CoreFlow™ ist eine Weiterentwicklung des Rührreibschweißens (Friction Stir Welding, FSW) und des Rührreibkanalisierens (Friction Stir Channelling, FSC), die es in einem einzigen Fertigungsschritt ermöglicht, unter der Oberfläche liegende Kanäle von Kühlkreisläufen in zwei- oder dreidimensionale monolithische Teile zu integrieren.
Technische Fragen
Welche Werkstoffe können mit CoreFlow™ bearbeitet werden?
Aluminium AA6082-T6 und AA1050-H14 Bleche und Platten mit einer Dicke von 5 bis 50 mm wurden erfolgreich verarbeitet. CoreFlow™ wurde schon für flache und rohrförmige Demonstratoren eingesetzt, die Kanäle entlang linearer, gekrümmter und schraubenförmiger Bahnen aufweisen. Die Demonstratoren haben sowohl Leckage- als auch Drucktests bestanden, mit Leckageraten deutlich unter 10-8 mbar/s und einem Druck von bis zu 9 bar.
Das Verfahren wird derzeit auf andere Aluminiumlegierungen und auf Kupfer, das im Vergleich zu Aluminium verbesserte thermische Eigenschaften aufweist, portiert und getestet. Darüber hinaus sind Magnesium und Titan die nächsten metallischen Kandidaten, an denen der Prozess getestet werden soll.
Es wird erwartet, dass CoreFlow™ nicht nur für Metalle sondern auch für Thermoplaste einsetzbar ist, da auch Rührreibschweißen (Friction Stir Welding, FSW) und Linearreibschweißen (Linear Friction Welding, LFW) von Kunststoffen bereits bewährte und etablierte Technologien sind. Die Anwendung von CoreFlow™ auf Thermoplaste wie PEEK eröffnet eine breite Palette neuer Möglichkeiten, um Metalle und Keramiken in einigen Anwendungen zu ersetzen. Zu den Anwendungen gehören Kühlkörper auf Leiterplatten und in der Hochleistungselektronik sowie für Kühlkanäle in Wärmetauschern, in Haushaltsgeräten, Beleuchtungseinrichtungen, Telekommunikationsgeräten, Rechenanlagen und Industrieanlagen, die in korrosiven Umgebungen eingesetzt werden. Von großem Interesse ist die Anwendung von CoreFlow™ für Spritzgussformen und ähnliche Formwerkzeuge.
Wie groß ist der Verzug im Vergleich zu konventionellen Kanalformverfahren?
CoreFlow™ nutzt Reibung, um Wärme zu erzeugen und das Material um den Stift herum zu plastifizieren, daher verursacht es einen gewissen Verzug. Die dabei auftretenden Spitzentemperaturen sind ähnlich wie beim FSW (Rührreibschweißen) und erreichen bis zu 90 % der Materialschmelztemperatur. Im Vergleich zum FSW ist das CoreFlow™-Wärmeprofil jedoch stärker lokalisiert. Daher sind die bei CoreFlow™ zu erwartenden Verformungswerte ähnlich (oder sogar geringer) als beim FSW.
Wenn statt CoreFlow™ ein Schmelzschweißverfahren zum Abdichten des Deckels nach der Bearbeitung verwendet wird, sind die Spitzentemperaturen, die das Material erfährt, höher als bei CoreFlow™, was zu einem stärkeren Verzug führen kann. CoreFlow™ führt aber meist zu etwas mehr Verzug als das Fräsen des Kanals aus dem Vollen und das anschließende Verschrauben oder Verlöten eines Deckels zur Abdichtung des Kanals.
Ein Gleichgewicht zwischen mehreren Faktoren wird angestrebt, darunter:
- Gesamtprozessdurchsatz und Kosten
- Dichtungszuverlässigkeit und Druckleistung
- Wartungskosten im Zusammenhang mit Dichtungen und Bolzen
- Zusätzliche Kosten für Vor- und Nachbearbeitung
Gibt es eine prozessbedingte Verschlechterung der mechanischen Eigenschaften?
