forms, where desired.
Key findings
- An aluminium-copper-lithium alloy in the peak aged T8 condition can be welded using LFW.
- Weld positioning and machining both kept within 0.1mm of the nominal dimension.
- The LFW route potentially offers high speed of manufacture and significant cost savings for aluminium-lithium products, above a certain production volume threshold.
Full-scale wing rib demonstrator designed by TWI for techno-economic assessment
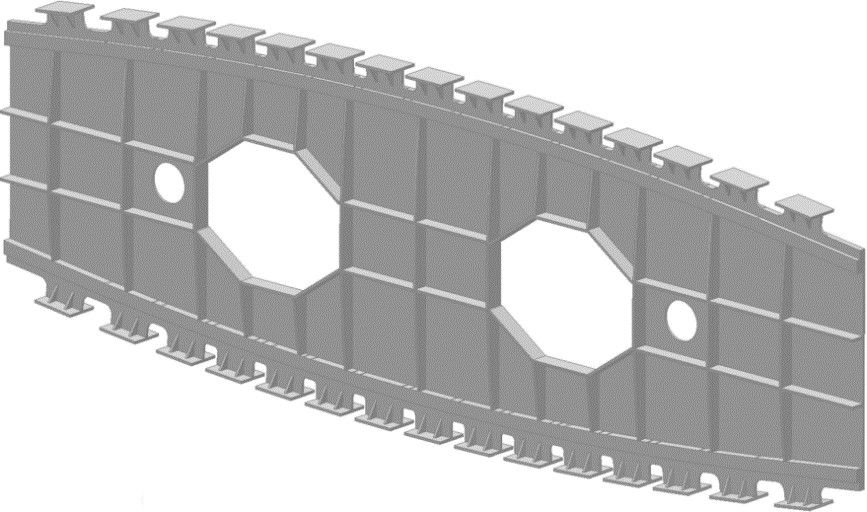
Longitudinal and transverse macrographs of a linear friction weld in Al-Cu-Li 2099 alloy
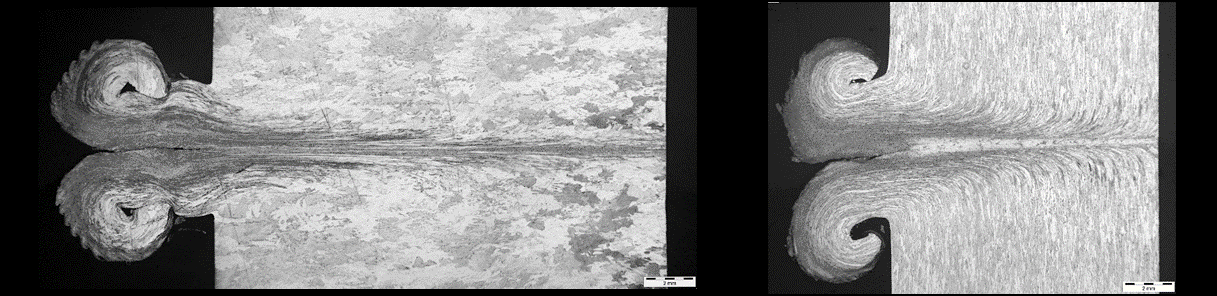