The amount of heat depends on the thermal conductivity and electrical resistance of the metal as well as the amount of time the current is applied. This heat can be expressed by the equation:
Q = I2Rt
In this equation “Q” is heat energy, “I” is current, “R” is electrical resistance and “t” is the time for which the current is applied.
Materials Appropriate for Spot Welding
Due to its lower thermal conductivity and higher electrical resistance, steel is comparatively easy to spot weld, with low carbon steel being most suited to spot welding. However, high carbon content steels (Carbon equivalence > 0.4wt%) are prone to poor fracture toughness or cracking in the welds as they tend to form hard and brittle microstructures.
Galvanised steel (zinc coated) requires slightly higher welding currents to weld than uncoated steels. Also, with zinc alloys, the copper electrodes rapidly degrade the surface and lead to a loss of weld quality. When spot welding zinc coated steels, electrodes must either be frequently exchanged or the electrode tip surface should be ‘dressed’, where a cutter removes contaminated material to expose a clean copper surface and reshapes the electrode.
Other materials commonly spot welded include stainless steels (in particular austenitic and ferritic grades), nickel alloys and titanium.
Although aluminium has a thermal conductivity and electrical resistance close to that of copper, the melting point for aluminium is lower, which means welding is possible. However, due to its low resistance, very high levels of current need to be used when welding aluminium (in the order of two to three times higher than for steel of equivalent thickness).
In addition, aluminium degrades the surface of copper electrodes within a very small number of welds, meaning that stable high quality welding is very hard to achieve. For this reason, only specialist applications of aluminium spot welding are currently found in industry. Various new technology developments are emerging to help enable stable high quality spot welding in aluminium.
Copper and its alloys can also be joined by resistance spot welding, although spot welding copper cannot be easily achieved with conventional copper alloy spot welding electrodes, as heat generation in the electrodes and work piece are very similar.
The solution to welding copper is to use an electrode made of an alloy with a high electrical resistance and a melting temperature far in excess of the melting point of copper (much greater than 1080°C). Electrode materials typically used for spot welding copper include molybdenum and tungsten.
Where is Spot Welding Used?
Spot welding has applications in a number of industries, including automotive, aerospace, rail, white goods, metal furniture, electronics, medical building and construction.
Given the ease with which spot welding can be automated when combined with robots and manipulation systems, it is the most common joining process in high volume manufacturing lines and has in particular been the main joining process in the construction of steel cars for over 100 years.
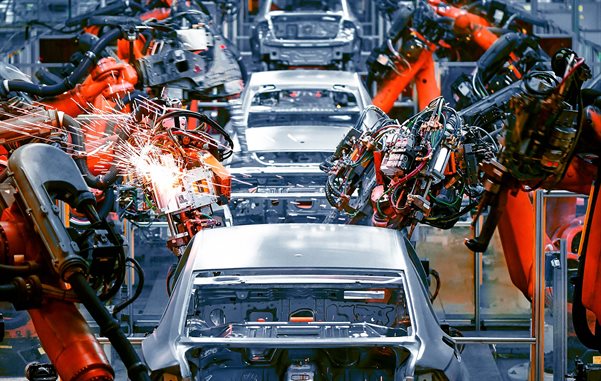
Car body welding on an automotive production line.
Related FAQs