Tehnic
Ce materiale pot fi procesate folosind CoreFlow ™?
Plăcile din aluminiu AA6082-T6 și AA1050-H14 cu o grosime de la 5 la 50 mm au fost procesate cu succes și aplicația a trecut deja la demonstratoare plate și tubulare care prezintă canale de-a lungul traiectoriilor liniare, curbate și elicoidale. Demonstranții au trecut atât testul de scurgere, cât și testarea presiunii, cu rate de scurgere mult sub 10-8 mbar ∙ L / s și presiune de până la 9 bar.
Procesul a fost în prezent portat și testat pe alte aliaje de aluminiu și pe cupru, care prezintă proprietăți termice îmbunătățite față de aluminiu. În plus, magneziul și titanul sunt următorii candidați metalici pe care va fi testat procesul.
În afară de metale, se așteaptă ca CoreFlow ™ să funcționeze și pe termoplastice. Sudarea prin frecare prin amestecare (FSW) și sudarea prin frecare liniară (LFW) a materialelor plastice este deja o tehnologie dovedită și consacrată. Aplicarea CoreFlow ™ la termoplastice precum PEEK deschide o gamă largă de noi posibilități de a înlocui metalele și ceramica în unele aplicații. Utilizările includ radiatoarele de pe plăcile de circuite, precum și tuburile pentru schimbătoarele de căldură din aparate, iluminat, dispozitive de telecomunicații, mașini de afaceri și echipamente industriale utilizate în medii corozive. De mare interes este aplicarea CoreFlow ™ pe piese turnate.
Care este distorsiunea în comparație cu tehnicile convenționale de formare a canalelor?
CoreFlow ™ exploatează fricțiunea pentru a genera căldură și plastifia materialul din jurul sondei, prin urmare provoacă un anumit nivel de distorsiune. Temperaturile de vârf implicate sunt similare cu cele ale FSW, ajungând până la 90% din temperatura de topire a materialului. Cu toate acestea, în ceea ce privește FSW, profilul de căldură CoreFlow ™ este mai localizat. Ca atare, nivelurile de distorsiune așteptate de la CoreFlow ™ sunt asemănătoare (sau chiar mai mici) decât cele ale FSW.
În ceea ce privește stabilirea unei comparații cu alte procese pentru fabricarea canalelor încorporate, prelucrarea din solid, urmată de fixarea mecanică sau lipirea unui capac pentru etanșarea canalului ar trebui să aibă o distorsiune mai mică decât CoreFlow ™. Dacă, în schimb, se folosește o tehnologie de sudare prin fuziune pentru a sigila capacul după prelucrare, temperaturile de vârf experimentate de material vor fi mai mari decât cele ale CoreFlow ™, ceea ce poate contribui la o distorsiune mai semnificativă.
Un compromis ar putea fi găsit printre mai mulți factori, inclusiv:
- Capacitatea și costul procesului general
- Fiabilitate de etanșare și performanță la presiune
- Costurile de întreținere asociate cu garniturile și șuruburile
- Costuri suplimentare de prelucrare pre și post
Există vreo deteriorare a proprietăților mecanice datorită procesului?
O reducere a rezistenței este observată în HAZ atunci când se prelucrează cu aliaje tratabile termic CoreFlow ™ (2xxx, 6xxx și 7xxx) în condițiile T6. Acest lucru nu este de așteptat pentru stările T4 sau pentru aliajele întărite (1xxx și 5xxx).
Ar trebui să se aștepte un comportament similar pentru alte metale care fac obiectul anchetei (de exemplu, Cu, Ti, Mg).
Care este viteza de procesare a CoreFlow ™?
Formarea și geometria canalului sunt influențate de raportul dintre rotația sondei și viteza de deplasare a acesteia.
La începutul dezvoltării, au fost produse secțiuni transversale dreptunghiulare pentru plăci de aluminiu AA6082-T6 cu grosime de 15 mm atunci când se combină viteze de rotație de 400-600 t / min cu viteze de traversare de 25-50 mm / min.
