Temper embrittlement refers to the decrease in notch toughness of alloy steels when heated in, or cooled slowly through, a temperature range of 400°C to 600°C. Temper embrittlement can also occur as a result of isothermal exposure to this temperature range. The occurrence of temper embrittlement can be determined by measurement of the change in the ductile to brittle transition temperature with a notched bar impact test, before and after heat treatment. In most cases, the hardness and tensile properties of the material will not show any change as a result of embrittlement, but the transition temperature can be raised by as much as 100°C for embrittling heat treatments.
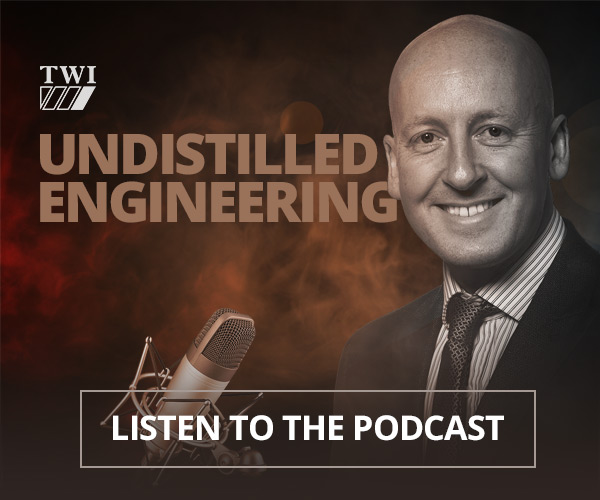
Temper embrittlement is caused by the presence of specific impurities in the steel, which segregate to prior austenite grain boundaries during heat treatment. The main embrittling elements (in order of importance) are antimony, phosphorus, tin and arsenic. The fracture surface of a material embrittled by these elements has an intergranular appearance.
Plain carbon steels with less than 0.5% Mn are not susceptible to temper embrittlement. However, additions of Ni, Cr and Mn will cause greater susceptibility to temper embrittlement. Small additions of W and Mo can inhibit temper embrittlement, but this inhibition is reduced with greater additions.
The original toughness of a steel which has suffered temper embrittlement can be restored by heating to above 600°C, and then cooling rapidly to below 300°C. However, the best method of avoidance is to reduce the embrittling impurities through control of raw materials and steel production.
In order to assess susceptibility to temper embrittlement in Cr-Mo steels, two compositional parameters are commonly employed, the Watanabe J factor (1) and the Bruscato X factor (2).
J=(Mn + Si)(P + Sn) x104 (in wt %), has been applied to parent steels and weld metals.
X=(10P + 5Sb + 4Sn + As)/100 (in ppm), is applied to weld metals.
If J is less than or equal to 180, or if X is less than 20, the risk of temper embrittlement is considered to be low. A limit in this form can be specified for procurement, where concerns over temper embrittlement exist. A more general expression for embrittlement in weld metals was given by Sugiyama et al(3):
P E = C + Mn + Mo + Cr/3 + Si/4 + 3.5 (10P + 5Sb + 4Sn + As)
The maximum value for this expression to avoid serious embrittlement depends on the welding process but is given as 2.8-3.0 where coarse grained weld metal exists.
Step cooling can reveal the susceptibility of a steel to temper embrittlement. The Charpy impact energy and transition temperature for steel after an embrittling heat treatment involving step cooling have been related via a mathematical expression that when fulfilled ensures that the material will not suffer an unacceptable degree of temper embrittlement in service (4).
AF + 2.5(SC - AF) < 38°C
where
AF=As formed Charpy 54J temperature
SC=Step cooled Charpy 54J temperature
This expression is used in the construction of pressure vessels that may operate in the embrittling temperature range, or that may pass slowly through that temperature range upon startup or shutdown.
One step cooling method with hold times and temperatures is given in ASTM A387, supplementary requirements [5] although this gives a more stringent requirement for the acceptable degree of temper embrittlement.
Temper embrittlement has been also related to reheat cracking and low-ductility creep fractures, and a number of types and mechanisms have been proposed, considering carbide precipitation as well as grain boundary embrittling elements.
References
- Ishiguo, T; Murakami, Y; Ohnishi, K and Watanabe, J: "2.25%Cr-1%Mo pressure vessel steels with improved creep rupture strength"; Proceedings of the symposium on Applications of 2.25%Cr-1%Mo steel for thick-wall pressure vessels, ASTM STP 755, 1980, pp. 129-147.
- Bruscato, R. M: "Embrittlement factors for estimating temper embrittlement in 2.25Cr:1Mo, 3.5Ni-1.75Cr-0.5Mo-0.1V and 3.5Ni steels"; ASTM conference, Miami, Florida, 1987.
- Sugiyama, T; Hatori, N; Yamamoto, S; Yoshino, F and Kiuchi, A: "Temper embrittlement of Cr-Mo weld metals"; IIW Doc. XII-E-6-81, IIW, 1981.
- Erwin, W.E. and Kerr, J.G: "The use of Quenched and Tempered 2¼Cr-1Mo Steel for Thick Wall Reactor Vessels in Petroleum Refinery Processes: An Interpretive review of 25 Years of Research and Application"; WRC Bulletin 275, February 1982.
- ASTM A387:"Standard specification for pressure vessel plates, Alloy steel, Chromium-molybdenum"
See further information about Materials and Corrosion Management, or please contact us.