Das Pulverbettschmelzen (Powder Bed Fusion, PBF) ist ein additives Fertigungsverfahren und funktioniert auf folgendem Grundprinzip: Die Teile werden durch Hinzufügen von pulverförmigem Material geformt, anstatt festes Material durch herkömmliche Formgebungsverfahren wie das Fräsen zu entfernen. Das PBF-Verfahren beginnt mit der Erstellung eines 3D-CAD-Modells, das numerisch in mehrere diskrete Schichten „zerlegt“ wird. Für jede Schicht wird ein Wärmequellen-Scanpfad berechnet, der sowohl die Grenzkontur als auch eine Form der Füllsequenz definiert, häufig ein Rastermuster, da die Wärmequelle in der Regel ein Energiestrahl (z. B. ein Laser) ist.
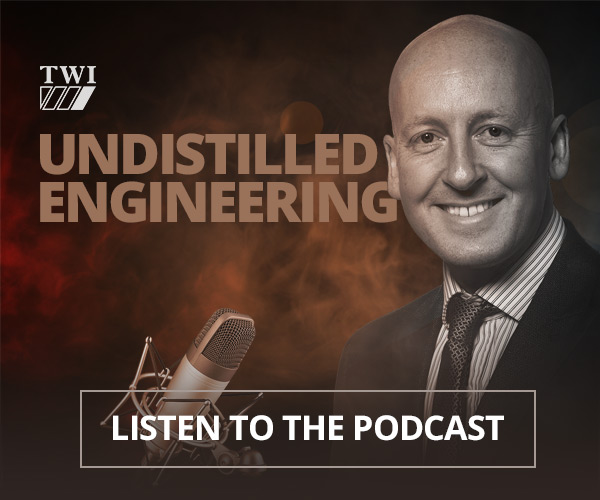
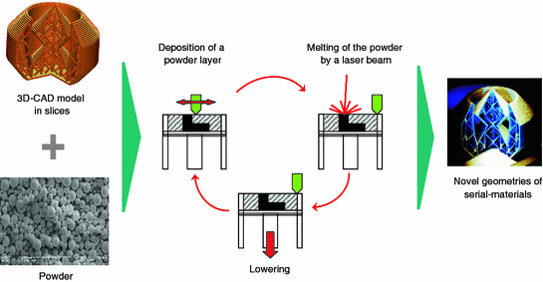
Die einzelnen Schichten werden dann nacheinander übereinander geklebt. Beim PBF-Verfahren wird das pulverförmige Material über die zuvor zusammengefügte Schicht gestreut, so dass die Verarbeitung der nächsten Schicht erfolgen kann. Das pulverförmige Material wird über einen Trichter zugeführt und mit Hilfe einer Walze oder eines Messers gleichmäßig über die Bauplattform des Pulverbettes verteilt. Die optimale Schichtdicke des aufgestreuten Pulvers hängt von den Verarbeitungsbedingungen und dem verwendeten Material ab, doch sind Werte von 25 bis 100 µm üblich.
Welche Verfahren gibt es beim Pulverbettschmelzen?
Es gibt mehrere Verfahren zum Pulverbettschmelzen, die nach der verwendeten Wärmequelle und der Art des zu verbindenden Materials unterschieden werden. Die beiden vorherrschenden Verfahren sind das Laserstrahlverfahren (PBF-LB) und das Elektronenstrahlverfahren (PBF-EB), für die es jeweils markenrechtlich geschützte Verfahrensvarianten gibt. Jede Variante bietet Vor- und Nachteile, so dass die Eignung von Anwendung zu Anwendung abgewogen werden sollte. Beispiele sind unten aufgeführt:
Selektives Laser-Sintern (SLS)
SLS ist ein markenrechtlich geschützter Begriff für eines der Laserstrahlverfahren. Das Verfahren sintert in der Regel pulverförmige Polymermaterialien wie Nylon und Polyetherketonketon (PEKK).
Selektives Laserschmelzen (Selective Laser Melting, SLM)
SLM ist ein markenrechtlich geschützter Begriff für ein weiteres Laserstrahlverfahren, das insofern mit SLS vergleichbar ist, als ein Laser zur Wärmezufuhr verwendet wird, der Laser schmilzt das Pulver jedoch vollständig auf, anstatt es zu sintern. Das Verfahren wird bei Metallpulvern wie Aluminiumlegierungen, Titan und seinen Legierungen sowie Edelstahl angewendet. Auch exotischere Metalle (z. B. Wolfram) können verarbeitet werden, sind aber eher anwendungsbezogen. In der Baukammer herrscht eine inerte Atmosphäre (in der Regel Argon), um eine Oxidation und/oder Nitrierung des konsolidierten Materials zu verhindern.
Direktes Metall-Laser-Sintern (DMLS)
DMLS ist eine Marke der EOS GmbH, einem deutschen Unternehmen für additive Fertigung, und ähnelt in seiner Funktionsweise dem SLM. Obwohl der Begriff „Sintern“ verwendet wird, wird ein vollständiges Schmelzen erreicht. TWI ist das erste britische Unternehmen, das über ein zertifiziertes Verfahren für die Herstellung mit dieser Technologie verfügt.
