Part 2
Click here for Part 1.
This second article on shape imperfections refers mostly to fillet welds but there are two additional butt weld imperfections that require some comment.
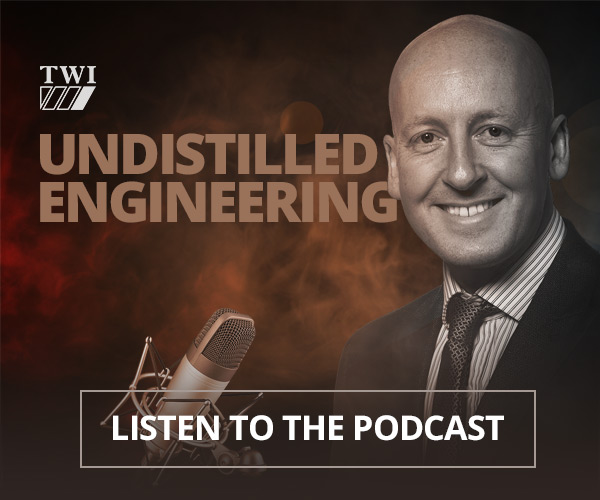
Excessive penetration (Excess penetration bead)
Fig.1. Excess penetration
Excess weld metal protruding through the root of a fusion (butt) weld made from one side only.
With pipe welding this type of imperfection may cause effects in the fluid flow that can cause erosion and/or corrosion problems.
Common causes
Penetration becomes excessive when the joint gap is too large, the root faces are too small, the heat input to the joint is too high or a combination of these causes.
Acceptance
The criteria which sets the level of acceptable penetration depends primarily on the application code or specification.
BS 2971 (Class 2 arc welding) requires that the 'penetration bead shall not exceed 3mm for pipes up to and including 150mm bore or 6mm for pipes over 150mm bore'.
BS 2633 (Class 1 arc welding) gives specific limits for smaller diameters pipes, eg for pipe size 25-50mm the maximum allowed bore penetration is 2.5mm.
ASME B31.3 bases acceptability on the nominal thickness of the weld, for instance, allowing for a thickness range of 13-25mm up to 4mm of protrusion. However, ASME notes that 'more stringent criteria may be specified in the engineering design'.
BS EN ISO 5817 (Quality levels for imperfections), which supersedes BS EN 25817, relates the acceptable protrusion to the width of the under-bead as follows:
Severity of service | Moderate, D | Stringent, B |
Limit (up to maximum) |
h ≤ 1mm + 1.0 b |
h ≤ 1mm + 0.2 b |
Maximum |
5 mm |
3 mm |
For thicknesses > 3mm where: h = height of excess & b = width of root (see Fig.1) |
Avoidance
It is important to ensure that joint fit-up is as specified in the welding procedure. If welder technique is the problem then re training is required.
Root concavity (suck-back; underwashing)
A shallow groove that may occur in the root of a butt weld.
Common causes
Root concavity is caused by shrinkage of the weld pool in the through-thickness direction of the weld. Melting of the root pass by the second pass can also produce root concavity.
This imperfection is frequently associated with TIG welding with the most common cause being poor preparation leaving the root gap either too small or, in some cases, too large. Excessively high welding speeds make the formation of root concavity more likely.
Acceptance
The root concavity may be acceptable. This will depend on the relevant standard being worked to. For example:
BS 2971 requires that:
a) there is complete root fusion
b) the thickness of the weld is not less than the pipe thickness.
ASME B31.3 requires that the 'total joint thickness, including weld reinforcement, must be greater than the weld thickness'.
BS EN ISO 5817 sets upper limits related to the quality level, eg for thicknesses > 3mm Moderate, (D), h ≤ 0.2t but max 2mm for Stringent, (B), h ≤ 0.05t but max 0.5mm. Furthermore, a smooth transition is required at the weld toes.
In effect the standards require that the minimum design throat thickness of the finished weldment is achieved. If the first two conditions of acceptance are met but the weld face does not have a sufficiently high cap, additional weld metal may be deposited to increase the throat.
Avoidance
It is important to ensure that joint fit-up is as specified in the welding procedure and that the defined parameters are being followed. If welder technique is the problem then retraining is required.
Fillet welded joints
This Section should be read in conjunction with Job Knowledge 66 Fillet welded joints - a review of the practicalities.
Excessive convexity
Fig.3. Excessive convexity
This feature is also covered by the definition for excess weld metal, see Part 1, and may be described as weld metal lying outside the plane joining the weld toes. Note that the term 'reinforcement', although used extensively in the ASME/AWS specifications is avoided in Europe as it implies that excess metal contributes to the strength of the welded joint. This is rarely the case.
Common causes
Poor technique and the deposition of large volumes of 'cold' weld metal.
Acceptance
The idealised design requirement of a 'mitre' fillet weld is often difficult to achieve, particularly with manual welding processes.
BS EN ISO 5817 acceptance is based on a mitre fillet weld shape with a specific design throat and any excess weld metal is measured in relation to this mitre surface. The limits for this imperfection relate the height of the excess metal to the width of the bead with maximum values ranging from 3mm for a stringent quality level to 5mm for a moderate quality level. Surprisingly, there is no reference to a 'smooth transition' being required at the weld toes for such weld shape.
