D J Abson (a) , Y Tkach (a) , I Hadley (a) V S Wright (b) and F M Burdekin (c)
(a) TWI
(b) Consultant, recently retired; formerly General Manager IRD, Rolls-Royce
(c) Formerly Professor at University of Manchester Institute of Technology
Published in Welding Journal, vol.85, no.3, March 2006, pp.63-69.
In Part 1, the similarities and differences between the exemptions from PWHT in several current codes are reviewed, and some rationalisations are considered. Part 2 of this article will consider a fracture mechanics assessment of steel toughness requirements.
Abstract
Post-weld heat treatment (PWHT) is applied to steel assemblies primarily to reduce the likelihood of brittle fracture by reducing the level of tensile welding residual stresses and by tempering hard, potentially brittle, microstructural regions. For large steel assemblies in particular, PWHT can be an expensive operation, and there is thus an economic incentive to avoid PWHT, wherever possible. Whether PWHT is necessary depends on the fracture toughness at the minimum service temperature, the stress levels and the size of any flaws which may be present. According to current fabrication codes, some structures (for example, where thickness is low) are exempt from PWHT. However, the exemptions differ between codes, and it would be desirable to effect some unification of these differing requirements. The present article reviews exemptions from PWHT in several current codes, and considers the similarities and the differences between them, including maximum permitted thickness for as-welded conditions, the associated toughness requirements (in terms of the Charpy test) and what may be done to effect some rationalisation. The views of representatives of user groups have been obtained in compiling this article.
Introduction
Conventional welding processes, which rely upon the local melting and fusion of material, generate significant residual stress distributions in the weldment. The magnitude of these stresses can, under conditions of high restraint, approach the yield strength of either the parent or weld materials. Post-weld heat treatment is applied to welded steel assemblies, primarily to reduce the likelihood of brittle fracture. The benefits of PWHT include a significant reduction of tensile residual stresses in the weld joint and, to a lesser extent, tempering of the heat-affected zone and the weld metal microstructures. PWHT is required where there is a risk of environmentally-assisted cracking.
PWHT of C-Mn steels is typically carried out at approximately 600°C, for one hour per 25mm of thickness. The PWHT of large steel assemblies is an expensive process, owing to the long hold times and slow heating and cooling rates involved, and also due to the high cost of down-time, particularly where PWHT follows the repair of an existing fabrication. It is therefore greatly desired that exemption from PWHT be achieved, where possible.
Current design codes in the pressure vessel and piping industries, such as the BSI and ASME codes, specify that PWHT is required if the thickness of the parts being welded exceeds a specified value, that limit usually depending on the Charpy test properties of the material and the minimum service temperature required. This approach provides a simple and direct method for determining whether PWHT is required and, since the limiting thickness criterion has been in use for many years, it can be considered to have been validated by custom and practice. However, the degree of conservatism of the codes is difficult to assess, and anomalies in limiting thickness values between different codes are known to exist. In the general structural industry for bridges, buildings and offshore structures, there is considerably more scope for using thick steel in the as-welded condition, but with increasing toughness requirements in terms of either higher Charpy energy absorption or lower temperatures for a reference level of energy absorption. There is, therefore, significant scope for extending the boundaries of exemption from PWHT.
There have been many years of research, principally carried out by or on behalf of the electric utility and petrochemical processing industries, examining the consequences for welded steel structures, vessels and pipe-work of carrying out repairs without PWHT. Of principal interest have been thick section C-Mn and low alloy steels, for which controlled deposition repair procedures have been devised. Some codes now include provision for repair without PWHT. [1-3] From time to time there have also been investigations aimed at providing recommendations for acceptable limits for the as-welded condition for general structural conditions. [4,5]
It is recognised that steel making technology has changed over the last thirty years or so. However, steel specifications do not always reflect these changes. For example, U.S. steel specifications commonly allow steels with a maximum carbon content in excess of 0.2%, and limits for S and P of 0.035%, and sometimes more. As a consequence, wide variations in weldability and in toughness can occur among steels that meet the same specification, particularly when steels are produced in parts of the world where steel making technology lags behind best practice. The fabrication codes were generally devised for older, normalised steels with higher carbon contents [6,7] , and often with no toughness requirement.
This present article compares and contrasts the current rules and guidelines present in various fabrication standards (mainly U.S.A. and U.K.) regarding the PWHT requirements of welds and the limits for as-welded construction made in pipes, pressure vessels and structures, including bridges, buildings and offshore structures, as discussed below. In addition this article examines a number of methods available for gaining exemption from PWHT, including specially designed weld repair procedures and a case-specific fracture mechanics approach (in Part 2). This investigation relates only to C-, C-Mn and low alloy steels. Some of the similarities and differences are considered, and testing required to move towards elimination of the apparent anomalies is considered. In compiling this article, the views of representatives of fabricators and end users have been sought.