Bei der Verarbeitung mit CoreFlow™ wärmebehandelbaren Legierungen (2xxx, 6xxx und 7xxx) im T6-Zustand wird eine Reduzierung der Festigkeit in der Wärmeeinflusszone beobachtet. Bei T4-Zuständen oder bei kaltverfestigten Legierungen (1xxx und 5xxx) ist dies nicht zu erwarten.
Ein ähnliches Verhalten sollte für andere untersuchte Metalle (z.B. Cu, Ti, Mg) erwartet werden.
Wie hoch ist die Bearbeitungsgeschwindigkeit von CoreFlow™?
Die Ausbildung und Geometrie des Kanals wird durch das Verhältnis zwischen der Stiftdrehzahl und ihrer Verfahrgeschwindigkeit beeinflusst.
Zu Beginn der Entwicklung wurde die Kombination von Drehzahlen von 400-600 U/min und Verfahrgeschwindigkeiten von 25-50 mm/min für rechteckige Querschnitte in 15 mm dicken Aluminiumplatten aus AA6082-T6 eingesetzt. Für eine bestimmte Kanalgeometrie kann der Prozess weiter optimiert werden, indem sowohl die Verfahrgeschwindigkeit als auch die Rotationsgeschwindigkeit erhöht werden, ihr Verhältnis also konstant gehalten wird. Diese Optimierung erfordert jedoch einen hohen Aufwand und ihre Ergebnisse sind auf ein bestimmtes Material und bestimmte Stiftabmessungen beschränkt. Darüber hinaus könnte eine Steigerung der Leistung und des Durchsatzes durch eine Änderung der Stiftkonstruktion erreicht werden, z. B. durch die Einführung zusätzlicher Merkmale oder durch die Optimierung des Extrusionsweges.
Durch die Bearbeitung des Hohlraums und das Abdichten der Kühlkanäle in einem einzigen Arbeitsschritt führt CoreFlow™ mehrere Fertigungsschritte gleichzeitig aus und bietet damit einen verfahrenstypischen Vorteil im Vergleich zu herkömmlichen Technologien, z. B. dem Fräsen mit anschließendem Abdichten durch Löten, Verschrauben oder Schweißen. Dies führt zu einem einfacheren Prozess und einer effizienteren und umweltfreundlicheren Herstellungsmethode, die weniger Rohstoffe verbraucht, weniger Abfall produziert und daher weniger wiegt als das konventionell durch Fräsen und Versiegeln hergestellte Gegenstück.
Es sei jedoch angemerkt, dass CoreFlow™ ein neuartiges Verfahren ist, das sich noch in ständiger Entwicklung befindet. Auch das FSW-Verfahren war anfangs, nachdem es 1991 am TWI erfunden worden war, im Vergleich zu den gängigen Schmelzschweißtechnologien ein langsamer Prozess. TWIs Erfahrung in Innovation und Prozessentwicklung ermöglichte es, die Geschwindigkeit des FSW-Verfahrens innerhalb von wenigen Jahren erheblich zu steigern und die Wettbewerbsfähigkeit des Prozesses drastisch zu verbessern. Der Schlüssel zur Erzielung höherer Verarbeitungsgeschwindigkeiten liegt in der FSW-Werkzeugkonstruktion, einem der wichtigsten Kompetenzbereiche von TWI.
Wie groß ist die Oberflächenrauheit der Innenwände?
Die Abbildung unten zeigt das Oberflächenprofil jeder der Innenflächen aus unseren Versuchen an AA6082-T6-Platten mit einer Dicke von 15 mm.