AWS D1.1 also has limits relating width to acceptable excess as follows:
Width of weld face | Maximum convexity |
W ≤ 8mm |
2mm |
W <8 to W<25mm |
3mm |
W ≥ 25mm |
5mm |
Avoidance
Welder technique is the major cause of this problem and training may be required. It is also important to ensure that the parameters specified in the welding procedures specification are adhered to.
Oversize fillet welds (welds with a throat larger than required by the design)
Fig.4. Oversize fillet weld
As discussed in Job Knowledge 66, oversize fillet welds can represent a significant additional cost and loss of productivity.
Common causes
There are some welding related causes, eg high welding current, slow travel speeds, and some supervision related (eg 'to be safe make this fillet bigger by x mm').
Acceptance
BS EN ISO 5817 has limits related to the actual throat (eg for stringent quality levels, the actual weld throat [a] may exceed the nominal (design) weld throat [h] by 1+0.15a with a maximum of 3mm. For the moderate quality level (D) the excessive throat thickness is unlimited.
Avoidance
Adhere to the specified welding procedure and parameters and do not add to the specified weld size. Where possible mechanise the welding operation.
Undersized fillet welds (fillet welds smaller than those specified)
Fig.5. Undersized fillet weld
Common causes
The welding related causes are associated with high welding speeds and low welding currents.
Acceptance
Therefore, it is normally assumed that fillet welds will be at least of the size specified. BS EN SIO 5817 states that limits to insufficient throat thickness are not applicable to processes with proof of greater depth of penetration, therefore a fillet weld with an apparent throat thickness smaller that that prescribed should not be regarded as being imperfect if the actual throat thickness with a compensating greater depth of penetration complies with the nominal value. That is if we can be sure there is good penetration the smaller fillet may be acceptable, however, this should be discussed with the designer of the fabrication. The limits set by the standard.
Relying upon deep penetration to provide the required minimum design throat thickness can be difficult to justify. Penetration is a weld characteristic that is hard to measure directly and reliance must be placed on the stringent control of both the welding process and the welder. Manual welding can rarely be relied upon to provide the required consistency but it is an option with mechanised welding systems.
Imperfection: fillet weld having a throat thickness smaller than the nominal value | Quality levels |
Moderate D |
Intermediate C |
Stringent B |
Long imperfections NOT permitted |
NOT permitted |
Short imperfections (see Fig.5) h ≤ 0.3mm+ 0.1 a |
|
max 2mm |
max 1mm |
|
Avoidance
Adhere to the specified welding procedure and parameters. Use sufficient current and appropriate travel speed. Where possible mechanise the welding operation.
Asymmetric fillet weld (a fillet weld where the legs are of unequal length)
Fig.6. Asymmetric fillet weld
Common causes
Due to incorrect electrode positioning or to gravity pulling the molten pool towards one face of the joint. It is an mainly a problem with fillet welds made in the horizontal/vertical (PB) position.
Acceptance
There are instances where asymmetry may be specified (eg to place the toe stress concentration in a particular region).
BS EN ISO 5817 would, for a 10mm leg length fillet weld (ie 7.1mm throat) allow a difference in leg lengths of about 2.5mm at the stringent quality level and 3.4mm at the moderate quality level. Acceptance is related to the throat thickness.
The consequence of this imperfection is a significant increase in weld volume. Provided the leg length requirement is achieved there would not be a loss of strength. Perhaps this is why, in other standards, a requirement is not specified and the acceptability is left to the inspection personnel to make the 'engineering judgement'!
Poor fit-up
The most common imperfection is an excessive gap between the mating faces of the materials.
Common causes
Poor workshop practice, poor dimensioning and tolerance dimensions on drawings.
Acceptance
A major problem with fillet welds is ensuring the gap between the components is within defined limits. BS EN ISO 5817 specifies the acceptance criteria as follows:
Quality levels |
Moderate D |
Intermediate C |
Stringent B |
h ≤ 1mm + 0.3 a |
h ≤ 0.5mm + 0.2 a |
h ≤ 0.5mm + 0.1 a |
max 4mm |
max 3mm |
max 2mm |
Where h = fit-up gap and a = fillet weld design throat |
Figure 7 shows that the gap results in a reduction in the leg length on the vertical plate and this, in turn, results in a reduction in the throat thickness of the joint. A 10mm leg length fillet with a root gap of 3mm gives an effective leg of 7mm (a throat of 4.9mm instead of the expected 7mm).
When the application of BS EN ISO 5817 is not required, the guidance of BS EN 1011-2 can be followed, which recommends a maximum gap of 3mm. This standard also states that the size of the fillet weld can be increased to compensate for a large gap.
This discrepancy is addressed within AWS D1.1. which permits a root gap of up to 5mm for material thickness up to 75mm. However, 'if the (joint) separation is greater than 2mm the leg of the fillet weld shall be increased by the amount of the root opening, or the contractor shall demonstrate that the effective throat has been obtained'.
This Job Knowledge article was originally published in Connect, January 2004. It has been updated so the web page no longer reflects exactly the printed version.