The objectives of the study were to identify the types of materials where industry considers that there are grounds for seeking wider exemption from PWHT; to compare and contrast the limiting thickness requirements above which PWHT is required and the associated Charpy test requirements for the as-welded condition in standards relevant to the fabrication industry; to investigate the methods available for gaining exemption from PWHT, namely the use of specially designed repair procedures and the specification of a minimum Charpy energy, calculated by a fracture mechanics approach; and to identify whether a future programme of toughness testing and residual stress measurements on specific steels is needed to demonstrate a case for exemption from PWHT.
Review of current practice and code requirements
Fabrication standards for C-Mn steel pressure vessels, piping and offshore structures
A survey was carried out in 1971 [10] , which showed that the requirements of various codes, in terms of the material thickness above which PWHT was required, varied considerably. Later work in 1980 [11] showed that, while considerable harmonisation had taken place, significant divergence remained. More recent work by Mohr [12] and also by Salkin [13] , who reviewed the differences in thickness limits, in temperature ranges and in hold times covering a range of steel types, has highlighted the limits and provisions for exemption from PWHT. These studies showed there was stillsome variation between codes. The results are included in Table 1, where the requirements of the U.S.A. codes relate to ASME P1 to P5 steels; the Table has been extended to include requirements for Charpy test properties, and to cover a range of other codes and standards.
Table 1 Limiting thickness for which postweld heat treatment is not required for C-Mn steels according to various standards.
Code | ASME P1 Group 1/C-Mn, & BS EN Group 1 | ASME P3 Groups 1 & 2, & BS EN Group 1.4 | ASME P4 Groups 1 & 2, & BS EN Group 5.1 | ASME P5 Group 1, & BS EN Group 5.2 | Comments |
ASME VIII [14] |
32mm increase to 38mm with 93°C preheat |
16mm, 93°C preheat, C ≤0.25% |
16mm, 121°C preheat, C ≤0.15% |
16mm, 149°C preheat, C ≤0.15% |
≥27J at 20°C for 32mm and R e ≤448MPa( ≥20J at 20°C for ≥34mm and Re ≤345MPa) |
Toughness requirement increases as strength increases; allowable thickness increases as toughness increases and as strength decreases. |
ASME B31.1 [15] |
19mm |
16mm, 95°C preheat, C ≤0.25% |
13mm, 120°C preheat, C ≤0.15% |
13mm, 150°C preheat, C ≤0.15% |
No explicit Charpy test requirement in the standard. |
ASME B31.3 [16] |
19mm |
19mm |
13mm 149°C preheat |
13mm, 177°C preheat, C ≤0.15% |
R e ≤448MPa, C v ≥18J R e ≤517MPa, C v ≥20J R e ≤656MPa, C v ≥27J |
Room temperature Charpy toughness requirements for carbon- and low alloy steels: |
ASME B31.8 [17] |
32mm |
No explicit Charpy test requirement in the standard. |
API 650 [18] |
32mm increase to 38mm with 90°C preheat |
Gp I-III & IIIA (defined in the standard) C V ≥20J. Gp IV-VI C V ≥41J; Gp VIA, C v ≥48J if Q & T or TMCP |
API 620 [19] |
32mm, increase to 38mm with 93°C preheat |
PWHT required for nozzles and attachments when wall thickness exceeded. |
C v ≥34J ( ≥40J for Q&Tmp;T grades)
C v ≥34J
C v ≥40J
C v ≥27J ( ≥34J in longitudinal direction) |
Test temperature ≤ (design metal temperature -17°C).
For design metal temperature > -40°C, if tested at or below this temperature.
Acceptable for design metal temperatures ≤-40°C.
Test temperature of -196°C for liquefied hydrocarbon gases. |
AWS D1/1 [29] |
Limits set by contract drawings or specifications. |
JIS B.8243 [20] |
32mm, increase to 38mm with 95°C preheat |
16mm, C ≤0.25%,95°C preheat |
Tubing 16mm, C ≤0.15, 120°C preheat; PWHT all thicknesses of vessel |
Tubing 16mm, C ≤0.15, Cr ≤3.0, 120°C preheat; PWHT all thicknesses of vessel |
R m <490MPa, C V ≥20J R m ≥490MPa, C V ≥27J |
At T ≤minimum operating temperature. |
Stoomwezen [21] |
32mm, C ≤0.23%, may increase to 40mm |
Fine-grained steel: C ≤0.23 and CE ≤0.55 and R e ≤370MPa and KV (perpendicular) ≥31J at 0°C and also KV (parallel) ≥27J at -50°C and 32mm < t ≤40mm and weld metal KV (perpendicular) ≥31J at 0°C, and as long as there is no accumulation of weldments or extensive local stiffening, and a hydrotest is carried out.