Pentru o geometrie de canal specifică, procesul poate fi optimizat în continuare prin creșterea atât a vitezei de traversare, cât și a vitezei de rotație, menținând astfel raportul constant. Cu toate acestea, această optimizare necesită eforturi extinse, iar rezultatele sale vor fi limitate la un anumit material și la dimensiunile sondei. Mai mult, performanță și randament sporit ar putea fi realizate prin schimbarea designului sondei, de exemplu, prin introducerea de caracteristici suplimentare sau prin optimizarea căii de extrudare.
Prin prelucrarea și resigilarea canalelor de răcire într-un singur pas, CoreFlow ™ consolidează multiple operațiuni de fabricație, oferind în mod inerent un avantaj în comparație cu tehnologiile tradiționale (de exemplu frezare, urmată de etanșare prin lipire / șurubare / sudare). Acest lucru creează un proces mai simplu și o metodă de fabricație mai eficientă și mai ecologică, utilizând mai puține materii prime, producând mai puține deșeuri și, prin urmare, cântărind mai puțin decât omologul său convențional fabricat prin frezare și sigilare.
Se poate observa, totuși, că CoreFlow ™ este un proces nou, aflat în continuă dezvoltare. Ca punct de referință, merită menționat faptul că FSW, când a fost inventat la TWI în 1991, a fost un proces lent în comparație cu tehnologiile de sudură prin fuziune obișnuite. Patrimoniul TWI în inovație și dezvoltarea proceselor a permis creșterea semnificativă a vitezei FSW după doar câțiva ani, îmbunătățind drastic competitivitatea procesului. Cheia pentru deblocarea unor viteze de procesare mai mari va fi proiectarea instrumentelor, unul dintre domeniile cheie de expertiză ale TWI.
Care este rugozitatea suprafetei peretilor interni?
Figura de mai jos prezinta profilul suprafetei fiecarei suprafete interne din incercarile noastre pe placi AA6082-T6 cu grosimea de 15 mm.
Fundul canalului este cea mai neteda suprafata interna, prezentand un Ra de 1,27 µm. Aceasta finisare a suprafetei este in concordanta cu gama de calitate oferita de frezarea finala (de obicei variaza intre 0,8 si 6,3 µm). Pe suprafata inferioara poate fi observat un model liniar de ondulatii circulare produse de marginea anterioara a sondei (subfigura a). Suprafata tavanului prezinta, de asemenea, un model liniar de semne circulare, desi cu directie opusa celei prezentate de suprafata inferioara (subfigura b). Tavanul prezinta o textura mai aspra, reflectata de valoarea Ra mai mare de 25,49 µm.
Peretii laterali de pe AS si RS prezinta o valoare Ra de 18,61 si respectiv 25,11 μm. Asa cum se arata in figura (subfigurile c, d), ambele suprafete sunt caracterizate printr-o morfologie asemanatoare scarii, orientata departe de directia de deplasare.
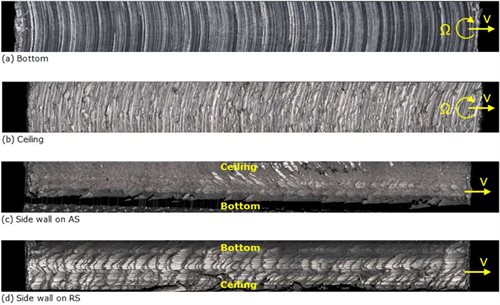
Caracterizarea rugozitatii suprafetei interioare a canalului: (a) Partea de jos; (b) Plafon; (c) Peretele lateral pe AS; (d) Peretele lateral pe RS.
Asigurarea unor valori de rugozitate consistente si repetabile poate permite ca aceasta sa fie o caracteristica de proiectare. Unele schimbatoare de caldura sunt texturate pentru a favoriza turbulenta in lichidul de racire (deoarece acest regim de flux imbunatateste disiparea caldurii prin convectie). Pentru produsele care necesita flux laminar, TWI dezvolta metode de imbunatatire a finisarii suprafetei interioare prin optimizarea procesului sau tehnici de post-procesare. Cateva exemple sunt gravarea chimica, prelucrarea cu flux abraziv (AFM) sau prelucrarea cu jet abraziv asistata in pat fluidizat (FB-AJM).
Cat de aproape pot fi pozitionate doua canale adiacente?
Canalele separate de peretele unui material subtire de 1-2 mm au fost fabricate cu succes in AA6082-T6 cu o grosime de 5 mm. Cu toate acestea, s-au observat diferite efecte termice datorita acumularii de caldura in timp ce reprocesam o mica zona locala cu mai multe treceri. Optimizarea procesului este necesara pentru a atenua acest lucru.
