Part 1
Part 2
Part 4
Part 5
Fillet welds may be combined with full or partial penetration butt welds - a combination weld. The designer is therefore required to decide whether to use a T-butt weld, a fillet weld or a combination of the two. In making this decision cost is a major factor.
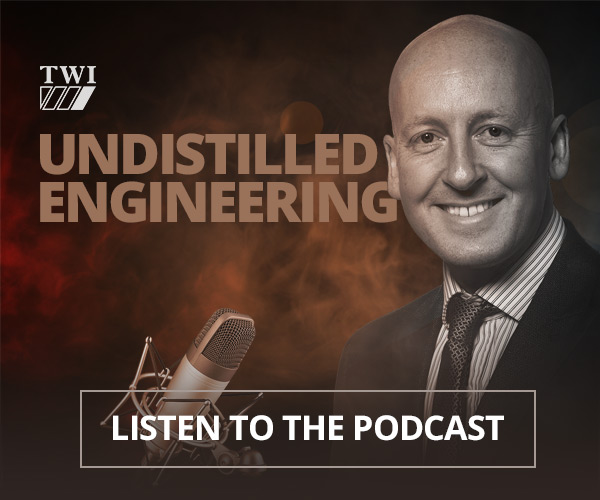
As mentioned in Job knowledge 91, the fillet weld requires no weld preparation, is easy to deposit and is often regarded as the cheapest weld of all to make. However cross sectional area, and therefore cost, increases as a function of the square of the leg length. Assuming the same strength requirements from the fillet welds as for the T-butt welds it becomes more economical to use a double sided full penetration T-butt joint at a plate thickness of around 30mm.The accuracy of this figure should be treated with caution as it is dependent on many factors such as the weld preparation costs and included angle.
Welding position is an additional factor. It may be more economical to deposit a butt weld in the flat position, where large diameter electrodes and high welding currents can be used, rather than a double sided fillet weld where one weld must be made in the overhead position ( Fig.1).
Fig.1. Flat position T-butt weld vs overhead fillet weld
An additional benefit from using a T-butt weld is that this weld type provides a direct transfer of force through the joint, giving a better performance under fatigue loads. Many design specifications will also have lower allowable stresses for a fillet weld compared with a butt weld and this can have a significant effect on cost, particularly when designing to match the strength of thicker plates.
It should be remembered that it is difficult, if not impossible, to examine a fillet weld volumetrically using radiographic or ultrasonic techniques and the internal weld quality is therefore entirely dependent on the skill and integrity of the welder. The comments on T-joints also apply to corner joints where two fillet welds may be more economical than one large fillet as shown in Fig.2. However, remember that one weld may need to be made in the overhead position if the component cannot be turned.
Fig.2. Corner Joints: Area of weld in a) -50mm2; and b) -25mm2
From the foregoing it is obvious that the decision to use fillet welds, T-butt joints or combination welds is not as straightforward as it may first appear and there are numerous factors that must be taken into account.
Butt joints are those welds where the weld metal is contained within the planes of the surfaces of the items being joined. The weld throat may be the full section thickness, a full penetration joint, or a proportion only - a partial penetration joint. Welds may be 'single sided joints', welded all from one side, or 'double sided', welded from both sides, ( Fig.3).
Fig.3. Full and partial penetration welds
Except for very thin plate, arc welded butt joints require a weld preparation to be flame cut or machined along the joint line. The conventional arc welding processes can penetrate into the base metal by only a limited amount. The maximum penetration in conventional TIG or manual metal arc (SMAW) welds is in the region of 3mm, MAG (GMAW) welds around 6mm and submerged arc some 15mm.
In order to weld the full thickness of a plate and achieve the weld throat thickness required by design it is therefore necessary to cut away sufficient metal along the joint line so that the welding electrode has access to the root of the joint, enabling the root pass to be deposited and then the remainder filled to complete the joint. A weld preparation, the 'weld prep', is therefore formed along the joint line using flame cutting, plasma cutting or machining. Figure 4 identifies the key features of a 'single bevel' weld preparation and those of a 'single-V' joint.
The smaller the included angle, the less access this will give to the root and the greater is the risk of defects such as lack of side wall fusion. This reduced access may, however, be compensated for by an increase in the root gap.
The bevel angles and the root gap will depend upon the process(es) used to make the joint and the material thickness. A narrow included angle requires less weld metal and therefore is more economical as the thickness increases. A downside to this is that the narrower the angle the more difficult access becomes and the risk of welding defects as mentioned above.
Too wide a root gap will result in a loss of control of the weld pool and melt through giving an irregular and excessive penetration bead. This may be overcome by using a backing strip if this is permitted by the service conditions.
Fig.4. Single bevel weld preparation
The choice of the weld preparation is therefore a compromise between maintaining adequate access and minimising the weld volume.
If a high quality root bead is required and access is not available to the root side of the weld e.g. in a pipe carrying fluids or in high pressure service, then an acceptable condition can be achieved using the TIG process to make the root bead. A typical pipe butt weld set-up would be 60° included angle, 1mm to 2mm root gap and a zero to 1.5mm thick root face.
Where access to the reverse side of the joint is available, the condition of the penetration bead is less important as the root bead can be ground to sound metal and a sealing pass deposited.
A reduction in weld volume can be achieved by the use of a 'J' preparation as shown in Fig.5. This preparation, unlike the straight chamfer of the 'V' preparation which can be flame cut, must be machined.
Fig.5. Key features of single sided 'J' preparation
This can be an expensive operation, which is why this type of weld is used only on thick joints, where the saving in deposited weld metal outweighs the cost of machining, or where very high quality root beads are required.
Machining of the weld preparation dictates that the dimensions, particularly that of the root face thickness, can be controlled far more closely than is possible with flame cutting and therefore a more accurate fit-up can be achieved.
It is often used on orbitally TIG welded pipe butt joints where a machined joint enables the tolerances required by a fully automatic process to be achieved.