Fine-grained steel: C ≤0.23 and CE ≤0.55 and R e ≤450MPa and t ≤32mm and as long as there is no accumulation of weldments or extensive local stiffening, there is no toughness requirement. |
BS 2971 [22] |
35mm |
No Charpy test requirement. |
BS 1113 [23] |
30mm, increase to 35mm with 100°C preheat, C ≤0.25% |
13mm, increase to 35mm with 100°C preheat, C ≤0.25%, |
≤13mm thick and ≤127mm diameter, C ≤0.15% |
≤13mm thick and ≤127mm diameter, C ≤0.15% |
C v >40J |
BS EN 12952 [24] |
<35mm |
<13mm |
<13mm |
C v ≥27J for transverse specimens (preferred) or C v ≥35J for longitudinal. |
T CV ≤ lowest scheduled operating temperature (T CV ≤20°C). |
BS 2633 [25] |
30mm, increase to 35mm 100°C preheat, C ≤0.25% |
≤12.5mm thick and ≤127mm diameter |
≤12.5mm thick and ≤127mm diameter, 120°C preheat |
≤12.5mm thick and ≤127mm diameter, 150°C preheat, C ≤0.15% |
No Charpy test requirement. |
PD 5500 [26] |
35mm, increase to 40mm if C v ≥27J at -20°C |
12.5mm, increase to 19mm with 100°C preheat |
PWHT required for all thicknesses |
PWHT required for all thicknesses |
PD 5500 [26] (Service temperature <0°C) |
40mm, but see comments |
R e <450MPa, C V ≥27J) R e ≥450MPa, C V ≥40J) |
T CV =2.94(MDMT -10)°C(PD 5500 Annex D) |
PrEN 13445 [27] |
35mm |
≤15mm thick, or ≤13 mm thick and ≤120 mm diameter |
≤15mm thick, or ≤13 mm thick and ≤120 mm diameter and design temperature <480°C |
C v ≥27J or C v ≥40J |
Test temperature depends on strength, toughness level and design reference temperature. |
EEMUA 158 [28] |
Minimum design throat thickness: - 40mm nodes 50mm plain regions |
R e ≥275 MPa, C V ≥27J R e ≥355 MPa, C V ≥36J R e ≥450 MPa, C V ≥45J |
C v at -40°C, for assumed MDMT = -10°C. |
BS 5950 [30] & BS 5400 [31] |
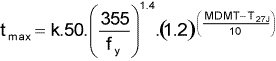
|
C v required at MDMT, k = 2 for as-welded joints but reduces with stress concentrations present. |
Several of the codes have a similar thickness limit, at ~32mm, above which PWHT is required. Provision is made in several codes [14,18-20,25] to extend this limit to 38 or 40mm if certain conditions, generally the imposition of a preheat of the order of 93°C (200°F), are met. The notable exceptions are ASME B31.1 [15] and B31.3 [16] , with a thickness limit of 19mm, and EEMUA 158 [27] that specifies a limit of 40mm for nodes, with a limit of 50mm applying to other regions. The apparent harmony is, however, in part illusory, because the steels employed in the U.S.A. and the U.K. are generally different inchemical composition (an issue which is considered in more detail in the Discussion), and may well have different inherent Charpy test properties.
It should be noted that the basic requirements of BS 1113 [22] and BS 2633 [24] , which are shown in Table 1, relate to steels with ≤0.25%C, and those of Stoomwezen [20] to steels with ≤0.23%C; in these standards, PWHT is required for steels with higher carbon contents. In BS 2633 [24] , PWHT is not required for steels ≤35mm thick if the service temperature is above 0°C, while PD 5500 [25] has the same requirement for steels up to 40mm thick. In Pr EN 13445 [26] , PWHT is only necessary in special cases, for example in H 2S service. In some of the British Standards [21,24,25] , PWHT is required, even up the limiting thickness shown, if it is specified by the purchaser.
The general trends revealed by the tabulation are for the permitted thickness without PWHT to decrease with increasing alloy content of steels and/or for increased preheat to be required, together with reductions in maximum carbon level permitted. For low alloy steels containing [22] 1.5%Cr and [22] 0.5%Mo, (including ASME P4 groups 1 and 2 steels) and also for 2.25%Cr-1%Mo steels (including ASME P5 group 1 steels), there is greater uniformity among the standards, and there are some strong similarities between the BS 2633requirements and those of ASME VIII and ASME B31.1 and B31.3.