Unul dintre cele mai recente subiecte de cercetare este crearea nu numai a canalelor, ci si a zonelor de sub suprafata. Acest lucru ar fi util pentru formarea rezervoarelor in aplicatiile de transport / manipulare a lichidelor, pentru incorporarea instrumentelor sau a greutatii usoare a structurilor existente.
Care sunt proprietatile subprodusului de sarma pe care il produce CoreFlow ™?
TWI cerceteaza daca materialul extrudat de pe placa sub forma de sarma poate fi utilizat ca materie prima pentru alte procese, cum ar fi fabricarea aditiva pe baza de sarma sau ca umplutura in sudarea prin fuziune. CoreFlow ™ este capabil sa extraga o lungime nelimitata de sarma de pe o placa sau dintr-o teava.
Acest proces, etichetat ForgeWire ™, este de mare interes pentru producerea unei bobine de sarma din materiale cu extrudabilitate slaba, cum ar fi aliajele de aluminiu sau magneziu. Producatorii de sarma sau dezvoltatorii de procese de fabricatie aditiva au acum o optiune rapida pentru producerea de sarma cu compozitie chimica adaptata si din formulari experimentale de aliaj (de exemplu, aluminiu-litiu sau aluminiu-scandiu), posibil chiar direct de la produsul laminat sau de la piesele turnate.
Pe ce aplicatii ar putea fi utilizate CoreFlow ™?
CoreFlow ™ isi propune deja sa gaseasca aplicatii revolutionare in fabricarea schimbatorilor de caldura, a sistemelor de racire, a gestionarii integrate a fluidelor si a greutatii usoare a structurilor.
Iata o lista de aplicatii potentiale:
- Tavi pentru baterii EV cu canale de racire integrate incorporate in structura metalica.
- Incorporati canale in carcasele motorului cu pereti subtiri pentru racirea activa, reducand greutatea si imbunatatind performanta motorului.
- Racirea motorului aeronavei prin retele de canale incorporate direct in nacele.
- Sisteme hidraulice de racire care permit inlocuirea furtunurilor, conductelor si armaturilor.
- Racirea serverelor de date, a infrastructurilor de comunicatii si a instalatiilor radar.
- Gestionati sarcina termica in echipamentele de fabricatie.Retele de lubrifiere.
- Incorporarea instrumentelor intr-o structura.Gestionarea cablurilor subterane.
- Ponderarea suplimentara a pieselor existente.
CoreFlow ™ necesita echipament specializat?
Incercarile au fost efectuate pe o masina ESAB SuperStir ™ (prezentata in figura de mai jos) cu un sistem de gantry FSW construit special prevazut cu sistemul stational de umar TWI.
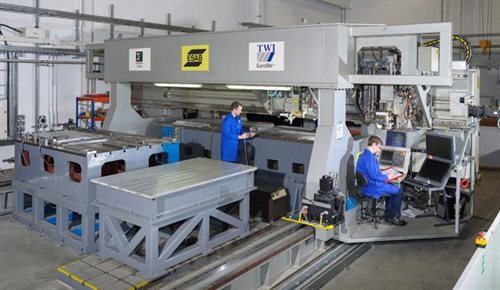
Sonda utilizata este o sonda cilindrica filetata din aliaj de cobalt-nichel-crom, combinata cu un umar plat static. Umarul avea patru gauri radiale pozitionate ortogonal, pentru a permite expulzarea materialului plastifiat. Sonda si umarul sunt proiectate special pentru materialul care urmeaza sa fie prelucrat si pentru aplicatia necesara.
Urmatoarea etapa a evolutiei CoreFlow ™ este dezvoltarea unui sistem universal de cap pentru masini de gaurit CNC si brate robotizate, facand procesul implementabil cu o investitie de capital mica. Pentru FSW, sistemele universale de cap au fost deja dezvoltate de TWI.
Incercarile robotizate sunt deja planificate pentru anul viitor, unde robotii ABB vor fi echipati cu un instrument CoreFlow ™ si vor fi folositi pentru a incorpora canale pe suprafete metalice tridimensionale.
