Coined from the words Light Amplification by Stimulated Emission of Radiation lasers have been a byword for efficiency and quality in materials processing since their advent in the sixties.
They offered an entirely new form of energy which in turn lent itself to uses in manufacturing, medicine and communications. Able to heat, melt and even vaporise material, lasers are seen as the ideal medium for channelling intense but controllable energy.
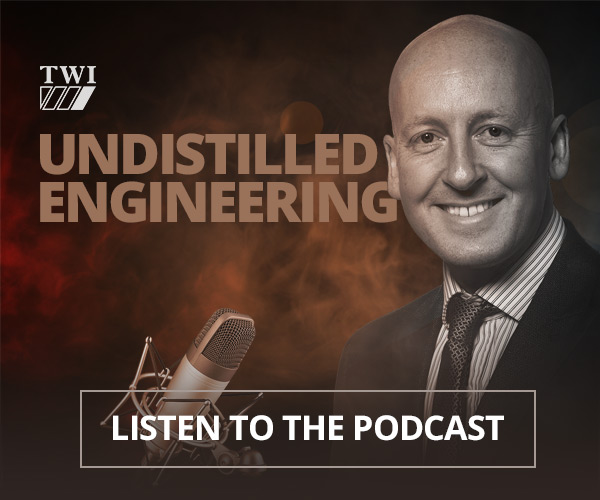
By far the most popular use of lasers is for cutting.
Laser Cutting
Laser cutting is mainly a thermal process in which a focused laser beam is used to melt material in a localised area. A co-axial gas jet is used to eject the molten material and create a kerf. A continuous cut is produced by moving the laser beam or workpiece under CNC control. There are three major varieties of laser cutting: fusion cutting, flame cutting and remote cutting.
In fusion cutting, an inert gas (typically nitrogen) is used to expel molten material out of the kerf. Nitrogen gas does not exothermically react with the molten material and thus does not contribute to the energy input.
In flame cutting, oxygen is used as the assist gas. In addition to exerting mechanical force on the molten material, this creates an exothermic reaction which increases the energy input to the process.
In remote cutting, the material is partially evaporated (ablated) by a high-intensity laser beam, allowing thin sheets to be cut with no assist gas.
The laser cutting process lends itself to automation with offline CAD/CAM systems controlling either three-axis flatbed systems or six-axis robots for three-dimensional laser cutting.
Improvements in accuracy, edge squareness and heat input control means that the laser process is increasingly replacing other profiling cutting techniques, such as plasma and oxy-fuel. There are many state of the art laser machines on the market for cutting purposes, which can be used to cut metals, woods and engineered woods.
Cutting characteristics | Benefits |
- Cuts carbon manganese steels up to 20mm
- Cuts stainless steel up to 12mm
- Cuts aluminium up to 10mm
- Cuts brass and titanium
- Cuts thermoplastics, wood and many non-metals
|
- High quality cut – no finishing
- Ultra flexible – simple or complex parts
- Non contact – no surface blemishing
- Quick set up – small batches
- Low heat input – small HAZ, low distortion
- Lends itself to nearly all materials
|
How Does the Lens Used Affect the Thickness of the Cut?
The laser cutting process involves focusing a laser beam, usually with a lens (sometimes with a concave mirror), to a small spot which has sufficient power density to produce a laser cut.
The lens is defined by its focal length, which is the distance from the lens to the focused spot. The critical factors which govern the efficiency of the process are the focused spot diameter (d) and the depth of focus (L).
The depth of focus is the effective distance over which satisfactory cutting can be achieved. It can be defined as the distance over which the area of the focused spot does not increase beyond 50%.
The laser focal spot diameter and the depth of focus is dependent on the raw laser beam diameter on the lens and the focal length of the lens. For a constant raw laser beam diameter, decrease in the focal length lens of the focusing lens results in a smaller focal spot diameter and depth of focus. For a constant focus length lens, increase in the raw beam diameter also reduces both the spot diameter and the depth of focus.
To allow comparison between lasers with different beam diameters we therefore use a factor called the focus f-number, which is the focal length, F, divided by the incoming raw beam diameter, D.
The requirements for cutting are as follows:
a) high power density and therefore small focused spot size
b) long depth of focus to process thicker materials with a reasonable tolerance to focus position variation.
Because these two requirements are in conflict with each other, a compromise must be made. The only other consideration is that the shorter the focal length, the closer the lens is to the workpiece, and therefore more likely to get damaged by spatter from the cutting process.
In fact, it would be possible to optimise focal length for each material thickness, but this would involve additional set-up time when changing from one job to another, which would have to be balanced against the increased speed. In reality, changing the lens is avoided and a compromised cutting speed used, unless a specific job has special requirements.
What Types of Laser Cutting are Used for Sheet Metal?
Nowadays most of industrial sheet metal laser cutting is carried out using two types of lasers: CO2 and fibre.
CO2 Laser
The CO2 laser (carbon dioxide laser) is generated in a gas mixture, which mostly consists of carbon dioxide (CO2), helium and nitrogen. Such a laser is electrically pumped using an electric discharge.