Der Boden des Kanals ist die glatteste Innenfläche und weist einen Ra von 1,27 µm auf. Diese Oberflächengüte entspricht dem Qualitätsbereich, der beim Schaftfräsen erreicht wird (typischerweise zwischen 0,8 und 6,3 µm). Auf der unteren Oberfläche ist ein lineares Muster kreisförmiger Riffel zu erkennen, die von der Vorderkante des Stifts erzeugt werden (Teilbild a). Die Deckenoberfläche weist ebenfalls ein lineares Muster kreisförmiger Markierungen auf, allerdings mit entgegengesetzter Richtung zu der der Bodenoberfläche (Teilbild b). Die Decke weist eine rauere Textur auf, was sich in dem höheren Ra-Wert von 25,49 µm widerspiegelt.
Die Seitenwände an der AS (advancing side) und der RS (retreating side) weisen Ra-Werte von 18,61 bzw. 25,11 μm auf. Wie in der Abbildung (Teilbilder c, d) dargestellt, sind beide Oberflächen durch eine schuppenartige, von der Fahrtrichtung wegweisende Morphologie gekennzeichnet.
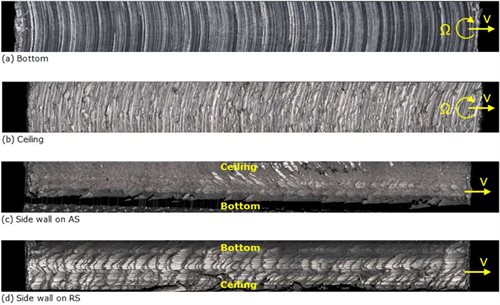
Charakterisierung der Rauheit der Kanalinnenfläche: (a) Boden; (b) Decke; (c) Seitenwand auf der AS (advancing side); (d) Seitenwand auf der RS (retreating side).
Die Herstellung konsistenter und wiederholbarer Rauheitswerte kann ein Konstruktionsmerkmal sein. Einige Wärmetauscher sind texturiert, um Turbulenzen im Kühlmittel zu fördern, da dieses Strömungsregime die Wärmeabfuhr durch Konvektion verbessert. Für Produkte, die eine laminare Strömung erfordern, entwickelt TWI Methoden zur Verbesserung der inneren Oberflächenbeschaffenheit durch Prozessoptimierung oder Nachbearbeitungstechniken. Einige Beispiele sind chemisches Ätzen, abrasive Strömungsbearbeitung (abrasive flow machining, AFM) oder fluidbettunterstützte abrasive Strahlbearbeitung (fluidised bed assisted abrasive jet machining, FB-AJM).
Wie eng können zwei benachbarte Kanäle positioniert werden?
Kanäle, die durch eine nur 1-2 mm dünne Materialwand getrennt sind, wurden erfolgreich in AA6082-T6 mit einer Dicke von 5 mm hergestellt. Es wurden jedoch unterschiedliche thermische Effekte durch den Wärmestau bei der Nachbearbeitung eines kleinen lokalen Bereichs mit mehreren Durchgängen beobachtet. Um dies abzumildern, ist eine Prozessoptimierung erforderlich.
Eines der neuesten Forschungsthemen ist die Erzeugung nicht nur von Kanälen, sondern auch von Bereichen unter der Oberfläche. Dies wäre nützlich, um Reservoirs für den Transport von Flüssigkeiten, die Einbettung von Instrumenten oder die Gewichtsreduzierung bestehender Strukturen zu bilden.
Welche Eigenschaften hat das Draht-Nebenprodukt, das CoreFlow™ produziert?
TWI erforscht, ob das Material, das in Form von Draht aus der Platte extrudiert wird, als Ausgangsmaterial für andere Prozesse verwendet werden kann, z. B. für die drahtbasierte additive Fertigung oder als Füllstoff beim Schmelzschweißen. CoreFlow™ ist in der Lage, eine unbegrenzte Länge an Draht aus einer Platte oder einem Rohr zu extrudieren.
Dieser Prozess, der als ForgeWire™ bezeichnet wird, ist von großem Interesse für die Herstellung einer Drahtspule aus schlecht extrudierbaren Materialien, wie Aluminium- oder Magnesiumlegierungen. Drahthersteller oder Entwickler von additiven Fertigungsverfahren haben nun eine schnelle Option zur Herstellung von Draht mit maßgeschneiderter chemischer Zusammensetzung und aus experimentellen Legierungsrezepturen (z. B. Aluminium-Lithium oder Aluminium-Scandium), möglicherweise sogar direkt aus dem Walzprodukt oder gegossenen Knüppeln.