Ce geometrii de canal pot fi realizate?
Geometria sectiunii transversale a canalului pare sa varieze de la dreptunghiular la triunghiular, in functie de parametrii utilizati. Toate canalele au o suprafata inferioara plana, situata in concordanta cu adancimea de lungime a sondei utilizata. Partea de jos a canalului prezinta muchii bine definite, coincidente cu conturul sondei.
In viitor, s-ar putea realiza forme suplimentare prin schimbarea parametrilor procesului si a formei sondei. Mai mult, schimband adancimea sondei in mod dinamic sau in trepte, ar putea fi realizate geometrii 3D si ar putea fi create canale la mai multe niveluri de adancime, permitand traversarea si modele mai complexe.
Care este adancimea maxima, latimea si grosimea plafonului unui tunel CoreFlow ™?
Dimensiunile canalului, inclusiv adancimea acestuia, depind in principal de geometria sondei. O regula generala in ceea ce priveste instrumentele care sunt de obicei utilizate in FSW este ca raportul de aspect ar trebui sa scada sub 0,5, ceea ce inseamna ca lungimea acestuia ar putea fi putin mai lunga (de pana la 2 ori) decat diametrul sau. La randul sau, acest lucru inseamna ca adancimea canalului ar putea fi de pana la doua ori latimea canalului.
Cu toate acestea, grosimea plafonului depinde si de parametrii de proces utilizati si nu numai de proiectarea sondei. Cresterea vitezei de rotatie a sondei, de exemplu, va creste viteza de extrudare, lasand mai putin material in urma in canal si, prin urmare, creand un plafon de canal mai subtire.
Comercial
Nu stiu cum sa proiectez CoreFlow ™ in produsele mele - cum va poate ajuta TWI?
TWI ofera totul, de la sfaturi cu privire la proiectarea componentelor, selectia proceselor si probleme de calitate, depanare, evaluari de fezabilitate si teste de pre-productie, aplicatii si dezvoltare de echipamente prototip. TWI ofera membrilor sai si partilor interesate acces la tehnologii de ultima generatie in domeniul sudarii, alaturarii, inspectiei si tehnologiilor auxiliare, aplicabile in mai multe sectoare industriale. Facilitatile noastre de cercetare se extind si la evaluarea integritatii structurale si la caracterizarea materialelor.
Cu aceste capabilitati, TWI va poate ajuta in proiectarea si prototiparea urmatoarei generatii de produse folosind CoreFlow ™ ca tehnologie de abilitare.
Care este starea IP a tehnologiei CoreFlow ™?
TWI a solicitat protectia brevetului in teritoriile din intreaga lume, pe baza publicatiei PCT numarul WO2018083438.
Cum pot afla mai multe despre obtinerea unei licente pentru utilizarea CoreFlow ™?
TWI intentioneaza sa ofere licente in baza brevetelor CoreFlow ™ pe baza de site, in conformitate cu modelul FSW. In acest sistem, taxa de licenta va fi stabilita pe baza numarului de site-uri pe care este utilizat CoreFlow ™ (mai degraba decat pe baza cantitatilor de piese procesate sau a produselor vandute). Cu toate acestea, TWI sunt intotdeauna dispusi sa revizuiasca acest acord de la caz la caz, urmarind sa acorde prioritate adoptarii si diseminarii tehnologiei.
Pentru informatii suplimentare referitoare la acordarea de licente pentru aceasta tehnologie, va rugam sa contactati departamentul IP al TWI la ipr@twi.co.uk.
Exista publicatii tehnice disponibile pe CoreFlow ™?
Au fost pregatite si publicate mai multe publicatii tehnice referitoare la CoreFlow ™.
Un articol de specialitate din renumita revista MTDCNC a fost publicat recent si poate fi gasit la acest link. https://mtdcnc.com/magazines/mtdcnc/twi-develops-sub-surface-machining
Un articol TWI Insight poate fi gasit la acest link. https://www.twi-global.com/media-and-events/insights/coreflow-a-sub-surface-machining-process
In plus, un manuscris stiintific intitulat „Dezvoltarea unei noi variante stationare a umarului de canalizare prin frecare” a fost scris de catre inventatorul CoreFlow ™ Dr. Joao Gandra si va fi publicat in curand intr-un jurnal stiintific.