Testul curentului Eddy este o metodă de inspecție nedistructivă (NDT), utilizată într-o varietate de scopuri, inclusiv pentru detectarea defectelor, măsurători ale grosimii materialului și acoperirii, identificarea materialului și stabilirea stării de tratare termică a anumitor materiale.
Ce este metoda de testare a curentului Eddy?
Metoda de testare a curentului Eddy este una dintre mai multe metode de testare nedistructivă care folosește principiul electromagnetismului pentru detectarea defectelor în materialele conductoare. O bobină special concepută, alimentată cu un curent alternativ, este plasată în apropierea suprafeței de testare, generând un câmp magnetic în schimbare care interacționează cu partea de testare și produce curenți de vârstă în apropiere.
Variațiile în fazele de schimbare și amploarea acestor curenți sunt apoi monitorizate prin utilizarea unui receptor-bobină sau prin măsurarea modificărilor la curentul alternativ care curge în bobina de excitație primară.
Variațiile de conductivitate electrică, permeabilitatea magnetică a piesei de testare sau prezența oricăror întreruperi, vor provoca o schimbare a curentului și o modificare corespunzătoare a fazelor și amplitudinii curentului măsurat. Modificările sunt afișate pe un ecran și sunt interpretate pentru a identifica defectele.
Cum funcționează testarea curentului Eddy?
Procedeul se bazează pe un material caracteristic cunoscut sub numele de inducție electromagnetică. Atunci când un curent alternativ este trecut printr-un conductor - de exemplu, o bobină de cupru - un câmp magnetic alternativ este dezvoltat în jurul bobinei și câmpul se extinde și se contractă pe măsură ce curentul alternativ crește și scade. Dacă bobina este apoi apropiată de un alt conductor electric, câmpul magnetic fluctuant care înconjoară bobina pătrunde materialul și, prin Legea lui Lenz, induce un curent curge în conductor. La rândul său, acest curent Eddy își dezvoltă propriul câmp magnetic. Acest câmp magnetic „secundar” se opune câmpului magnetic „primar” și, astfel, afectează curentul și tensiunea care curg în bobină.
Orice modificare a conductivității materialului examinat, cum ar fi defectele de suprafață aproape sau diferențele de grosime, vor afecta magnitudinea curentului. Această schimbare este detectată folosind fie bobina primară, fie bobina de detecție secundară, care constituie baza tehnicii de inspecție a încercărilor de curent curent.
Permeabilitatea este ușurința în care un material poate fi magnetizat. Cu cât este mai mare permeabilitatea, cu atât este mai mică adâncimea de penetrare. Metalele nemagnetice, cum ar fi oțelurile inoxidabile austenitice, aluminiu și cupru au o permeabilitate foarte mică, în timp ce oțelurile feritice au o permeabilitate magnetică de câteva sute de ori mai mare.
Densitatea curentului este mai mare, iar sensibilitatea la defecte este cea mai mare, la suprafață și aceasta scade odată cu adâncimea. Viteza scăderii depinde de „conductivitate” și „permeabilitate” a metalului. Conductivitatea materialului afectează adâncimea de penetrare. Există un flux mai mare de curent Eddy la suprafață în metale cu conductivitate ridicată și o scădere a penetrării în metale precum cupru și aluminiu.
Adâncimea de penetrare poate fi variată modificând frecvența curentului de alternanță - cu cât este mai mică frecvența, cu atât mai mare este adâncimea de penetrare. Prin urmare, frecvențele înalte pot fi utilizate pentru a detecta defecte de suprafață apropiată și frecvențe joase pentru a detecta defecte mai profunde. Din păcate, pe măsură ce frecvența este redusă pentru a da o penetrare mai mare, sensibilitatea de detectare a defectelor este de asemenea redusă. Prin urmare, există, pentru fiecare test, o frecvență optimă pentru a oferi adâncimea de penetrare și sensibilitatea necesare.
