Frequently Asked Questions
Preheat is the temperature to which the surfaces to be welded together are heated, before welding commences. Interpass temperature is the temperature at which subsequent weld runs are deposited. Procedures can specify a maximum interpass temperature, which is done to control weld metal microstructural development, and also ensures that the weld is similar to the welds made in the procedure qualification. Minimum interpass temperatures are maintained to control hydrogen cracking, and in most cases are similar to the preheat temperature.
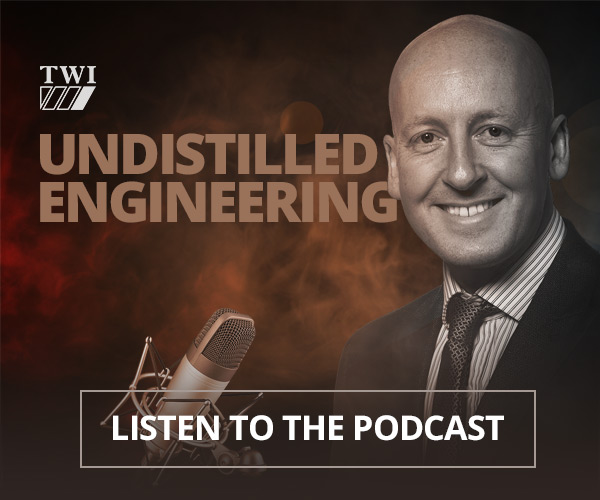
All the weld runs in a joint will have the same hydrogen input, cooling capacity and composition, and therefore similar preheat (minimum interpass) requirements, dependent on heat input, to avoid hydrogen cracking . A possible exception to this would be the root pass, which may have a higher stress concentration than the remainder of the joint, and so the root region may require a higher preheat than the minimum interpass temperature of the filling passes.
Some materials need the interpass temperature to be maintained for a period of time to encourage hydrogen escape from the material between passes. In these cases, the minimum interpass temperature is the minimum temperature reached between passes, rather than the minimum temperature at which any run is deposited. As increasing numbers of passes are deposited, the hydrogen in the weld has further to diffuse before reaching a free surface, so hydrogen is more likely to become trapped in the steel and to be the cause of cracking upon final cooling. Thus, maintaining interpass temperature for a longer period of time may reduce the need for postheat after welding, as the hydrogen is encouraged to difffuse out of the weld during the welding operation.
For high alloy materials, it can be important to allow the weld to cool to below the transformation temperature between passes, as too high an interpass temperature will allow the weld to remain austenitic. Hydrogen has a higher solubility in austenite than ferrite, and also a slower diffusion rate, so if the weld is austenitic throughout welding, less hydrogen will escape from the steel and cracking may occur upon final transformation. The transformation from austenite to ferrite between passes also allows microstructural refinement or tempering, from heating by subsequent passes.
It is necessary to select a method of preheat control which is appropriate to the welding operation. For example, when there is a need for stringent interpass control, certain preheating methods, such as local preheating ahead of the moving welding torch, which can allow the interpass temperature to fall below the minimum interpass temperature, are not suitable.
See further information about Materials and Corrosion Management or please contact us.