In Table 1, it will be noted that in ASME VIII [14] , API 650 [18] , BS 1113 [22] and BS 2633 [24] , there is a marginal increase in the thickness limit if a preheat at a minimum temperature of ~93°C (200°F) is used. The reason for this is not known, and has not been discovered in the contacts made with representatives of the fabrication industry. It may reflect an anticipated increase in toughness or avoidance of hard local brittle zones from a slight reduction in as-welded HAZ hardness, as well as a reduced likelihood of hydrogen-assisted fabrication cracking.
Fabrication standards for buildings and bridges
The material thickness requirements for bridges and buildings, as specified in BS 5950:2000 [30] and BS 5400:2000 Part 3 [31] , have been examined. These specifications are much less prescriptive regarding requirements for exemption from PWHT; most welded connections in bridges and buildings, including those in thick sections, are left in the as-welded condition, and the emphasis is on the use of materials with sufficient fracture toughness not to require PWHT. Indeed, BS 5950 does not consider PWHT at all. However, these codes do provide material thickness limits. Unlike some of the pressure vessel and piping codes examined previously, the limiting thickness requirements are dependent upon service temperature, yield strength and Charpy impact properties.
A summary of strength and impact values for current European structural steel products is given in Ref. [5] . All the new European structural steel grades are supplied to a minimum Charpy impact level; the minimum Charpy toughness requirements are 27J at -50°C for most grades, with some requirements being 40J at -20°C (which is approximately equivalent to 27J at -30°C). However, there may be a limiting thickness up to which the impact toughness is guaranteed. For example in BS EN 10025 [32] , this limiting thickness for non-alloyed grades is 250mm for plates and 100mm for sections.
The limiting thickness values in BS 5950 [30] and BS 5400 [31] are presented as general equations; the form of these equations is the same for both specifications, although differences exist in calculating the so-called k-factor.
The equations, the background to which is explained in more detail in Ref. [5] , are shown below.
T min ≥ T 27J - 20:BS 5950 & BS 5400:
BS 5400: not permitted.
where:
t |
is the maximum permitted thickness of the part under stress in mm; |
k |
is the k-factor (see below); |
σy |
is the nominal yield strength of the part; |
T min |
is the design minimum temperature of the part in °C; |
T 27J |
is the temperature in degrees Celsius for which a minimum Charpy energy of 27J is specified by the product standard for impact tests on longitudinal V-notch test pieces. |
The k-factor is the product of four sub-factors relating to susceptibility to brittle fracture, as follows:
k=k d.k g.k σ .k s
and takes values ranging from <0.25 to 4. Low values of k denote higher susceptibility to brittle fracture, e.g. high applied stress, high strain rate or the presence of stress concentrations. The sub-factors each account for a different aspect of susceptibility to brittle fracture, as follows:
- k d accounts for the weld detail, and takes values between 0.5 and 2, which can be increased by 50% if PWHT is applied;
- k g accounts for the presence of gross stress concentrations and takes values up to 1;
- k σ takes account of stress levels, with values ranging from 1 to 2
- k s takes account of high strain rates, with values of 0.5 (for areas likely to be loaded under impact) and 1 (for all other areas).
As an example, the maximum permitted thickness of a grade 355 steel in the as-welded condition, subjected to Charpy testing at the material design minimum temperature (MDMT), would be 50mm for the condition k = 1, i.e. with simple weld details, quasi-static strain rates and no gross stress concentrations. This is broadly comparable with the upper range of allowable thicknesses of Table 1. However, the limiting thickness for the same as-welded joint could be a slow as 14mm under the same applied stresses and strain rates, if gross stress concentrations and poor weld details are present. If high-strain-rate loading also applies, e.g. bridge parapets, it could be even lower at 7mm. Conversely, for simple welded joints under low applied stress, the limiting thickness could be as high as 100mm, and even 150mm if the fabrication is subjected to PWHT.
The fracture avoidance rules given in BS5400 Part 3 [31] are based on fracture mechanics calculations broadly similar to those described in Part 2 of this article, calibrated against other considerations such as the results of full-scale tests on simulated bridge details, and case histories of bridge failure. Details of these calculation methods are described in reference 5, and a comparison is made with the work carried out in the present investigation in Part 2 of this article.
Eurocode 3 - design of steel structures
The requirements of Eurocode 3 [33] have also been examined. Note that the document examined is a draft for development (DD ENV), and so is subject to change before final issue as a Eurocode. The document contains a procedure based on fracture mechanics principles and the Master Curve correlation between fracture toughness and Charpy energy.
Basically, the procedure determines the required fracture toughness for a steel component, depending on factors such as:
- Steel strength grade.
- Section thickness.
- Loading speed.
- Lowest service temperature.
- Applied stress.
- Application of PWHT.
- Type of structural element.
- Consequences of failure.