Für welche Anwendungen könnte CoreFlow™ eingesetzt werden?
CoreFlow™ ist bereits auf dem Weg, revolutionäre Anwendungen bei der Herstellung von Wärmetauschern, Kühlsystemen, integriertem Fluidmanagement und dem Leichtbau von Strukturen zu finden.
Hier eine Liste möglicher Anwendungen:
- Elektroauto-Batteriewannen mit integrierten Kühlkanälen, die in die Metallstruktur eingebaut sind.
- Einbau von Kanälen in dünnwandige Elektromotorgehäuse zur aktiven Kühlung, wodurch das Gewicht reduziert und die Motorleistung verbessert wird.
- Kühlung von Flugzeugtriebwerken durch direkt in die Gondeln integrierte Kanalnetze.
- Hydraulische Kühlsysteme, die es ermöglichen, Schläuche, Rohre und Armaturen zu ersetzen.
- Kühlung von Datenservern, Kommunikationsinfrastrukturen und Radaranlagen.
- Bewältigung der thermischen Belastung in Fertigungsanlagen.
- Netzwerke für die Schmiermittelzuführung.
- Einbettung von Instrumenten in eine Struktur.
- Interne Kabelführung zum Verlegen von innen geführten Kabeln und Bowdenzügen.
- Zusätzliche Gewichtsreduzierung von bestehenden Teilen.
Erfordert CoreFlow™ eine spezielle Ausrüstung?
Die meisten Versuche wurden auf einer ESAB SuperStir™-Maschine (siehe Abbildung unten), einem speziell angefertigten FSW-Portalsystem durchgeführt, das mit dem proprietären stationären Schultersystem von TWI ausgestattet ist.
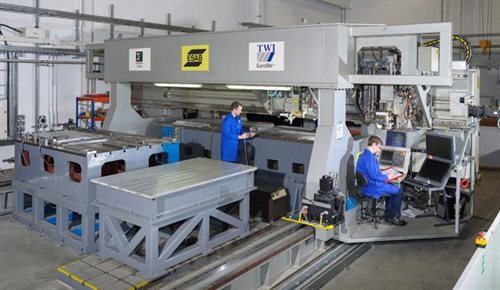
Der verwendete Stift ist ein zylindrischer, proprietärer Gewindestift aus einer Kobalt-Nickel-Chrom-Legierung, kombiniert mit einer statischen flachen Schulter. Die Schulter verfügt über vier orthogonal angeordnete, radiale Entlüftungslöcher, um den Austritt des plastifizierten Materials zu ermöglichen. Stift und Schulter sind speziell für das zu bearbeitende Material und die gewünschte Anwendung ausgelegt.
Die nächste Stufe in der Evolution von CoreFlow™ ist die Entwicklung eines Universalkopfes für CNC-Fräsmaschinen und Roboterarme, wodurch das Verfahren mit einer geringen Investition umsetzbar wird. Für FSW wurden von TWI bereits Universalkopf-Systeme entwickelt.
Für 2021 sind Roboterversuche geplant, bei denen ABB-Roboter mit einem CoreFlow™-Werkzeug instrumentiert und zum Einbetten von Kanälen in dreidimensionale metallische Oberflächen eingesetzt werden sollen.
Welche Kanalgeometrien können realisiert werden?
Die Kanalquerschnittsgeometrie scheint je nach den verwendeten Parametern von rechteckig bis dreieckig zu variieren. Alle Kanäle weisen eine ebene Bodenfläche auf, die konsistent mit der verwendeten Stiftlänge ist. Der Boden des Kanals weist gut definierte Kanten auf, die mit der Stiftkontur übereinstimmen.