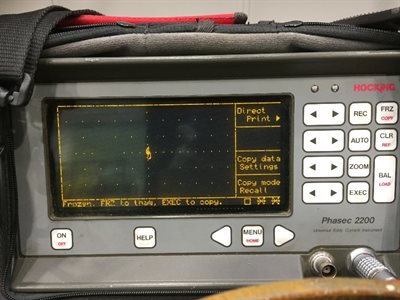
Standarde și calibrare
Toate sistemele trebuie calibrate folosind standarde de referință adecvate - ca în cazul oricărei metode NDT și sunt o parte esențială a oricărei proceduri de testare curentă. Blocurile de calibrare trebuie să fie din același material, condiția de tratament termic, forma și dimensiunea articolului care trebuie testat.
Pentru detectarea defectelor, blocul de calibrare conține defecte artificiale care simulează defecte, în timp ce, pentru detectarea coroziunii, blocul de calibrare are grosimi diferite. Metoda actuală necesită un operator de înaltă calificare - instruirea este esențială.
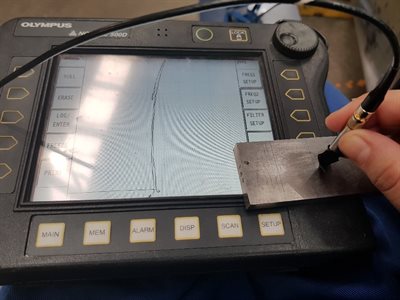
Avantaje
- Capabil să detecteze fisuri de suprafață și aproape de suprafață de 0,5 mm
- Capabil să detecteze defectele prin mai multe straturi, inclusiv acoperiri de suprafață ne-conductoare, fără interferențe din defectele plane
- Metoda fără contact care face posibilă inspecția suprafețelor la temperaturi ridicate și a celor subacvatice
- Eficient pe obiecte de testare cu geometrii complexe fizic
- Oferă feedback imediat
- Echipamente portabile și ușoare
- Timp de pregătire rapidă - suprafețele necesită o curățare prealabilă și nu este necesar cuplarea
- Capabil să măsoare conductibilitatea electrică a obiectelor de testare
- Poate fi automatizat pentru inspectarea pieselor uniforme, cum ar fi roți, tuburi ale cazanului sau discuri cu motor aerian
Limitări
- Poate fi utilizat numai pe materiale conductoare
- Adâncimea de penetrare este variabilă
- Foarte sensibil la schimbări de permeabilitate magnetică - încercarea de sudare a materialelor ferromagnetice este dificilă - dar cu detectoare digitale de defecte și design sondă, nu este imposibilă
- Nu se pot detecta defectele care sunt paralele cu suprafața obiectului de testare
- O interpretare atentă a semnalului este necesară pentru a diferenția între indicațiile relevante și cele nerelevante
Aplicații
- Inspecția pieselor sau componentelor, inclusiv:
Îmbinări sudate
Alezajele tuburilor în funcțiune
Alezajele găurilor de șurub
Tuburi metalice
Sudurile de agitare prin frecare
Lame de turbină cu gaz
Suduri cu duze în reactoarele nucleare
Butuci de elice pentru uragane
Poduri din fontă
Lame de turbină cu gaz
- Detectarea defectelor, inclusiv:
Defecte de rupere a suprafeței
Defecte liniare (mici ca 0,5 mm adâncime și 5 mm lungime)
fisuri
Lipsa fuziunii
Coroziune generalizată (în special în industria aeronavelor pentru examinarea piei de avioane)
Identificarea atât a metalelor feroase, cât și a celor neferoase și a anumitor aliaje - în special a aliajelor de aluminiu
Stabilirea stării de tratament termic
Determinarea dacă o acoperire nu este conductivă
Verificarea tratamentului termic al metalelor
Eddy Current Array
Matricea de curent Eddy (ECA) este un ansamblu de senzori sau bobine cu curent unic care sunt multiplexate într-o anumită ordine pentru a obține sensibilitatea dorită. Există multe modele diferite de sonde cu curent curent, inclusiv sonde flexibile, sonde căptușite sau degete încărcate cu arc.