The provisions of the draft Eurocode [33] are fairly similar to those of BS5400 [31] (and therefore similar to the upper range of Table 1) for the case k = 1, i.e. where there are no gross stress concentrating features or fatigue-sensitive weld details. However, whereas under BS5400 the maximum permitted thickness for the same as-welded joint under similar applied stress and at a similar strain rate could range from 14 to 50mm (as illustrated in the previous section), it would remain 50mm throughout under the draft Eurocode.
The draft Eurocode [33] and BS5400-3 [31] requirements are compared and contrasted in detail in Ref. [5] , where concern is expressed at some of the potentially unsafe provisions of the former.
Review of documentation for low alloy steels
The information relating to low alloy steels in piping and pressure vessel codes, primarily from the U.S.A. and U.K., has also been reviewed. The information is also summarised in Table 1. (See Table 2 for the compositions of relevant ASME P numbers.) For such steels, there are some strong similarities in the requirements relating to exemptions from PWHT between the U.S.A. and U.K. codes; in Table 1, BS 2633 [25] stipulates a similar preheat to the U.S. codes. However, the requirements of ASME B31.3 [16] differ from the other codes, in that PWHT is not required for ASME P3 grade 1 and 2 steels up to 19mm thick, while this code requires a higher preheat for P4 grades 1 and 2 and P5 grade 1 steels. It should be recognised that the situation is appreciably more complex than these numbers in Table 1 suggest, as different recommendations apply to specific weldments. See, for example, the footnote to ASME VIII Division 1 Table UCS-56 [14] , which includes clauses relating to nozzle connections, and the welding of pressure parts to non-pressure parts. The additional requirement to gain exemption from PWHT for tubes less than or equal to 13mm thick and less than or equal to 120mm diameter in P5 type steels in Pr EN 13445 [27] is that the design temperature should exceed 480°C.
Table 2 Summary of information on relevant ASME P numbers
ASME P number | Steel types |
P1 group 1 |
C-Mn |
P3 groups 1 and 2 |
C-0.5%Mo; 0.5%Cr-0.5%Mo |
P4 groups 1 and 2 |
0.5%Cr-1.25%Mn-Si; 1%Cr-0.5%Mo; 1.25%Cr-0.5%Mo-Si |
P5 group 1 |
2.25%Cr-1%Mo; 3%Cr-1%Mo |
Discussion
Differences between material grouping systems in the ASME, CEN and British Standard codes
The grouping of materials used for welding has been carried out under the auspices of the different code standards committees in both Europe, including the U.K., and the U.S.A. In the U.S.A., steels have been allocated a P number orS number, but since 1998 materials used for welder qualification may conform to other national or international standards or specifications, provided that the requirements for mechanical properties and specified analysis limits of theP or S number are met. In the UK, materials have been given group numbers in BS 4870 [34] (for welding procedures) and BS 4871 [35] (for welder qualifications). Both of these standards have been superseded by European standards BS EN 288 [36] and BS EN 287 [37] . A submission was made to the committee compiling CR TR 15608, the draft guidelines for a metallic material grouping system [38] by Sperko [39] . In his proposed Annex to CR TR 15608, he attempted to unify the ASME and CRTR 15608 grouping. He examined 985 relevant U.S.A. steel specifications, and found the following:
- 196 steel compositions could be classified within an ASME P1 Group.
- Of the 196, only 91 C-Mn steels could be given a CR TR 15608 group number.
This study has indicated that, in terms of an ASME or CEN grouping system, material grouping does not provide a basis for exemption from PWHT. It would clearly be of considerable benefit in moving towards more uniform PWHT requirements if steel producers were to extend the practice of dual, or even multiple, certification of steels, so that greater uniformity is achieved in the compositions of steels. The practice would also facilitate the eventual unification of standards.
Code requirements
Although the fundamental details of the differences in the separate codes for pressure vessels and piping, in terms of preheat and other requirements, have not been included, Table 1 indicates that rationalisation of the PWHT exemption of all the codes would not be easy to achieve. For C-Mn steels, a comparison of codes, in terms of maximum wall thickness where PWHT is not required and maximum carbon equivalent of material permitted, has suggested an even more widely spread divergence. The codes are for different engineering applications. Differences between these may include different design stress criteria, different inherent Charpy test requirements and (through the inspection codes) different allowable defect sizes. The codes were drawn up by different professional bodies, based on extensive experience and engineering practice. Therefore differences arose and inconsistent requirements ensued. The gross differences that have arisen are likely to preclude the issue of a unified code requirement giving exemption from PWHT.
Three of the main groups of steel users with an interest in obtaining exemption from PWHT are the petrochemical industry (through EEMUA [The Engineering Equipment and Materials Users Association] Material Technology Committee), the power generation industry (through EGWP - the Electricity Generators Welding Panel) and the general structural industry. The data covered in this review suggest that reconciliation of the requirements of these two user groups may notbe possible. It would clearly be of benefit to the power generation industry to increase the thickness threshold for PWHT, for example to the 40mm embodied in EEMUA 158 [28] for C-Mn steels. Examination of the data also raises questions about the need to give a PWHT to weldments covered by BS 1113 [23] and BS 2633 [25] when the carbon content exceeds 0.25%. This limitation appears questionable, in the absence of such a condition in the other codes, but should be considered in relation to the Charpy properties of the steels concerned.
