By Ewan Tarrant, Damaso De Bono and Tyler London
Background
As the metal additive manufacturing (AM) industry continues to grow, prediction of mechanical performance and control of distortion due to metal AM processes remains a significant problem. The ability to predict mechanical performance through finite element analysis (FEA) can reduce cost, waste production and negative impact on the environment, since numerical simulation removes the need for repeated pre-production trials.
This document critically reviews existing modelling approaches used to simulate selective laser melting (SLM), and establishes three benchmark geometries against which initial SLM finite element simulations can be compared. Thermo-physical and thermo-mechanical material properties for Ti‑6Al‑4V and In718 are extracted from various sources which may be used in these simulations. The modelling approaches reviewed are generally applicable to other metal AM technologies, and are not restricted to SLM.
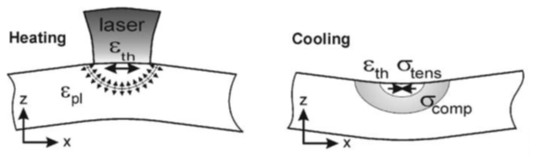
Tensile and compressive stresses lead to distortion of the build during SLM