Lamellar tearing can occur beneath the weld especially in rolled steel plate which has poor through-thickness ductility. The characteristic features, principal causes and best practice in minimising the risk of lamellar tearing are described.
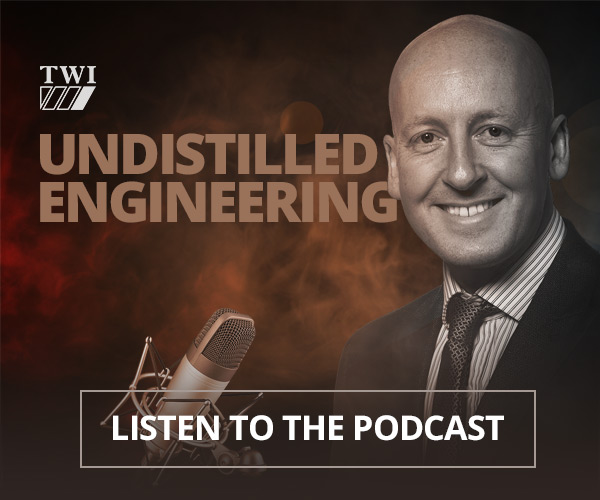
Identification
Visual appearance
The principal distinguishing feature of lamellar tearing is that it occurs in T-butt and fillet welds normally observed in the parent metal parallel to the weld fusion boundary and the plate surface , (Fig 1). The cracks can appear at the toe or root of the weld but are always associated with points of high stress concentration.
Fracture face
The surface of the fracture is fibrous and 'woody' with long parallel sections which are indicative of low parent metal ductility in the through-thickness direction, (Fig 2).
Metallography
As lamellar tearing is associated with a high concentration of elongated inclusions oriented parallel to the surface of the plate, tearing will be transgranular with a stepped appearance.
Causes
It is generally recognised that there are three conditions which must be satisfied for lamellar tearing to occur:
- Transverse strain - the shrinkage strains on welding must act in the short direction of the plate ie through the plate thickness
- Weld orientation - the fusion boundary will be roughly parallel to the plane of the inclusions
- Material susceptibility - the plate must have poor ductility in the through-thickness direction
Thus, the risk of lamellar tearing will be greater if the stresses generated on welding act in the through-thickness direction. The risk will also increase the higher the level of weld metal hydrogen
Factors to be considered to reduce the risk of tearing
The choice of material, joint design, welding process, consumables, preheating and buttering can all help reduce the risk of tearing.
Material
Tearing is only encountered in rolled steel plate and not forgings and castings. There is no one grade of steel that is more prone to lamellar tearing but steels with a low Short Transverse Reduction in Area (STRA), commonly associated with a high concentration of rolled sulphide or oxide inclusions, will be susceptible. As a general rule, steels with STRA over 20% are essentially resistant to tearing whereas steels with below 10 to 15% STRA should only be used in lightly restrained joints (Fig. 3).
Steels with a higher strength have a greater risk especially when the thickness is greater than 25mm. Aluminium treated steels with low sulphur contents (<0.005%) will have a low risk.
Steel suppliers can provide plate which has been through-thickness tested with a guaranteed STRA value of over 20%.
Joint Design
Lamellar tearing occurs in joints producing high through-thickness strain, eg T joints or corner joints. In T or cruciform joints, full penetration butt welds will be particularly susceptible. The cruciform structures in which the susceptible plate cannot bend during welding will also greatly increase the risk of tearing.
In butt joints, as the stresses on welding do not act through the thickness of the plate, there is little risk of lamellar tearing.
As angular distortion can increase the strain in the weld root and or toe, tearing may also occur in thick section joints where the bending restraint is high.
Several examples of good practice in the design of welded joints are illustrated in Fig. 4.
- As tearing is more likely to occur in full penetration T butt joints, if possible, use two fillet welds, Fig. 4a.
- Double-sided welds are less susceptible than large single-sided welds and balanced welding to reduce the stresses will further reduce the risk of tearing especially in the root, Fig. 4b
- Large single-side fillet welds should be replaced with smaller double-sided fillet welds, Fig. 4c
- Redesigning the joint configuration so that the fusion boundary is more normal to the susceptible plate surface will be particularly effective in reducing the risk, Fig. 4d
Weld size
Lamellar tearing is more likely to occur in large welds typically when the leg length in fillet and T butt joints is greater than 20mm. As restraint will contribute to the problem, thinner section plate which is less susceptible to tearing, may still be at risk in high restraint situations.
Welding process
As the material and joint design are the primary causes of tearing, the choice of welding process has only a relatively small influence on the risk. However, higher heat input processes which generate lower stresses through the larger HAZ and deeper weld penetration can be beneficial.
As weld metal hydrogen will increase the risk of tearing, a low hydrogen process should be used when welding susceptible steels.
Consumable
Where possible, the choice of a lower strength consumable can often reduce the risk by accommodating more of the strain in the weld metal. A smaller diameter electrode which can be used to produce a smaller leg length, has been used to prevent tearing.
A low hydrogen consumable will reduce the risk by reducing the level of weld metal diffusible hydrogen. The consumables must be dried in accordance with the manufacturer's recommendations.
Preheating
Preheating will have a beneficial effect in reducing the level of weld metal diffusible hydrogen. However, it should be noted that in a restrained joint, excessive preheating could have a detrimental effect by increasing the level of restraint produced by the contraction across the weld on cooling.
Preheating should, therefore, be used to reduce the hydrogen level but it should be applied so that it will not increase the amount of contraction across the weld.
Buttering
Buttering the surface of the susceptible plate with a low strength weld metal has been widely employed. As shown for the example of a T butt weld (Fig. 5) the surface of the plate may be grooved so that the buttered layer will extend 15 to 25mm beyond each weld toe and be about 5 to 10mm thick.
In-situ buttering ie where the low strength weld metal is deposited first on the susceptible plate before filling the joint, has also been successfully applied. However, before adopting either buttering technique, design calculations should be carried out to ensure that the overall weld strength will be acceptable.
Acceptance standards
As lamellar tears are linear imperfections which have sharp edges, they are not permitted for welds meeting the quality levels B, C and D in accordance with the requirements of BS EN ISO 5817:2007.
Detection and remedial action
If surface-breaking, lamellar tears can be readily detected using visual examination, liquid penetrant or magnetic particle testing techniques. Internal cracks require ultrasonic examination techniques but there may be problems in distinguishing lamellar tears from inclusion bands. The orientation of the tears normally makes them almost impossible to detect by radiography.
This Job Knowledge article was originally published in Connect, May/June 2000. It has been updated so the web page no longer reflects exactly the printed version.