For C-Mn and Cr-Mo steels, the lower thickness threshold embodied in ASME B31.1 [15] and B31.3 [16] , compared with the other standards, may reflect the likelihood that the welding will be carried out in the field, and that defect rates and defect sizes may be greater than for shop welds. Girth welds in steel pipes have been subjected to a fracture mechanics assessment by Mohr [40] , who assumed the presence of root defects, and who concluded that the fracture resistance of pipes thicker than 19mm was at least equal to that of thinner walled pipes. As PWHT is not required by ASME B31.1 for thinner walled pipes, presumably because the fracture resistance has been found to be sufficient, Mohr questioned the need for PWHT of thicker walled pipe, a broadly similar conclusion to that implied by the calculated toughness in Part 2 of the current work, if a fixed (rather than a proportional) flaw size is assumed in the calculations. However, all of these considerations need to be seen in the context of the inherent Charpy properties of the materials concerned, and thisis not explicitly treated in some of the codes involved.
The position of the general structural industry is that the scale and size of structures is so large that PWHT of the overall structure is impracticable, and PWHT is only considered for local sub-assemblies under exceptional circumstances. Virtually all welded connections in bridges and buildings, including those in thick sections, are left in the as-welded condition, and the emphasis is on the use of materials with sufficient fracture toughness not to require PWHT. Fracture mechanics calculations broadly similar to those described in Part 2 of this article were used in defining the fracture avoidance rules given in BS5400 Part 3 [31] , and these were calibrated against other information, including the results of full-scale tests on simulated bridge details, and case histories of bridge failure. The detailed history of the piping codes is not known, but it is likely that custom and practice made a greater contribution, no doubt with some experience of failures incorporated. Also, it is noted that ASME B31.1 [15] and ASME B31.8 [17] provide for non-impact tested steels to be used. However, since the code development took place, steel-making technology has changed significantly, steel toughness levels have generally improved substantially, and (at least within Europe) steel specifications commonly incorporate impact toughness requirements. It is therefore likely that limiting thicknesses could be increased, and thus PWHT omitted, as was shown to be acceptable for the steel vessels subjected to an ECA by Leggatt et al. [41] .
General discussion
In spite of the disparities between the PWHT requirements of the pressure vessel and piping standards depicted in Table 1, some rationalisation could be effected by building on the similarities which do exist. One possible approach would be to define a modest limiting thickness, perhaps ~32mm, for which there are few additional requirements and a minimum level of absorbed Charpy energy could be assumed for the steels concerned. A greater limiting thickness could then be accommodated if additional requirements were met. This is the approach adopted in PD5500 [26] , where the additional requirement is a minimum Charpy impact toughness (of ≥27J at -20°C) for the higher level of limiting thickness of 40mm. More extensive requirements for the same limiting thickness are imposed in Stoomwezen [21] . These are C ≤0.23%, IIW CE ≤0.45, R e ≤370 N/mm 2 , both C v ≥27J at -50°C and C v ≥31J at 0°C for the parent steel, and C v ≥31J at 0°C for the weld metal. It will be noted that the codes do not mention explicitly as-welded HAZ toughness, even though this factor would probably be limiting if HAZ fracture toughness were to be measured and a detailed engineering critical assessment were to be carried out.
This present study has demonstrated that code classifications and material groupings do not provide avenues for a uniform approach across all the codes, at least for C- and C-Mn steels, for the omission of PWHT following welding. PD5500:2000 [26] provides an Appendix which can be used to justify exemption from PWHT. The justification is based on a design reference temperature calculation. However, it appears that this philosophy has been adopted only in this pressure vessel code, and the approach may not gain wide acceptance in codes for other applications. A material properties, rather than code-based, approach might be more widely acceptable. What appears to be required is a knowledge base of weldment impact value/fracture toughness properties for welds deposited with known welding parameters. It may then be possible for codes to include HAZ toughness requirement for weldments.
Conclusions
Code requirements for permitting as-welded construction without PWHT have been reviewed for C- and C-Mn and some low alloy steels, and the requirements of different codes have been compared. From this study, the following conclusions have been drawn:
- U.S.A and U.K. code requirements are generally similar in the limiting thickness of C- and C-Mn steels (including ASME P1 steels) beyond which PWHT is required for pressure vessels, piping and storage tanks, at ~32mm. However, there are differences in the chemical compositions of U.S.A. and U.K. steels which influence PWHT requirements. The major exceptions in this area are ASME B31.1 and B31.3 (limiting thickness 19mm). However, general structural codes, such as BS 5400 for bridges, BS 5950 for buildings and EEMUA 158 for offshore structures, permit significantly higher thicknesses in the as-welded condition, linked to increasing Charpy energy requirements.