CO2 lasers typically emit at a wavelength of 10.6μm. Those used for material processing can generate beams of many kilowatts in power. The wall-plug efficiency of CO2 lasers is about 10%, which is higher than for most lamp-pumped solid-state lasers (eg ND:YAG lasers), but lower than for many diode-pumped lasers .
A CO2 laser can cut thicker materials (>5mm) faster than a fibre laser of the same power. It also produces a smoother surface finish when cutting thicker materials.
Laser cutting of sheet metals historically started with CO2 lasers. Most CO2 laser cutting machines are three-axis systems (X-Y, two-dimensional positioning control with a Z-axis height control).
There are, however, a number of ways of achieving the X-Y movement: either moving the laser head, moving the workpiece or a combination of both.
The most popular approach is known as a 'flying optics' system, where the workpiece remains stationary and mirrors are moved in both X and Y axes. The advantages of this approach are that the motors are always moving a known, fixed mass. This can often be much heavier than the workpiece, but it is easier to predict and control.
As the workpiece is not moved, this also means that there is no real limit to sheet weight. The disadvantage of flying optics is the variation in beam size, as a laser beam is never perfectly parallel, but actually diverges slightly as it leaves the laser.
This means that without controlling the divergence, there may be some variation in cutting performance between different parts of the table, due to a change in raw beam size. This effect can be reduced by adding a re-collimating optic, or some systems even use adaptive mirror control.
The alternative is a 'fixed optic' system where the laser head remains stationary and the workpiece is moved in both X and Y axes. This is the ideal situation optically, but the worse situation mechanically, especially for heavier sheets.
For relatively light sheet weights, a fixed optic system can be a viable option, but as the sheet weight increases, accurately positioning the material at high speed can be a problem.
The third option is known as a 'hybrid' system, where the laser head is moved in one axis and the material moved in the other axis. This is often an improvement over fixed optics, but still suffers from difficulties with heavier sheet weights.
Fibre Lasers
Fibre lasers are a member of a family called ‘solid-state lasers’. In solid-state lasers, the beam is generated by a solid medium. Fibre lasers, disk lasers and Nd:YAG lasers are in the same category.
A fibre laser beam is generated by a series of laser diodes. The laser beam is then transmitted through an optical fibre where it gets amplified (similar to a conventional laser cavity in CO2 lasers). The amplified beam, on exiting the optical fibre, is collimated and then focused by a lens or a concave onto the material to be cut. Fibre laser sources have the following advantages:
- Unlike a conventional CO2 resonator, a fibre laser source does not have any moving parts (eg fans for gas circulation) or mirrors in the light-generating source. This is a major advantage in terms of reducing maintenance requirements and operating costs.
- Fibre lasers are typically two to three times more energy-efficient that CO2 lasers of the same power.
- A fibre laser can cut thin sheets faster than a CO2 laser of the same power. This is due to better absorption of fibre laser wavelength at the cutting front.
- Fibre lasers are capable of cutting reflective materials without fear of back reflections damaging the machine. This allows copper, brass, and aluminium to be cut without problems.
Direct Diode Lasers
Direct diode laser technology is the latest progress in the field of solid-state lasers. In this technology, several laser beams emitted from laser-emitting diodes of different wavelengths are superimposed using so-called beam combining techniques. Unlike fibre lasers, direct diode lasers do not include a brightness-enhancing stage, giving them lower optical losses and higher wall-plug efficiency. However, for the same reason, direct diode lasers are currently of lower beam quality compared to fibre lasers. Direct diode lasers at multi-kilowatt levels of power are commercially available and have been successfully used for sheet metal cutting applications.
What Difficulties Does Reflection Cause?
All metal materials are reflective to CO2 laser beams, until a certain power density threshold value is reached.
Aluminium is more reflective than carbon manganese steel or stainless steel and has the potential to cause damage to the laser itself.
Most laser cutting machines use a laser beam aligned normal to a flat sheet of material. This means that should the laser beam be reflected by the flat sheet it can be transmitted back through the beam delivery optics and into the laser itself, potentially causing significant damage.
This reflection does not come entirely from the sheet surface, but is caused by the formation of a molten pool which can be highly reflective. For this reason simply spraying the sheet surface with a non-reflective coating will not entirely eliminate the problem.
As a general rule the addition of alloying elements reduces the reflectivity of aluminium to the laser, so pure aluminium is harder to process than a more traditional 5000 series alloy.
With good, consistent cutting parameters the likelihood of a reflection can be reduced to almost zero, depending on the materials used. However, it is still necessary to be able to prevent damage to the laser while developing the conditions or if something goes wrong with the equipment.
The 'aluminium cutting system' which most modern equipment uses is actually a way of protecting the laser rather than an innovative technique for cutting. This system usually takes the form of a back reflection system that can detect if too much laser radiation is being reflected back through the optics.
This will often automatically stop the laser, before any major damage is caused. Without this system there are risks with processing aluminium as there is no way of detecting if potentially hazardous reflections are occurring.