The characteristic features and principal causes of porosity imperfections are described. Best practice guidelines are given so welders can minimise porosity risk during fabrication.
Identification
Porosity is the presence of cavities in the weld metal caused by the freezing in of gas released from the weld pool as it solidifies. The porosity can take several forms:
- distributed
- surface breaking pores
- wormhole
- crater pipes
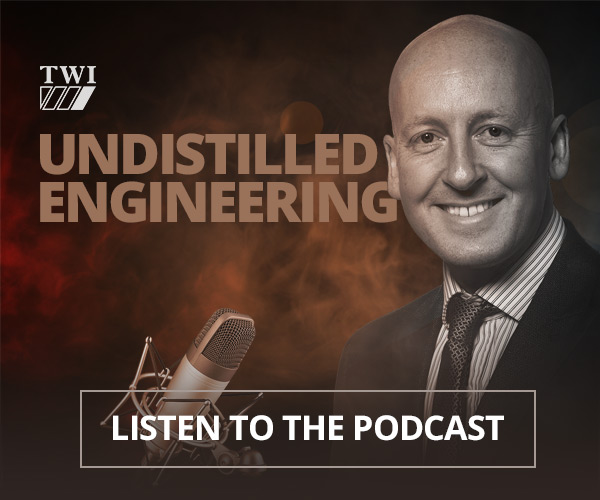
Cause and prevention of defects in welding
Distributed porosity and surface pores
Distributed porosity
(Fig. 1) is normally found as fine pores throughout the weld bead. Surface breaking pores
(Fig. 2) usually indicate a large amount of distributed porosity
Cause
Porosity is caused by the absorption of nitrogen, oxygen and hydrogen in the molten weld pool which is then released on solidification to become trapped in the weld metal.
Nitrogen and oxygen absorption in the weld pool usually originates from poor gas shielding.
As little as 1% air entrainment in the shielding gas will cause distributed porosity and greater than 1.5% results in gross surface breaking pores. Leaks in the gas line, too high a gas flow rate, draughts and excessive turbulence in the weld pool are frequent causes of porosity.
Hydrogen can originate from a number of sources including moisture from inadequately dried electrodes, fluxes or the workpiece surface. Grease and oil on the surface of the workpiece or filler wire are also common sources of hydrogen.
Surface coatings like primer paints and surface treatments such as zinc coatings, may generate copious amounts of fume during welding. The risk of trapping the evolved gas will be greater in T joints than butt joints especially when fillet welding on both sides (see Fig 2). Special mention should be made of the so-called weldable (low zinc) primers. It should not be necessary to remove the primers but if the primer thickness exceeds the manufacturer's recommendation, porosity is likely to result especially when using welding processes other than MMA.
Prevention
The gas source should be identified and removed as follows:
Air entrainment- - seal any air leak
- - avoid weld pool turbulence
- - use filler with adequate level of deoxidants
- - reduce excessively high gas flow
- - avoid draughts
Hydrogen- - dry the electrode and flux
- - clean and degrease the workpiece surface
Surface coatings- - clean the joint edges immediately before welding
-
- check that the weldable primer is below the recommended maximum thickness
Wormholes
Characteristically, wormholes are elongated pores (Fig. 3) which produce a herring bone appearance on the radiograph.
Cause
Wormholes are indicative of a large amount of gas being formed which is then trapped in the solidifying weld metal. Excessive gas will be formed from gross surface contamination or very thick paint or primer coatings. Entrapment is more likely in crevices such as the gap beneath the vertical member of a horizontal-vertical, T joint which is fillet welded on both sides.
When welding T joints in primed plates it is essential that the coating thickness on the edge of the vertical member is not above the manufacturer's recommended maximum, typically 20µm, through over-spraying.
Prevention
Eliminating the gas and cavities prevents wormholes.
Gas generation- - clean the workpiece surfaces at and adjacent to the location where the weld will be made
- - remove any surface contamination, in particular oil, grease, rust and residue from NDT operations
- - remove any surface coatings from the joint area to expose bright material
-
- check the primer thickness is below the manufacturer's maximum
Joint geometry- - avoid a joint geometry which creates a cavity
-
Crater pipe
A crater pipe forms during the final solidification of the weld pool and is often associated with some gas porosity.
Cause
This imperfection results from shrinkage on weld pool solidification. Consequently, conditions which exaggerate the liquid to solid volume change will promote its formation. Extinquishing the welding arc will result in the rapid solidification of the weld pool.
In TIG welding, autogenous techniques, or stopping the welding wire entering the weld pool before extinquishing the welding arc, will effect crater formation and may promote the pipe imperfection.
Prevention
Crater pipe imperfection can be prevented by controlling the rate at which the welding arc is extinquished or by welder technique manipulating the welding arc and welding wire
Removal of stop- - use run-off tag to enable the welding arc to be extinquisehd outside the welded joint
-
- grind out the weld run stop crater before continuing with the next electrode or depositing the subsequent weld run
Welder technique- - progressively reduce the welding current to reduce the weld pool size (use slope-down or crater fill functions)
-
- add filler (TIG) to compensate for the weld pool shrinkage
Porosity susceptibility of materials
Gases likely to cause porosity in the commonly used range of materials are listed in the Table.
Principal gases causing porosity and recommended cleaning methods
Material | Gas | Cleaning |
C-Mn steel |
Hydrogen, Nitrogen and Oxygen |
Grind to remove scale coatings |
Stainless steel |
Hydrogen |
Degrease + wire brush + degrease |
Aluminium and alloys |
Hydrogen |
Chemical clean + wire brush + degrease + scrape |
Copper and alloys |
Hydrogen, Nitrogen |
Degrease + wire brush + degrease |
Nickel and alloys |
Nitrogen |
Degrease + wire brush + degrease |
Detection and remedial action
If the imperfections are surface breaking, they can be detected using a penetrant or magnetic particle inspection technique. For sub surface imperfections, detection is by radiography or ultrasonic inspection. Radiography is normally more effective in detecting and characterising porosity imperfections. However, detection of small pores is difficult especially in thick sections.
Remedial action normally needs removal by localised gouging or grinding but if the porosity is widespread, the entire weld should be removed. The joint should be re-prepared and re-welded as specified in the agreed welding procedure.
This Job Knowledge article was originally published in Connect, July/August 1999. It has been updated so the web page no longer reflects exactly the printed version.