Burn-in is an accepted practice for detecting early failures in a population of semiconductor devices. It usually requires the electrical testing of a product, using an expected operating electrical cycle (extreme of operating condition), typically over a time period of 48-168 hours. Alternatively, thermal (e.g. 125°C for 168 hours) or environmental stress screening (e.g. 20 cycles from -10 to 70°C ramped at +°C/mm) is used. Burn-in is applied to products as they are made, to detect early failures caused by faults in manufacturing practice.
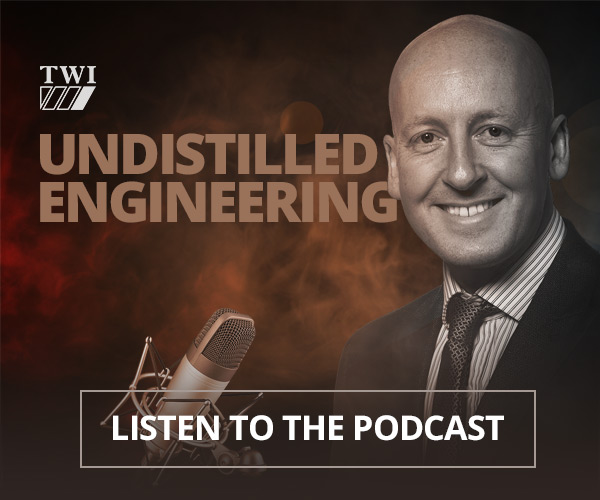
As a general rule, it is best to burn-in at the component level when the cost of testing and replacing parts is lowest. Burn-in of a board or an assembly is difficult because different components have different limits. However, burn-in at this level can show faults that burn-in of components cannot find, such as dry or cold solder joints and contact problems.
For more complex devices, dynamic burn-in is used where thermal stress is combined with dynamic simulation of inputs to provide worst-case operating conditions.
Further information
Please contact us for more information.