Project Code: 33402
Start date and planned duration: October 2019, 30 months
Objectives
- To develop laser welding solutions for joining composite to metal parts in an overlap joint configuration.
- To integrate and validate intelligent fixturing and on-line quality assurance (QA), capable of performing real-time monitoring of weld depth during processing.
- To demonstrate the technology on industrially-relevant case studies from the aerospace and automotive sectors.
Project Outline
Due to stringent fuel economy regulations, automotive and aerospace companies are increasingly looking to reduce the weight of structures, through the use of dissimilar materials.
Joining dissimilar materials can be challenging and often beyond the capacity of conventional automated production processes. Currently, most challenging multi-materials assemblies are mechanically fastened and/or adhesive bonded. Limitations associated to using these two techniques include extra weight, cost and durability issues. These drawbacks limit the adoption of more advanced multi-material designs and reduce the potential benefits such optimised designs could achieve.
Consequently, there is a clear need for new, flexible, cost-effective and rapid methods for joining dissimilar materials, capable of meeting industry performance and manufacturing demands.
The project aims to develop an innovative technique to join composite to metal parts. Laser welding solutions with integrated real-time keyhole depth monitoring technology will be investigated, to produce a sound overlap weld between the metal plate part and a metallic interlayer, sprayed onto the composite substrate.
The technical approach will include three main steps, outlined in Figure 1.
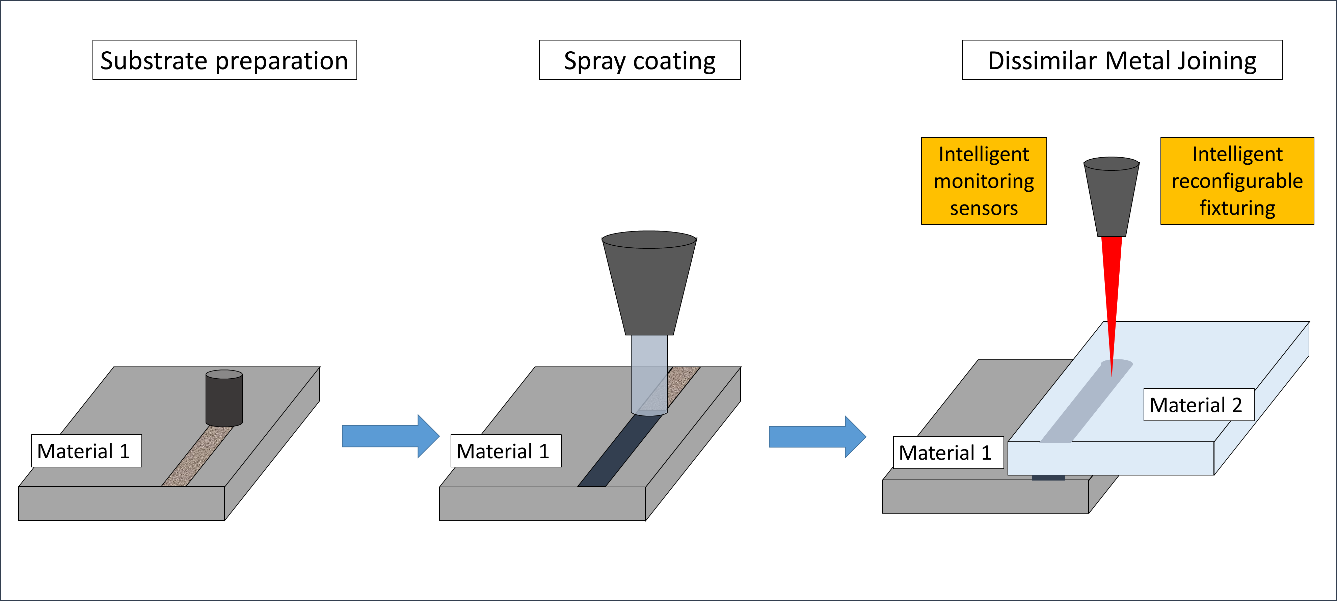
Figure 1 Schematic of proposed concept
Industry Sectors
- Aerospace
- Automotive
Benefits to Industry
The complementary project ULTIMATE is funded through Innovate UK and involves the following partners: CAV Aerospace, Gestamp, FAR-UK LTD, Curtiss-Wright Surface Technologies and TWI Ltd.
The project together with ULTIMATE will combine existing industrially proven technologies (i.e. metal spraying and laser welding) in a novel way to further enable high quality and high productivity joining of challenging dissimilar material combinations (such as composite to aluminum).
The novel manufacturing capability may be adopted by members in the transport sector enabling the uptake of advanced light-weight solutions. Larger design flexibility, cost effectiveness and novel product development will be used by end users for growing their businesses and extend their market position.