Pop rivets, also known as blind rivets, are a type of rivet. They are used in applications where there is limited - or no - access to the rear side (blind side) of the parts to be joined.
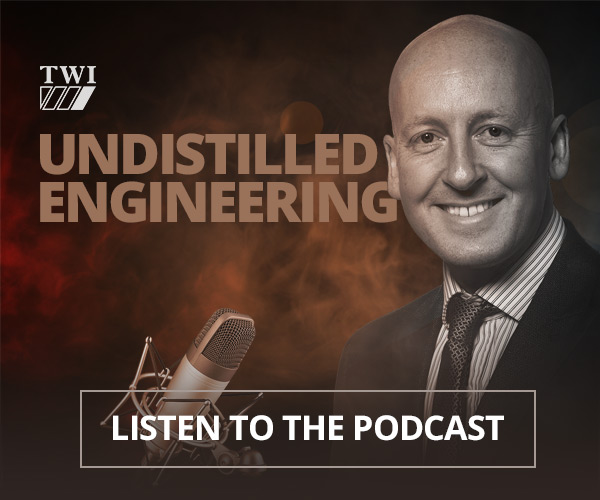
Pop rivets consist of two parts. The first part is called the rivet body (also known as the shell or hat) and the second part is called the mandrel (also known as the stem).
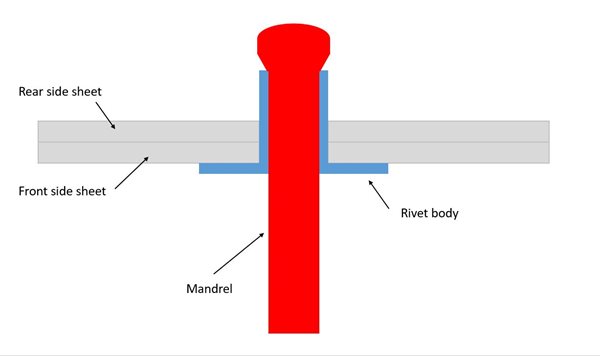
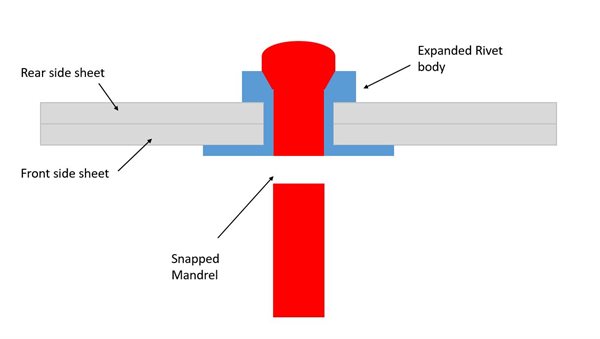
In situations where access to both sides of a component is limited, a hole is first drilled through the parts to be joined. A pop rivet is then inserted through the drilled hole and the rivet body is brought into contact with the parts. A pop rivet gun is placed on the rivet, pulling the mandrel into the rivet body, causing it to expand and grip the parts to be joined. Once gripped, the mandrel snaps, permanently holding the rivet in place. This results in a localised joint.
They are used to make high strength joints in a range of materials, including metals, plastics, wood and leather. Typically, the processes is used for joining plastic or sheet metal.
To enable pop rivets to meet the requirements of a wide variety of applications, they are available in many materials, including:
- Steel
- Stainless steel
- Monel
- Copper
- Aluminium
Advantages include:
- Being cost effective
- Allowing for joining of parts when there is limited rear access
- Being durable
- Being lighter than bolts/screws (dependent on rivet material)
Disadvantages include:
- Being difficult to remove once placed
- Protruding from the sheet metal surface, potentially creating a hazard and reducing aerodynamics
- Potential corrosion issues if the rivet material differs from the metal parts to be joined