MIG welding power sources have what is known as a 'constant voltage' output characteristic (Fig. 1). The arc voltage is established by setting the output voltage on the power supply. The power source will then supply sufficient welding current to melt the welding electrode at the rate required to maintain the preset voltage (or relative arc length). This means that the wire feed speed can be used to control the welding current.
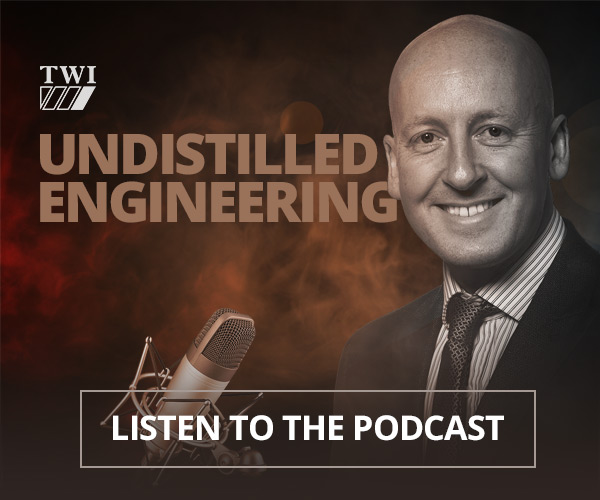
As the wire feed speed is increased, the arc length will momentarily become shorter so the arc voltage becomes lower than the preset value. Because of its output characteristic, the power source will supply a higher welding current. This increases the melting rate of the electrode which self corrects the arc voltage and arc length.
The contact tip-to-workpiece distance affects the welding current too. Increasing the contact tip-to-workpiece distance produces a longer electrode stickout, or electrode extension. As the electrode extension increases, so does the electrical resistance of the wire. Resistance heating causes the temperature of the electrode to rise. Therefore, less welding current is required to melt the electrode at a given feed rate.
A long electrical stickout increases deposition rate because the wire is preheated before melting in the arc. However, too long a stickout results in poor weld bead shape, shallow penetration and an unstable arc. Good electrode extension is from 6 to 13mm for short circuiting transfer and from 13 to 25mm for other types of metal transfer.
For more information, please contact us.