- For low alloy steels containing ≤1.5%Cr and ≤0.5%Mo, (including ASME P4 groups 1 and 2 steels) and also for 2.25%Cr-1%Mo steels (including ASME P5 group 1 steels), there are some strong similarities between the BS 2633 requirements and those of ASME VIII and ASME B31.1 and B31.3. The general trends are for the permitted thickness without PWHT to decrease with increasing alloy content of steels and/or for increased preheat to be required, together with reductions in maximum carbon level permitted.
- In view of the differences which exist in the chemical compositions of broadly comparable U.S.A. and U.K. steels and the lack of consistent requirements for Charpy test properties (as far as ASME and CEN are concerned), alignment by material grouping for C-Mn steels is not universally possible as a basis for exemption from PWHT.
- Since the development of the earliest codes, steel-making technology has changed significantly, steel toughness levels have generally improved substantially, and (at least within Europe) steel specifications commonly incorporate impact toughness requirements. It is therefore likely that limiting thicknesses could be increased, and thus PWHT omitted.
- U.K. code requirements for general structures such as bridges, buildings and offshore structures permit significantly greater thicknesses to be used in the as-welded condition, linked to Charpy toughness requirements for different grades of steel, based on fracture mechanics analyses. The requirements can be expressed in terms of MDMT - T27J (the temperature difference between the material design minimum temperature and the temperature for 27 Joules energy absorption in the Charpy test) and the yield strength of the steel, for given assumptions about flaw size and stress level.
Recommendations
- Where the relevant fabrication codes require that a PWHT be carried out, consideration should be given to carrying out a fracture mechanics assessment, with the agreement of all interested parties, in order to extend the thickness beyond which PWHT is required.
- Typical Charpy test data should be reviewed and collated in terms of thickness and material type and IIW CE for steels supplied against the various standards summarised in Table 1. Following completion of the review, consideration should be given to the following cases:
- C- and C-Mn steels which would potentially allow an increase in the ASME B31.1 and B31.3 threshold thickness level for PWHT, and
- C- and C-Mn steels with <0.25%C, to establish if the BS 1113 and BS 2633 requirements are justified.
- Consideration should be given to the generation of toughness data for thicknesses >12.5mm, and where Charpy energy requirements are not unduly onerous, to see where the avoidance of PWHT can be justified.
- Steel producers should be encouraged to extend the practice of dual, or even multiple, certification of steels, so that greater uniformity is achieved in the compositions of steels, thereby facilitating the eventual unification of standards.
- Consideration should be given to introducing HAZ toughness requirements into fabrication codes.
Acknowledgements
Helpful discussions with C S Wiesner and other colleagues at TWI, and input from D J Allen, of Powergen, B Parry-Mills and M Coleman, of British Energy, and R Carroll of Foster Wheeler Energy Limited are gratefully acknowledged.
The work was carried out within the Core Research programme of TWI, which was funded by Industrial Members of TWI.
References
- ASME Boiler and pressure vessel code, Section III 'Rules for construction of nuclear facility components'. American Society of Mechanical Engineers, New York, July 2001, paragraph NB-4622.9 Temper bead weld repair.
- ASME Boiler and pressure vessel code, Section XI 'Rules for service inspection of nuclear power plant components'. American Society of Mechanical Engineers, New York July 2001, paragraph IWA-4623.1 Temper bead welding of similar materials - Shielded metal arc welding.
- National Board Inspection Code - A manual for boiler and pressure vessel inspectors, National Board of pressure Vessel Inspectors, Columbus, Ohio, USA.
- Burdekin F M: Materials aspects of BS5400:Part 6, paper 4 in The Design of Steel Bridges' Ed. K.C. Rockey and H.R. Evans, Granada ISBN 0 24611339 1, 1981.
- Ogle M H, Burdekin F M and Hadley I: 'Material selection requirements for civil structures'. Proc. IIW Int. Conf. on Welded Construction for Urban Infrastructure, 56th Annual Assembly of the IIW, 10 July 2003, Bucharest, Romania, Ed. D Dehelean, International Institute of Welding, 2003, 201-229.
- Spaeder C E, Doty W D: 'Report No. 2: ASME post-weld heat treating practices: an interpretive report'. Welding Research Council Bulletin, 407 December 1995.
- Hancock P, Chubb J P and Spurrier J: 'A new perspective on the influence of thickness and post-weld heat treatment for large scale welded joints'. J Engineering Materials and Technology 1995, pp.117, 209-214.
