Chemical vapour deposition (CVD) is a coating process that uses thermally induced chemical reactions at the surface of a heated substrate, with reagents supplied in gaseous form. These reactions may involve the substrate material itself, but often do not.
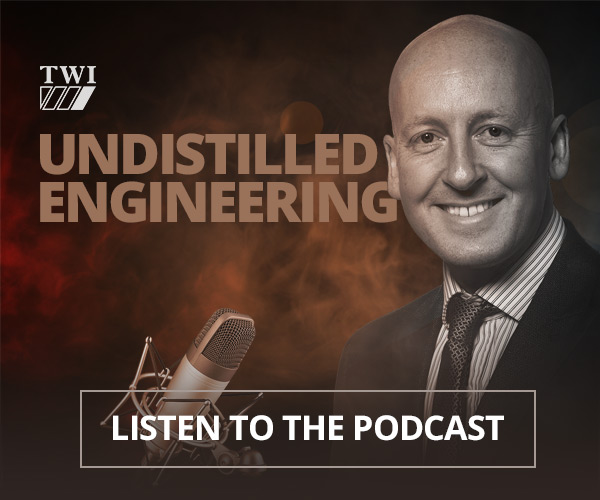
The simplest CVD process involves the pyrolytic decomposition of a gaseous compound on the substrate to provide a coating of a solid reaction product. For example, the following reactions are used to produce solid coatings of tungsten metal (W), titanium carbide (TiC) and titanium nitride (TiN) respectively:
WF6 + 3H2 = W (solid) + 6HF (gas)
TiCl4 + CH4 = TiC (solid) + 4HCl (gas)
TiCl4 + ½ N2 + 2H2 = TiN (solid) + 4HCl (gas)
Alumina may be deposited by the reaction:
Al2Cl6 + 3CO2+ 3H2 = Al2O3 (solid) + 3CO (gas) + 6HCl (gas)
Although, the reactions listed above involve only gaseous reagents, the substrate material in some cases also plays a significant role. For example, the rate controlling step in the growth of a TiC layer on carbon steels or cemented carbides from TiCl 4is the reaction:
TiCl4 + C + 2H2 = TiC (solid) + 4HCl (gas)
This involves carbon from the substrate. This reaction can lead to decarburisation of the substrate immediately beneath the coating and must be taken into account when selecting a suitable substrate material.
A key advantage of the CVD process lies in the fact that the reactants used are gases, thereby taking advantage of the many characteristics of gases. One result is that CVD is not a line-of-sight process as are most other plating/coating processes and can be used to coat restricted access surfaces. CVD offers many advantages over other deposition processes. These include a wide range of coating materials based on metals, alloys and ceramics. The coatings can be deposited with very low porosity levels and with high purity. The process can be economical in production, with many parts coated at the same time in large batch numbers.
CVD coating processes employ temperatures typically in the range 600 to 1100°C. At these high temperatures, significant thermal effects may occur in the substrate material. Steels, for example, will often be heated into the austenite phase region and the coating process may need to be followed by suitable heat treatment to optimise the properties of the substrate.
A commonly variant of CVD widely used in industry is plasma assisted CVD (PACVD). In the plasma assisted (also known as plasma activated) CVD process, an electrical discharge in a low pressure (<100 Pa) gas is used to accelerate the kinetics of the CVD reaction. This can lower the reaction temperatures by several hundreds of degrees Celsius. However PACVD coating rates are generally lower than CVD as a consequence of the lower gas pressure.
Plasma assisted CVD method is one of several related techniques used to deposit thin films of diamond, which have attractive tribological properties with very high hardness and low friction. Microwave plasmas are currently of considerable interest for the activated manufacture of diamond films.
Other compounds that are deposited by PACVD include quartz, silicon, silicon nitride and titanium nitride as thin film substrates, dielectrics and insulating layers in electronic applications.
See further information about Materials & Corrosion Management or please contact us.