Friction surfacing is a technique for depositing many materials including tool steels, stainless steels and hardfacings to improve the performance of an underlying metallic surface.
The process involves rotating a solid consumable bar with one of its ends pressed hard against a substrate material such as a plate, disc or cylinder. Heat is generated at the tip of the consumable, producing a plasticised layer. Lateral movement of the substrate, relative to the rotating consumable, deposits this plasticised material on to the substrate (see illustration).
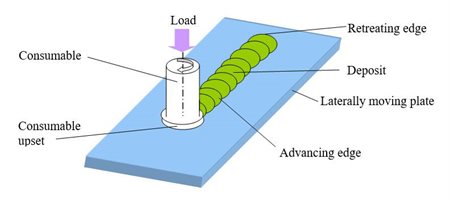
FIG. A. Schematic diagram of friction surfacing process on a flat substrate
There is no melting of the substrate material and therefore no dilution of the substrate into the deposit. The composition of the deposit is the same as that of the consumable.
The deposit is inherently homogenous and has good mechanical strength and adherence. The interface region usually remains intact, even after resisting loads equal to the ultimate tensile strength of the weaker material. However, the bond quality at the edges of the deposit is generally poor, and this area may need to be removed. With high strength surfacing materials, the thickness of the deposit is generally small. The surface appearance depends on the material deposited, and the parameters used.
Friction surfacing is a solid phase process, allowing use of metallurgically incompatible materials. Special combinations of material properties can be achieved which cannot usually be realised in monolithic materials. This reduces usage of more expensive or strategic materials.
The process has been extended to deposit metal matrix composites (MMCs) by inserting hard particles into one or more holes or slots machined in the consumable bar. The material of the bar becomes the matrix, with the hard particles distributed throughout it.
Friction surfacing is best suited to niche applications where materials compatibility problems exist.
Further information
TWI Industrial Members are welcome to read Friction surfacing tomorrow - industrial applications of cladding.