- BS 7910: 1999: 'Guide on methods for assessing the acceptability of flaws in metallic structures', incorporating Amendment 1.
- BS 7448: Part 2: 1997: 'Fracture mechanics toughness tests - Method for determination of KIc, critical CTOD and critical J values of welds in metallic material'.
- Nicholson S and Brook J C: 'Review of codes', Proc. Biennial Conf. On Heat Treatment'. Joint Committee Iron and Steel Inst., London, December 1971.
- Saunders G G: 'Residual stresses and their reduction'. Developments in Pressure Vessel Technology-3, Applied Science Publishers Ltd., 1980.
- Mohr W: 'Post-weld heat treatment: A review. Inspection, assessment and repair of welded structures and components'. 10th Annual North American Welding Research Conference, Ohio, 1994.
- Salkin R V: 'The desirability of unifying ideas and codes on stress relief thermal heat treatments'. FWP Journal, Part 1 Nov.1988 27-34, Part 2 Dec. 1988 5-13.
- ASME VIII Div 1: July 2001: 'Rules for construction of pressure vessels'.
- ASME B31.1: 1998: 'ASME code for pressure piping, power piping'.
- ASME B31.3: 1999: 'ASME code for pressure piping, process piping'.
- ASME B31.8: 1999: 'ASME code for pressure piping, gas transmission and distribution piping systems'.
- API 650: November 1998: 'Welded steel tanks for oil storage'.
- API 620 'Design and construction of large, welded, low-pressure storage tanks'. American Petroleum Institute, February 1996.
- JIS B 8243 - 1981: 'Construction of pressure vessels'.
- 'Rules for pressure vessels'. Vol.2 Section W 0701. 'Heat treatment of unalloyed and low alloy steel' and Section W 0702 'Heat treatment of unalloyed and low alloy steel pipes'. Dienst voor het Stoomwezen, The Hague, 1991.
- BS 2971 'Specification for Class II arc welding of carbon steel pipework for carrying fluids'. British Standards Institution, 1991.
- BS 1113: 1992: 'Design and manufacture of water-tube steam generating plant (including superheaters, reheaters and steel tube economisers)'.
- BS EN 12952: 2001: 'Water tube boilers and auxiliary installations -Part 2 Materials for pressure parts of boilers and accessories'; and Part 5 'Workmanship and construction of pressure parts of the boiler.'
- BS 2633: 1987, 'Class 1 arc welding of ferritic steel pipework for carrying fluids'.
- British Standards Institution Published Document PD 5500, 2000: 'Unfired fusion welded pressure vessels'.
- BS EN 13445 2002: 'Unfired pressure vessels, Part 4: Manufacture'.
- EEMUA 158: 1994: 'Construction specification for fixed offshore structures in the North Sea'.
- AWS D1.1/D1.1M: 2002: 'Structural welding code steel'.
- BS 5950-1:2000: 'Structural use of steelwork in building. Code of practice for design - Rolled and welded sections'.
- BS 5400-3:2000 (incorporating Corrigendum 1): 'Steel, concrete and composite bridges - Part 3: Code of practice for design of steel bridges'
- BS EN 10025: 1993:'Hot rolled products of non-alloy structural steels -Technical delivery conditions'.
- DD ENV 1993-1-1:1992 'Eurocode 3: Design of steel structures, Part 1.1 General rules and rules for buildings'.
- BS 4870: 1981 'Approval testing of welding procedures - Part 1: Fusion welding of steel'. (Superseded by BS EN 288-1: 1992 and BS EN 288-3: 1992.)
- BS 4871: 1992 'Approval testing of welders working to approved welding procedures - Part 1: Fusion welding of steel'. (Superseded by BS EN 287-1: 1992.)
- BS EN 288: Part 1: 1992 'Specification and approval of welding procedures for metallic materials - General rules for fusion welding', and BS EN 288: Part 3: 1992 'Specification and approval of welding procedures for metallic materials - Welding procedure tests for the arc welding of steels'.
- BS EN 287- Part 1: 1992 'Approval testing of welders for fusion welding -: Steels'.
- British Standards Institution, Published Document PD CR ISO 15608:2000 'Welding-guidelines for a metallic material grouping system', June 2000.
- Sperko W.J: 'Assignation of ASME Materials to the new grouping system CR TR 15608', CEN/TC 121/SC 1 N 407, June, 1998.
- Mohr W C: 'Fracture mechanics to justify the minimum thickness for PWHT: Girth butt-welded steel pipe'. Edison Welding Institute Report for Research Members MR9708, December 1997.
- Leggatt R H, Muhammed A, Smith A T and Cheaitani M J: 'Using fracture mechanics to claim exemption from PWHT - Four case studies'. TWI Report for Research Members 679/1999, May 1999.