Elektronenstrahlschmelzen (Electron Beam Melting, EBM)
Elektronenstrahlschmelzen ist ein mit dem SLM vergleichbares Verfahren, bei dem der Laser durch eine Elektronenkanone ersetzt wird. Es ist daher ein PBF-EB-Verfahren. Aufgrund der Verwendung eines Elektronenstrahls wird in der Baukammer ein Vakuum anstelle einer Schutzgasatmosphäre verwendet, obwohl eine geringe Menge Schutzgas (in der Regel Helium) für eine bessere Prozesskontrolle eingesetzt wird.
Nachbearbeitung
Die Nachbearbeitung von PBF-Bauteilen ist in der Regel erforderlich, um sie für die vorgesehenen Anwendungen zu optimieren: Dies gilt insbesondere für Metalle und Legierungen. Dies kann aus den folgenden Gründen geschehen:
- Verbesserung der mechanischen Eigenschaften (durch Wärmebehandlung)
- Verringerung der Eigenspannung (durch Wärmebehandlung)
- Verbesserung der Oberflächengüte (durch chemisches oder Laserpolieren und/oder Strahlen)
Was sind die Vorteile des Pulverbettschmelzens?
Zu den Vorteilen des Pulverbettschmelzens gehören:
- Geringerer Materialverlust und geringere Kosten (besseres Verhältnis zwischen Anschaffung und Verbrauch)
- Verbesserte Produktionsentwicklungszeiten
- Ermöglichung von Rapid Prototyping und Kleinserienfertigung
- Herstellung von funktional abgestuften Teilen
- Vollständig kundenindividuelle Teile auf Chargenbasis, wodurch feste Konstruktionen vermieden werden
- Gute Auflösung im Vergleich zu anderen additiven Fertigungsverfahren
- Effizientes Recycling von ungeschmolzenem Pulver
- Fähigkeit, viele Materialqualitäten zu verbinden, darunter Keramik, Glas, Kunststoffe, Metalle und Legierungen
- Keine Notwendigkeit für Bearbeitungsvorrichtungen mehr
Welche Anwendungsmöglichkeiten bietet Pulverbettschmelzen?
Pulverbettschmelzen wird in einer Vielzahl von Industriezweigen für zahlreiche Anwendungen eingesetzt. So wird das Verfahren zum Beispiel in der Medizintechnik zur Herstellung von maßgeschneiderten orthopädischen Komponenten wie Schädel- oder Hüftgelenkimplantaten aus Titanlegierungen eingesetzt.
Aus Sicht der Luft- und Raumfahrt finden PBF-Verfahren großes Interesse und Verwendung in Militär- und Verkehrsflugzeugen. Ein Beispiel dafür ist die im PBF-Verfahren hergestellte Treibstoffdüse des GE9X-Triebwerks von General Electric, das in Boeing 777-Flugzeugen eingesetzt wird. Das GE9X ist das größte produzierte Turbofan-Triebwerk, und die additiv gefertigte Düse ist fünfmal haltbarer als frühere Versionen.[1] Die Boeing 777 mit ihren beiden GE9X-Triebwerken enthält 300 additiv gefertigte Teile.[2]
Der schwedische Automobilhersteller Koenigsegg hat PBF-Techniken während des gesamten Herstellungsprozesses seines neuesten Hypercars, des "One:1", eingesetzt, angefangen beim Rapid Prototyping, um sicherzustellen, dass verschiedene Details des Fahrzeugs so aussehen und funktionieren, wie man es sich vorstellt, bis hin zur Herstellung von Metallteilen für Serienfahrzeuge. Zu den Produktionsteilen gehören Turboladergehäuse, Auspuffkomponenten, Luftkanäle und Innenspiegel.[3] Die additiven Fertigungsverfahren ermöglichten Koenigsegg eine Reduzierung des Materialabfalls und der Kosten. Bei Kleinserien (wie sie bei High-End-Autos üblich sind) ist die Herstellung komplexer Teile durch additive Fertigung billiger, schneller und effizienter als der Bau der erforderlichen Werkzeuge für die Produktion bestimmter komplexer Teile, wie er in der Automobilindustrie üblich ist.[3]
Wie kann TWI helfen?
TWI unterstützt seine industriellen Mitglieder vielen Aufgaben und Herausforderungen im Bereich der additiven Fertigung einschließlich Binder Jetting und Powder Bed Fusion. TWI arbeitet seit langem mit seinen Mitgliedern und an gemeinsamen Projekten in verschiedenen Industriezweigen zusammen, um die additive Fertigung zu unterstützen. TWI verfügt über einen beträchtlichen kollektiven Erfahrungsschatz in verschiedenen Bereichen der Nutzung der verschiedenen Technologien in weitreichenden Anwendungen.
TWI ist eine auf industrieller Mitgliedschaft basierende Organisation. Die Experten von TWI können Ihrem Unternehmen eine Ergänzung zu Ihren eigenen Ressourcen bieten. Unsere Mitarbeiter haben es sich zur Aufgabe gemacht, der Industrie bei der Verbesserung von Sicherheit, Qualität, Effizienz und Rentabilität in allen Aspekten der Schweiß- und Fügetechnik zu helfen. Die industrielle Mitgliedschaft im TWI erstreckt sich derzeit auf über 600 Unternehmen weltweit und umfasst alle Industriezweige.
Quellen
[1] World's First Plant to Print Jet Engine Nozzles in Mass Production. GE News, 14. Juli 2014.
[2] Boeing 777X's first flight with more than 300 3D printed parts. 3Dnatives, 29. Januar 2020.
[3] Koenigsegg Harnesses Additive Manufacturing for the One:1. Digital Engineering 24/7, 21. April 2014.