In Zukunft können weitere Formen durch Veränderung der Prozessparameter und der Stiftform realisiert werden. Darüber hinaus könnten durch eine dynamische oder schrittweise Änderung der Stiftlänge 3D-Geometrien erreicht werden und Kanäle auf mehreren Tiefenebenen erzeugt werden, die sich kreuzende und komplexere Muster ermöglichen.
Was ist die maximale Tiefe, Breite und Deckendicke eines CoreFlow™-Kanals?
Die Abmessungen des Kanals, einschließlich seiner Tiefe, hängen hauptsächlich von der Geometrie des Stifts ab. Eine Faustregel für Werkzeuge, die üblicherweise beim FSW eingesetzt werden, ist, dass das Aspektverhältnis unter 0,5 liegen sollte, was bedeutet, dass seine Länge etwas länger (bis zum 2-fachen) als sein Durchmesser sein könnte. Dies wiederum bedeutet, dass die Kanaltiefe bis zum Doppelten der Kanalbreite betragen kann.
Die Deckendicke hängt nicht nur von der Stiftkonstruktion sondern auch von den verwendeten Prozessparametern ab. Eine Erhöhung der Stiftrotationsgeschwindigkeit erhöht beispielsweise die Extrusionsrate, wodurch weniger Material im Kanal zurückbleibt und somit eine dünnere Kanaldecke entsteht.
Kommerzielle Fragen
Ich weiß nicht, wie ich meine Produkte für CoreFlow™ auslegen soll - wie kann TWI helfen?
TWI bietet alles, von der Beratung bei der Konstruktion von Komponenten, der Auswahl von Prozessen und Qualitätsproblemen, der Fehlersuche, Machbarkeitsbewertungen und Vorproduktionsversuchen bis hin zur Entwicklung von Anwendungen und Prototypanlagen. TWI bietet seinen Mitgliedern und anderen Interessenten Zugang zum neuesten Stand der Technik in den Bereichen Schweißen, Fügen, Inspektion und Zusatztechnologien, die in verschiedenen Industriezweigen anwendbar sind. Unsere Forschungseinrichtungen erstrecken sich auch auf die Bewertung der strukturellen Integrität und die Materialcharakterisierung.
Mit diesen Fähigkeiten kann TWI Sie bei der Entwicklung und dem Prototyping der nächsten Generation Ihrer Produkte unter Verwendung von CoreFlow™ als Basistechnologie unterstützen.
Wie ist der patentrechtliche Status der CoreFlow™-Technologie?
TWI hat Patentschutz in Gebieten auf der ganzen Welt beantragt, basierend auf der PCT-Publikationsnummer WO2018083438.
Wie erfahre ich mehr über den Erwerb einer Lizenz zur Nutzung von CoreFlow™?
TWI beabsichtigt, Lizenzen unter den CoreFlow™-Patenten auf Standortbasis anzubieten, in Anlehnung an das FSW-Modell. In diesem System würde sich die Lizenzgebühr nach der Anzahl der Standorte richten, an denen CoreFlow™ eingesetzt wird (und nicht nach der Menge der verarbeiteten Teile oder verkauften Produkte). TWI ist jedoch jederzeit bereit, diese Regelung von Fall zu Fall zu überprüfen, um der Übernahme und Verbreitung der Technologie Vorrang zu geben.
Für weitere Informationen zur Lizenzierung dieser Technologie kontaktieren Sie bitte die IP-Abteilung von TWI unter ipr@twi.co.uk .
Gibt es technische Veröffentlichungen zu CoreFlow™?
Es wurden mehrere technische Publikationen zu CoreFlow™ erstellt und veröffentlicht:
Weitere Fragen?
Dieser Artikel gehört zu einer Reihe von häufig gestellten Fragen (FAQs). Weitere Informationen zu diesem Thema finden Sie in im „CoreFlow™ - Technology Launch Webinar“ auf unserer Website. Bei weiteren Fragen senden Sie bitte eine englischsprachige E-Mail an:
kontakt@twi-deutschland.com