The characteristic features and principal causes of incomplete root fusion and penetration are described. General guidelines on 'best practice' are given so welders can minimise the risk of introducing imperfections during fabrication.
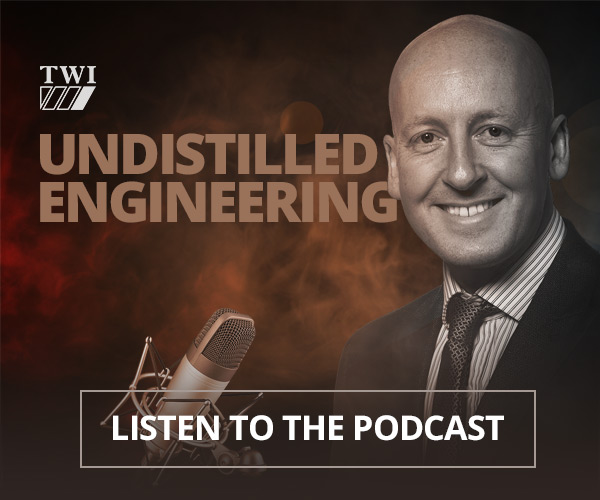
Fabrication and service defects and imperfections
As the presence of imperfections in a welded joint may not render the component defective in the sense of being unsuitable for the intended application, the preferred term is imperfection rather than defect. For this reason, production quality for a component is defined in terms of a quality level in which the limits for the imperfections are clearly defined, for example Level B, C or D in accordance with the requirements of BS EN ISO 5817. For the American standards ASME IX and AWS D1.1, the acceptance levels are contained in the standards.
The application code will specify the quality levels which must be achieved for the various joints.
Imperfections can be broadly classified into those produced on fabrication of the component or structure and those formed as result of adverse conditions during service. The principal types of imperfections are:
fabrication:
- lack of fusion
- lack of or incomplete penetration
- cracks
- porosity
- inclusions
- incorrect weld shape and size
service:
- brittle fracture
- stress corrosion cracking
- fatigue failure
Welding procedure, joint features and access and welder technique will have a direct effect on fabrication imperfections. Incorrect procedure or poor technique may produce imperfections leading to premature failure in service.
Incomplete root fusion or penetration
Identification
Incomplete root fusion is when the weld fails to fuse one side of the joint in the root. Incomplete root penetration occurs when both sides root region of the joint are unfused. Typical imperfections can arise in the following situations:
- an excessively thick root face in a butt weld (Fig. 1a)
- too small a root gap (Fig. 1b)
- misplaced welds (Fig. 1c)
- failure to remove sufficient metal in cutting back to sound metal in a double sided weld (Fig. 1d)
- incomplete root fusion when using too low an arc energy (heat) input (Fig. 1e)
- too small a bevel angle,
- too large a diameter electrode in MMA welding (Fig 2)
Fig. 1 Causes of incomplete root fusion
Fig. 2 Effect of electrode diameter on root fusion and penetration
Causes
These types of imperfection are more likely in consumable electrode processes (MIG, MAG, FCAW, MMA and SAW) where the weld metal is 'automatically' deposited as the arc consumes the electrode wire or rod. The welder has limited control of weld pool penetration independent of depositing weld metal. Thus, the non consumable electrode TIG process in which the welder controls the amount of filler material depoisted independent of penetration is less prone to this type of defect.
In MMA welding, the risk of incomplete root fusion and root penetration can be reduced by using the correct welding parameters and electrode diameter to give adequate arc energy input and satisfactory penetration. Electrode diameter is also important in that it should be small enough to give adequate access to the root, especially when using a small included vee angle (Fig 2). It is common practice to use either a 2.5mm or 3.25mm diameter electrode for the root run so the welder can manipulate the weld pool and control the degree of penetration. However, for the fill passes where penetration requirements are less critical, a 4mm or 5mm diameter electrode may be used to achieve higher deposition rates.
In MIG welding, the correct welding parameters for the material thickness, and a short arc length, should give adequate weld bead penetration. Too low a current level for the size of root face will give inadequate weld penetration. Too high a level, causing the welder to move too quickly, will result in the weld pool bridging the root without achieving adequate penetration.
It is also essential that the correct root face size and bevel angles are used and that the joint root gap is set accurately. To prevent the root gap from closing, adequate tacking will be required.
Best practice in prevention
The following techniques can be used to prevent lack of root fusion:
- In TIG welding, do not use too large a root face or too small a root gap and ensure the welding current is sufficient for the weld pool to penetrate fully the root
- In MMA welding, use the correct current level and not too large an electrode diameter for the root run
- In MIG / MAG welding, use a sufficiently high welding current level which is supported by the appropriate arc voltage for the application
- When using a joint configuration with a root gap, make sure it is of adequate width and does not close up during tacking and subsequent welding
- Do not use too low a current level causing the weld pool to bridge the root gap without fully penetrating the root.
Acceptance standards
The limits for lack of or incomplete penetration are specified in BS EN ISO 5817 for the three quality levels.
Lack of or incomplete root penetration is not permitted for Quality Level B (stringent) and Level C (intermediate). However, Level C makes an exception for partial penetration butt welds welded from both sideas.
For Quality Level D (moderate) short lack of or incomplete penetration imperfections are permitted.
Incomplete root penetration is not permitted in the manufacture of pressure vessels but is allowable in the manufacture of pipework depending on material and wall thickness.
Remedial actions
If the root cannot be directly inspected, for example using a penetrant or magnetic particle inspection technique, detection is by radiography or ultrasonic inspection. Remedial action will normally require removal by gouging or grinding to sound metal, followed by re-welding usually in conformity with the original welding procedure.
Relevant standards
BS EN ISO 5817:2007 Welding - fusion-welded joints in steel, nickel, titanium and their alloys (beam welding excluded) - Quality levels for imperfections.
BS EN ISO 10042:2005 Welding - Arc welded joints in aluminium and its alloys - Quality levels for imperfections.
Copies of other articles in the Job knowledge for welders series can be found under Practical Joining Knowledge or by using the search engine.
This Job Knowledge article was originally published in Connect, March/April 1999. It has been updated so the web page no longer reflects exactly the printed version.